Festo ELCC-TB-KF-110-200-0H-P0-CR Bruksanvisning
Festo
Inte kategoriserad
ELCC-TB-KF-110-200-0H-P0-CR
Läs nedan 📖 manual på svenska för Festo ELCC-TB-KF-110-200-0H-P0-CR (30 sidor) i kategorin Inte kategoriserad. Denna guide var användbar för 8 personer och betygsatt med 4.5 stjärnor i genomsnitt av 2 användare
Sida 1/30
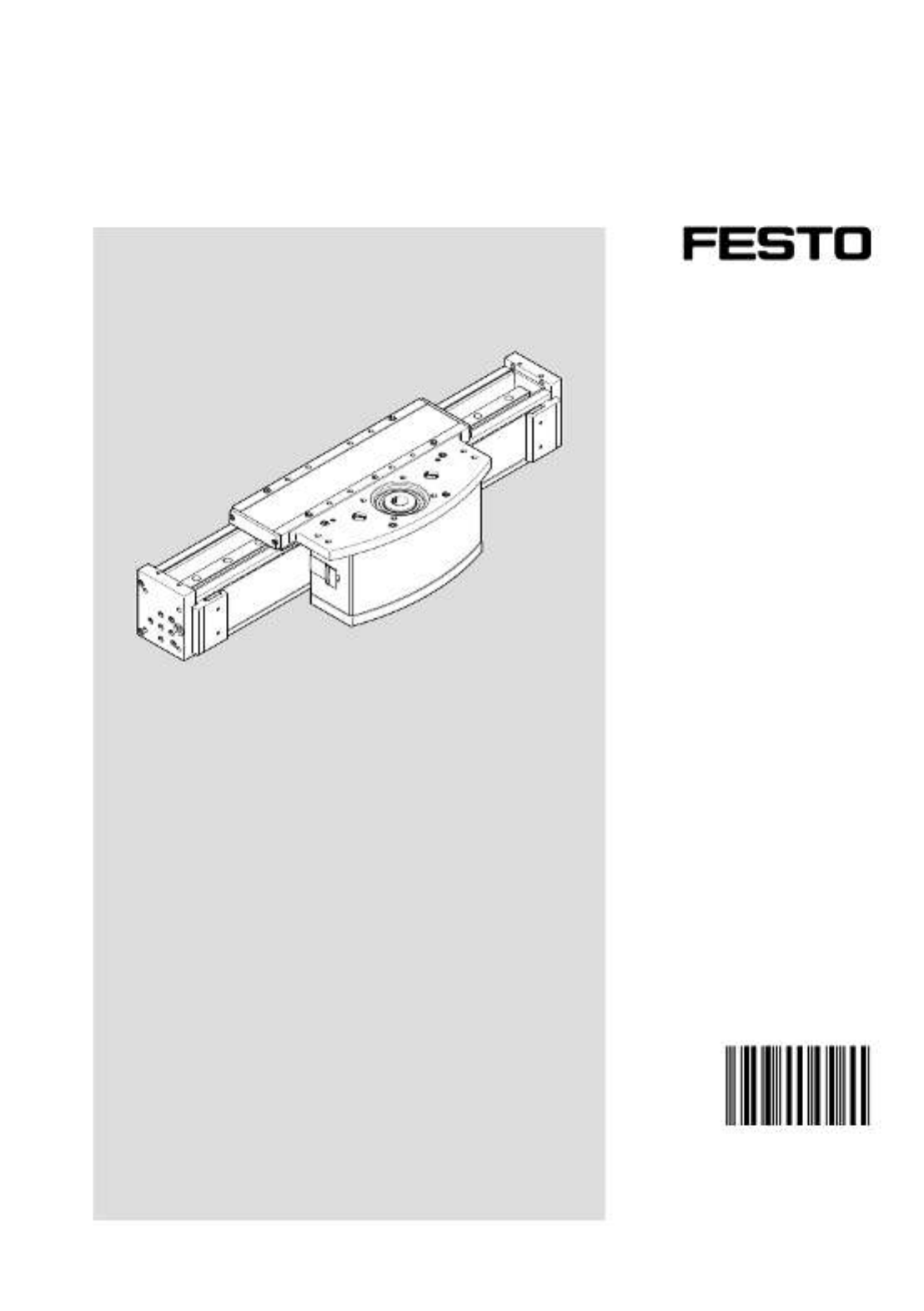
ELCC-TB
Cantilever axis
Operating instruc-
tion
8178817
8178817
2023-05c
[8178819]
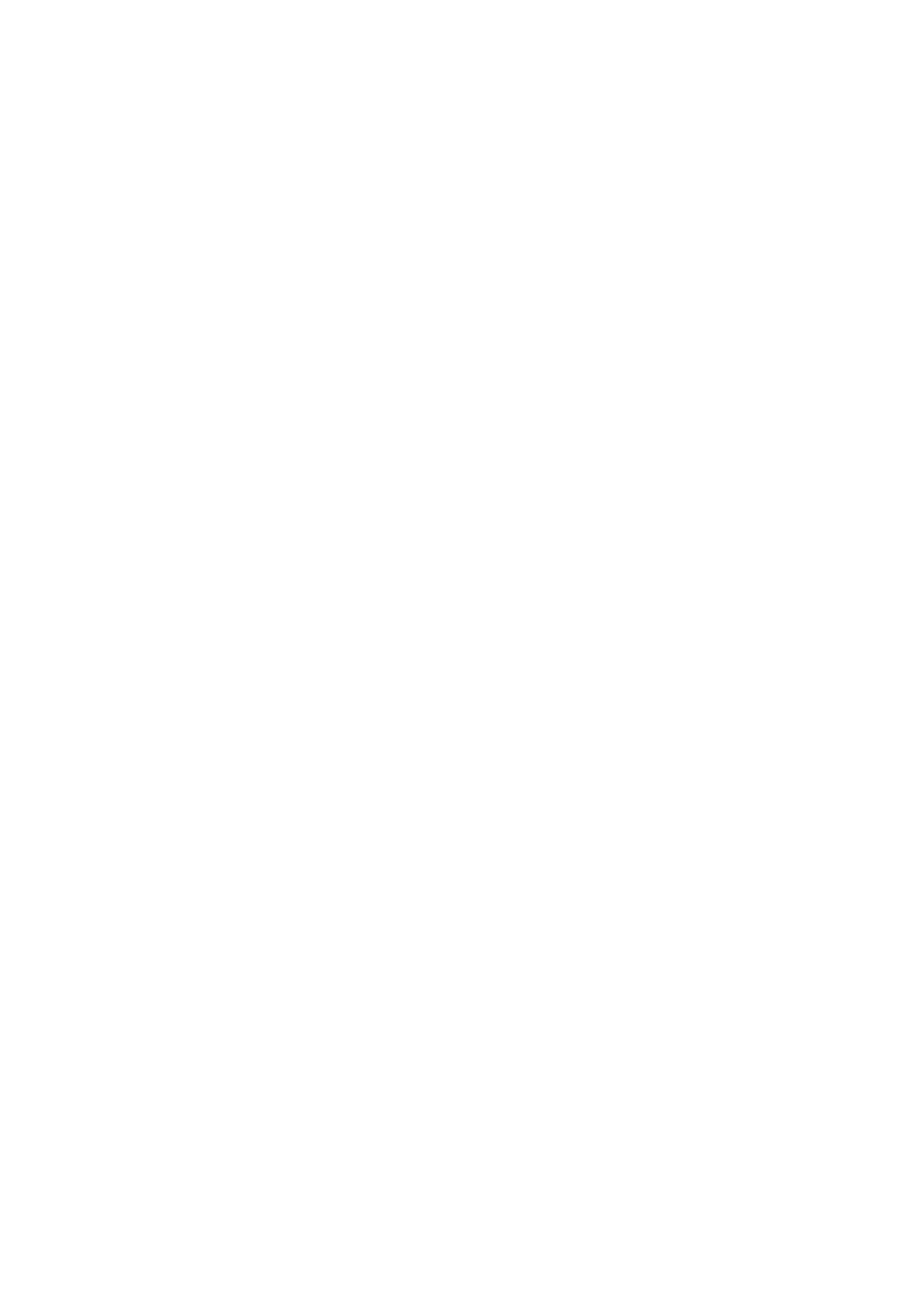
Translation of the original instructions
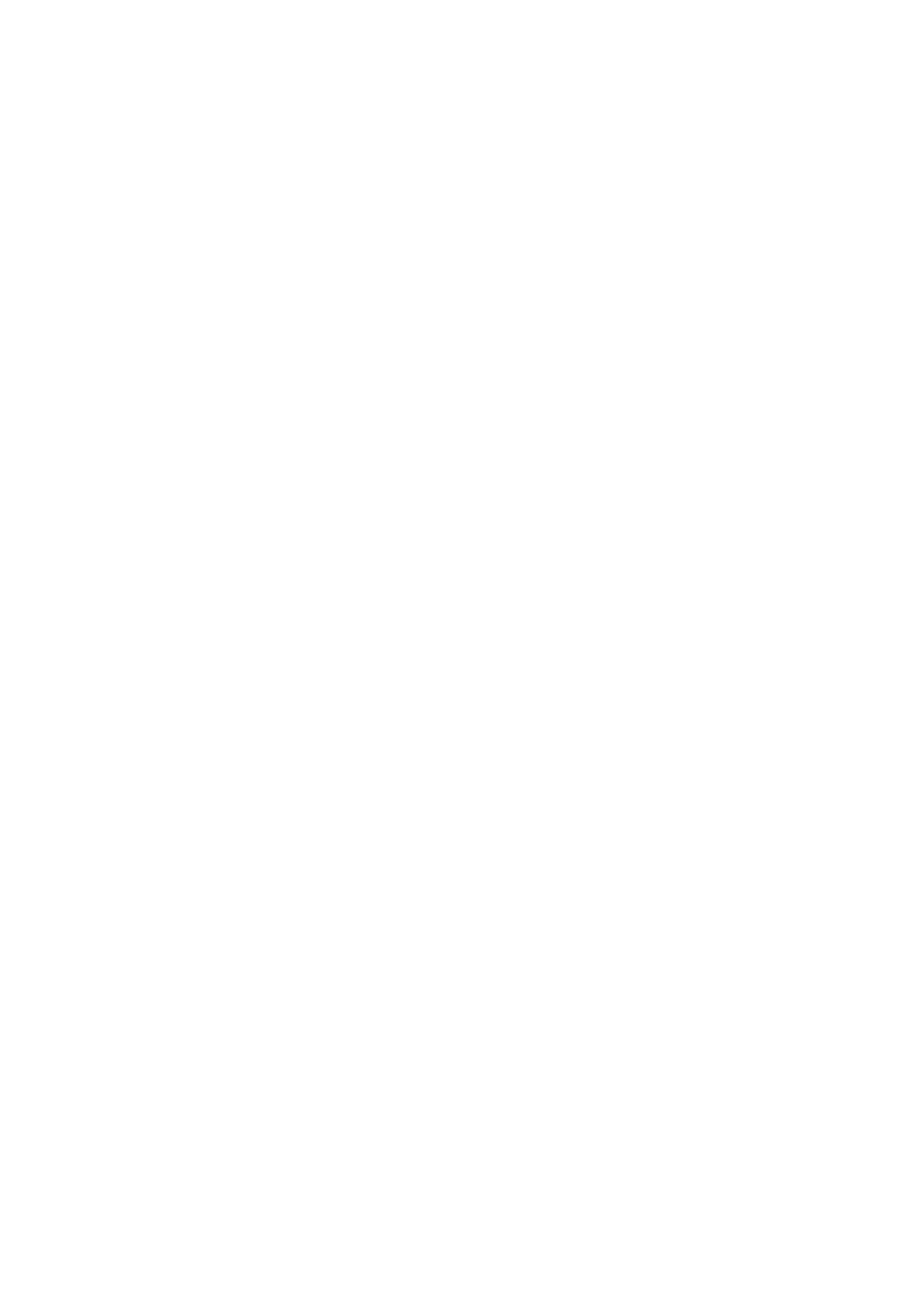
Festo — ELCC-TB — 2023-05c
3
Table of contents
1 Applicable documents. . . . . . . . . . . . . . . . . . . . . . . . . . . . . . . . . . . . . . . . . . . . . . . . . . . . . . . . . . . . 4
2 Safety. . . . . . . . . . . . . . . . . . . . . . . . . . . . . . . . . . . . . . . . . . . . . . . . . . . . . . . . . . . . . . . . . . . . . . . . . . 4
2.1 Safety instructions. . . . . . . . . . . . . . . . . . . . . . . . . . . . . . . . . . . . . . . . . . . . . . . . . . . . . . . . . . 4
2.2 Intended use. . . . . . . . . . . . . . . . . . . . . . . . . . . . . . . . . . . . . . . . . . . . . . . . . . . . . . . . . . . . . . 4
2.3 Training of qualified personnel. . . . . . . . . . . . . . . . . . . . . . . . . . . . . . . . . . . . . . . . . . . . . . . . 4
3 Additional information. . . . . . . . . . . . . . . . . . . . . . . . . . . . . . . . . . . . . . . . . . . . . . . . . . . . . . . . . . . . 4
4 Product overview . . . . . . . . . . . . . . . . . . . . . . . . . . . . . . . . . . . . . . . . . . . . . . . . . . . . . . . . . . . . . . . . 5
4.1 Product design. . . . . . . . . . . . . . . . . . . . . . . . . . . . . . . . . . . . . . . . . . . . . . . . . . . . . . . . . . . . . 5
4.2 Function. . . . . . . . . . . . . . . . . . . . . . . . . . . . . . . . . . . . . . . . . . . . . . . . . . . . . . . . . . . . . . . . . . 6
5 Transport. . . . . . . . . . . . . . . . . . . . . . . . . . . . . . . . . . . . . . . . . . . . . . . . . . . . . . . . . . . . . . . . . . . . . . . 6
6 Assembly. . . . . . . . . . . . . . . . . . . . . . . . . . . . . . . . . . . . . . . . . . . . . . . . . . . . . . . . . . . . . . . . . . . . . . . 6
6.1 Safety. . . . . . . . . . . . . . . . . . . . . . . . . . . . . . . . . . . . . . . . . . . . . . . . . . . . . . . . . . . . . . . . . . . . 6
6.2 Mounting motor. . . . . . . . . . . . . . . . . . . . . . . . . . . . . . . . . . . . . . . . . . . . . . . . . . . . . . . . . . . . 6
6.3 Mounting axis. . . . . . . . . . . . . . . . . . . . . . . . . . . . . . . . . . . . . . . . . . . . . . . . . . . . . . . . . . . . . . 7
6.4 Mounting payload on the standard slide. . . . . . . . . . . . . . . . . . . . . . . . . . . . . . . . . . . . . . . . 8
6.5 Mounting payload on the additional slide . . . . . . . . . . . . . . . . . . . . . . . . . . . . . . . . . . . . . . 10
6.6 Mounting end position protection. . . . . . . . . . . . . . . . . . . . . . . . . . . . . . . . . . . . . . . . . . . . 12
6.7 Mounting sensor. . . . . . . . . . . . . . . . . . . . . . . . . . . . . . . . . . . . . . . . . . . . . . . . . . . . . . . . . . 13
6.8 Connecting sealing air or clamping unit. . . . . . . . . . . . . . . . . . . . . . . . . . . . . . . . . . . . . . . 14
7 Commissioning. . . . . . . . . . . . . . . . . . . . . . . . . . . . . . . . . . . . . . . . . . . . . . . . . . . . . . . . . . . . . . . . . 15
8 Maintenance. . . . . . . . . . . . . . . . . . . . . . . . . . . . . . . . . . . . . . . . . . . . . . . . . . . . . . . . . . . . . . . . . . . 16
8.1 Safety. . . . . . . . . . . . . . . . . . . . . . . . . . . . . . . . . . . . . . . . . . . . . . . . . . . . . . . . . . . . . . . . . . . 16
8.2 Checking toothed belt wear. . . . . . . . . . . . . . . . . . . . . . . . . . . . . . . . . . . . . . . . . . . . . . . . . 16
8.3 Checking cover strip. . . . . . . . . . . . . . . . . . . . . . . . . . . . . . . . . . . . . . . . . . . . . . . . . . . . . . . 16
8.4 Checking clamping unit. . . . . . . . . . . . . . . . . . . . . . . . . . . . . . . . . . . . . . . . . . . . . . . . . . . . . 17
8.5 Cleaning axis. . . . . . . . . . . . . . . . . . . . . . . . . . . . . . . . . . . . . . . . . . . . . . . . . . . . . . . . . . . . . 17
8.6 Lubricating axis. . . . . . . . . . . . . . . . . . . . . . . . . . . . . . . . . . . . . . . . . . . . . . . . . . . . . . . . . . . 18
9 Fault clearance. . . . . . . . . . . . . . . . . . . . . . . . . . . . . . . . . . . . . . . . . . . . . . . . . . . . . . . . . . . . . . . . . 19
10 Technical data. . . . . . . . . . . . . . . . . . . . . . . . . . . . . . . . . . . . . . . . . . . . . . . . . . . . . . . . . . . . . . . . . . 22
10.1 Technical data, mechanical. . . . . . . . . . . . . . . . . . . . . . . . . . . . . . . . . . . . . . . . . . . . . . . . . . 22
10.2 Characteristic curves of deflection. . . . . . . . . . . . . . . . . . . . . . . . . . . . . . . . . . . . . . . . . . . . 24
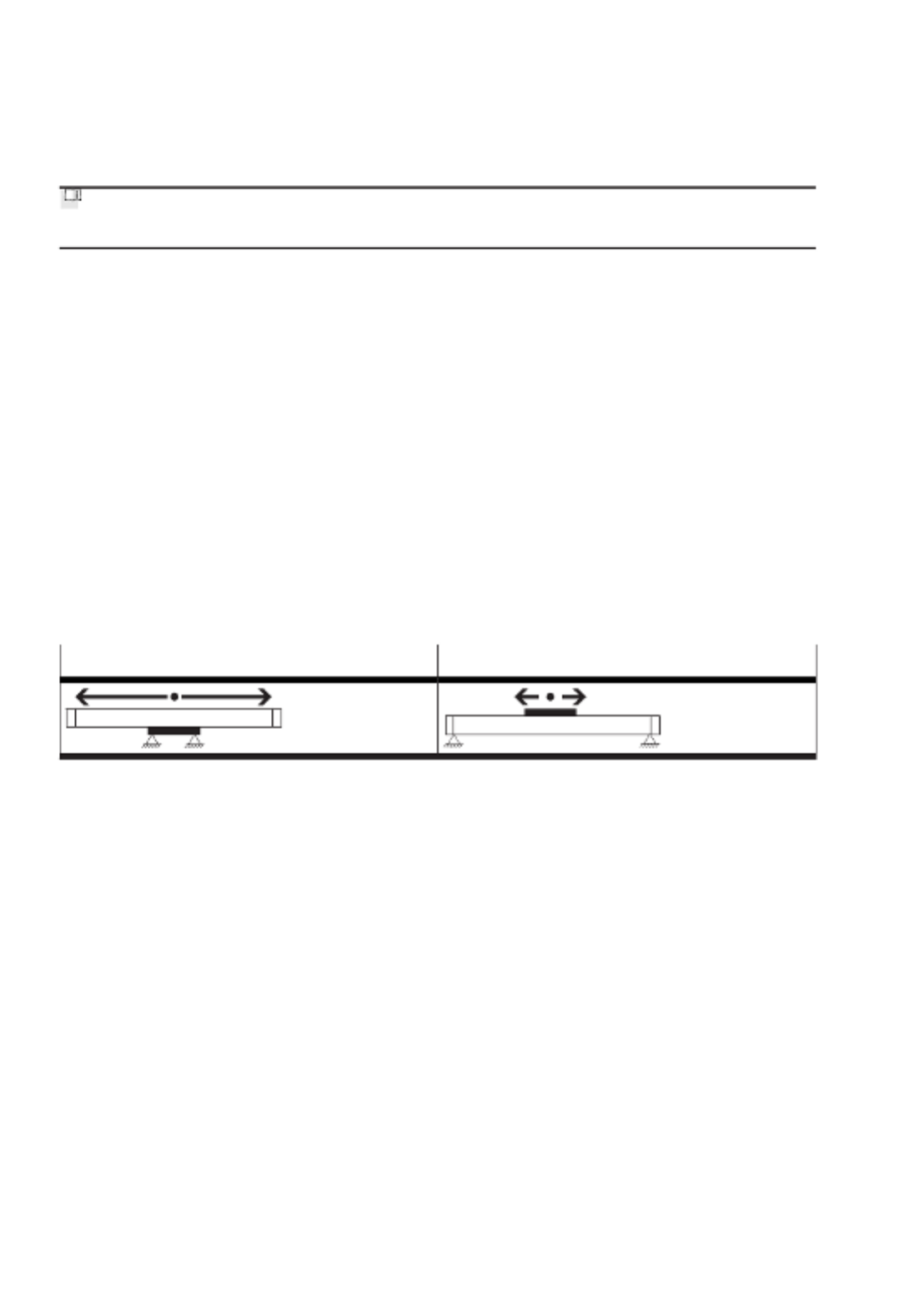
4
Festo — ELCC-TB — 2023-05c
Additional information
1 Applicable documents
All available documents for the product
èwww.festo.com/sp.
2 Safety
2.1 Safety instructions
–Observe the identifications on the product.
–Only use the product if it is in perfect technical condition.
–Before working on the product: Switch off the power supply, ensure that it is off and secure it
against being switched on again.
–Store the product in a cool, dry environment protected from UV and corrosion. Keep storage times
short.
–Store the product in ambient conditions without oils, greases and grease-dissolving vapours.
2.2 Intended use
The axis positions payloads or moves external guides.
The attached clamping unit ELCC-...-C holds payloads in all mounting positions.
The axis is approved for cantilever operation and slide operation.
Cantilever operation Slide operation
Tab. 1: Operating modes
2.3 Training of qualified personnel
Work on the product may only be carried out by qualified personnel who can evaluate the work and
detect dangers. The qualified personnel have knowledge and experience in dealing with electric drive
systems.
3 Additional information
–Contact the regional Festo contact if you have technical problems
èwww.festo.com.
–Accessories and spare parts èwww.festo.com/catalogue.
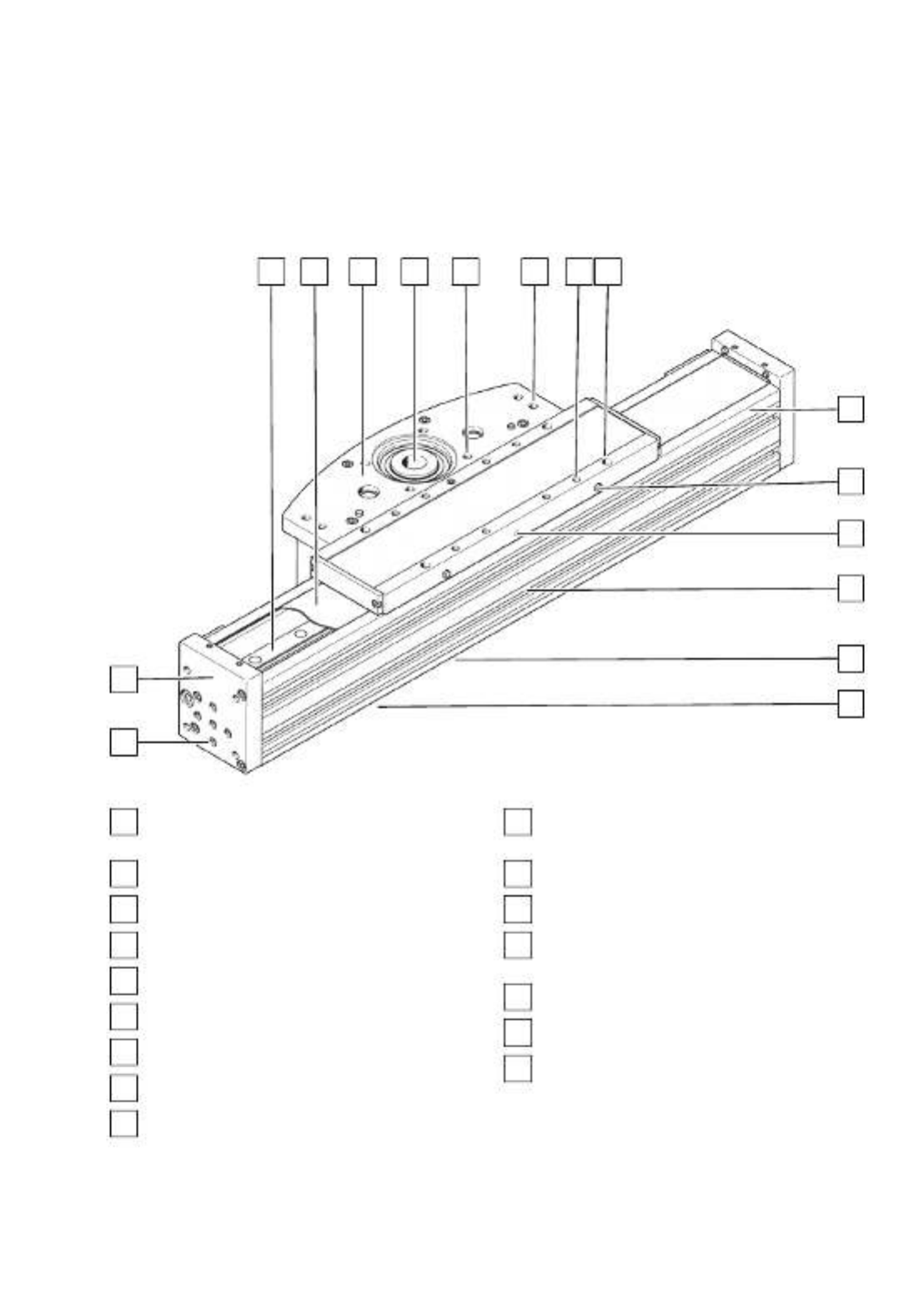
Festo — ELCC-TB — 2023-05c
Product overview
5
4 Product overview
4.1 Product design
Product design ELCC-TB
1
2
3 4 5 6 7 8 9 10
11
12
13
14
15
16
Fig. 1: Product design ELCC-TB
1
Threaded hole and centring hole for pay-
load
2
End cap
3
Guide rail
4
Cover strip
5
Drive head
6
Hollow drive shaft
7
Threaded hole for motor mounting kit
8
Threaded hole for shock absorber stop
9
Threaded hole for direct fastening or
threaded hole and centring hole for payload
10
Threaded hole and centring hole for direct
fastening or payload
11
Cantilever profile
12
Guide lubrication point
13
Threaded hole for clamping unit connection
or sealing air connection
14
Slot for slot nut
15
Threaded hole for sensor bracket
16
Slot for slot nut, payload and switch lug
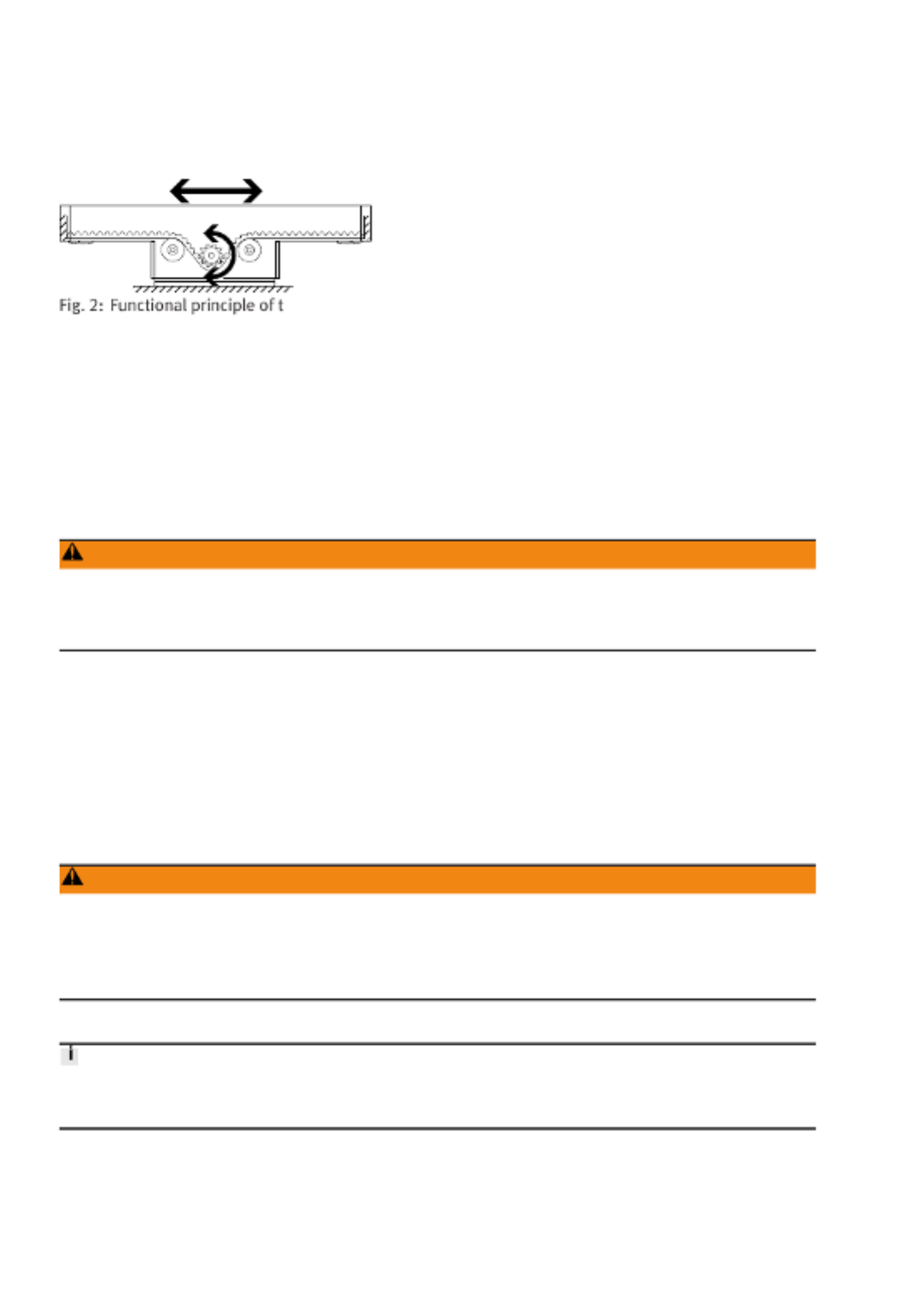
6
Festo — ELCC-TB — 2023-05c
Assembly
4.2 Function
Fig. 2: Functional principle of toothed belt drive with fixed toothed belt
The axis converts the rotary motion of the mounted motor into a linear motion of the cantilever or
slide. The toothed belt drive converts the torque of the motor into a feed force. The linear movement
of the cantilever or slide is accurately guided by the guide. The integrated cover strip prevents abraded
particles from penetrating the immediate vicinity of the drive. The clamping unit is used for holding
loads at standstill or for emergency braking in the event of a power failure. Sensors and displacement
encoder enable query of end positions, reference position and intermediate position.
5 Transport
WARNING
Risk of injury due to falling product
If the product is lifted incorrectly, it may fall and cut, crush or separate body parts.
• Lift the product only with suitable load-bearing equipment.
–Store and transport the product in its original packaging. Observe the weight, the dimensions and
the ambient conditions.
–Take the centre of gravity of the product into consideration.
–Store and transport the product in a horizontal position.
6 Assembly
6.1 Safety
WARNING
Risk of Injury due to Unexpected Movement of Components
For vertical or slanted mounting position: when power is off, moving parts can travel or fall uncon-
trolled into the lower end position.
• Bring moving parts of the product into a safe end position or secure them against falling.
6.2 Mounting motor
Observe the limit values for forces, torques and speeds if a non-recommended motor and motor
mounting kit are used.
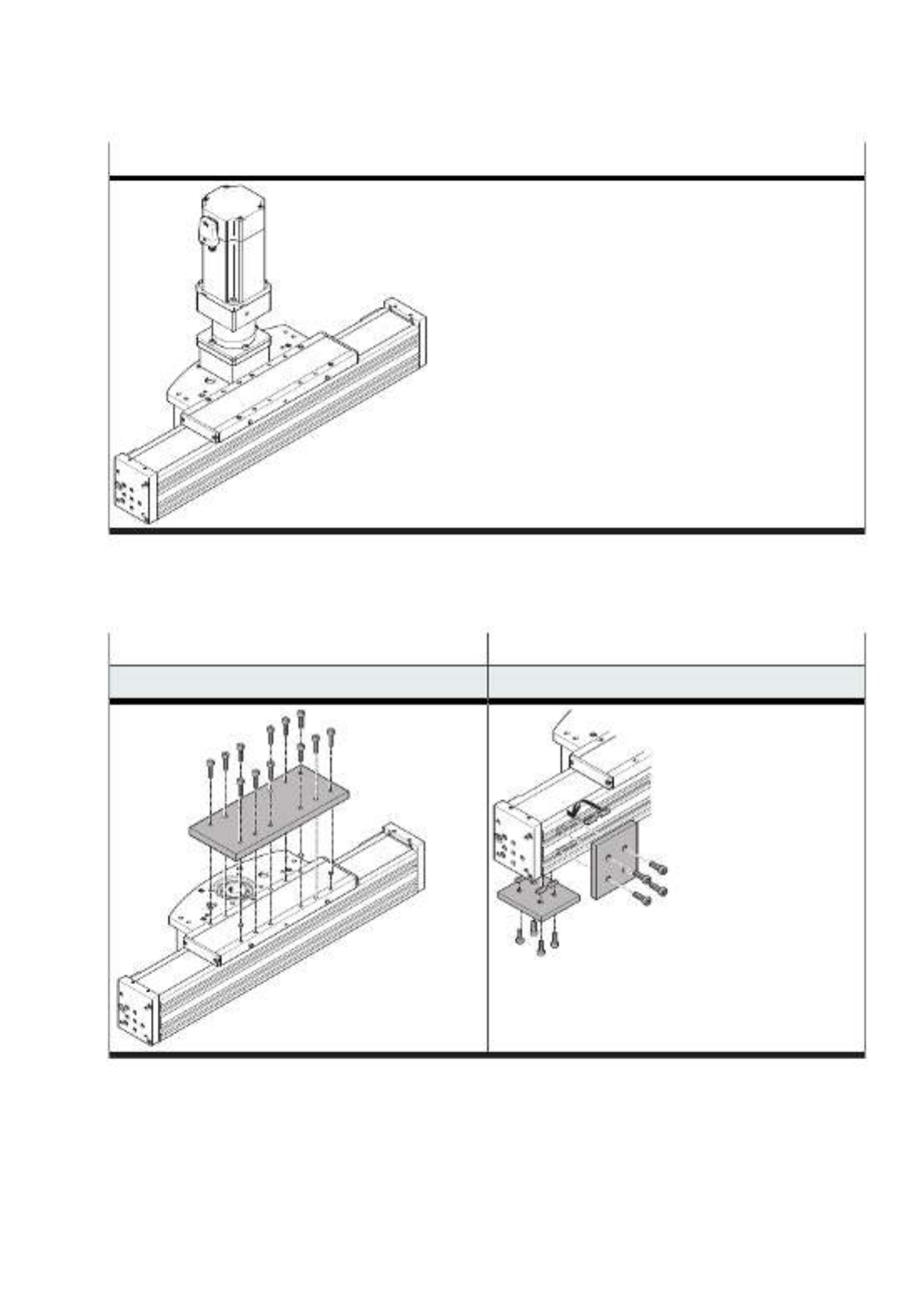
Festo — ELCC-TB — 2023-05c
Assembly
7
Axial kit EAMM-A
Tab. 2: Overview of mounting motors
• Mount the motor and motor mounting kit without tension.
6.3 Mounting axis
Cantilever operation Slide operation
Direct fastening on slide Slot nut NST
Tab. 3: Overview of mounting components
Requirements:
–Adequate clearance for payload to avoid collisions with motor, mounting components and sensor
components.
–Sufficient space for maintenance work.
–A mounting surface flatness of 0.01mm above the slide surface.
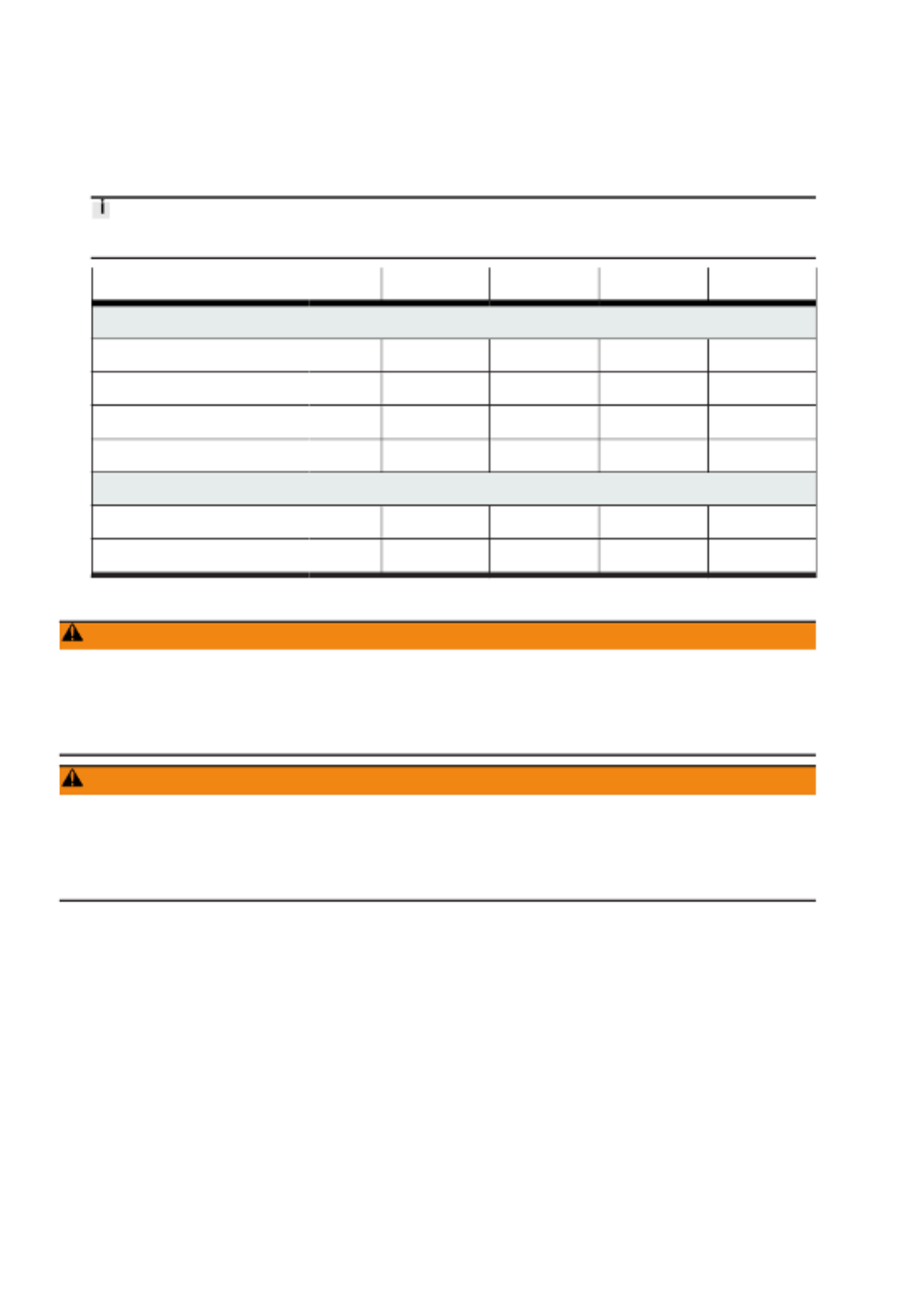
8
Festo — ELCC-TB — 2023-05c
Assembly
1. Place the mounting components on the support points.
2. Tighten the screws. Observe the maximum tightening torque and maximum screw-in depth.
When used in multi-axis systems: align to the first axis and install without tension.
ELCC-TB-... -60 -70 -90 -110
Direct fastening on slide
Thread M5 M5 M6 M6
Max. tightening torque [Nm] 6 6 10 24
Max. screw-in depth tmax [mm] 10 10 12 16.2
Centring element [mm] 5 H7 9 H7 9 H7 12 H7Æ Æ Æ Æ
Slot nut NST
Thread M5 M5 M6 M6
Max. screw-in depth tmax [mm] 6 6 12 12
6.4 Mounting payload on the standard slide
WARNING
Unexpected movement of components.
Injury due to impacts or crushing.
• Before working on the product, switch off the control and secure it to prevent it from being switched
back on accidentally.
WARNING
Risk of Injury due to Unexpected Movement of Components
For vertical or slanted mounting position: when power is off, moving parts can travel or fall uncon-
trolled into the lower end position.
• Bring moving parts of the product into a safe end position or secure them against falling.
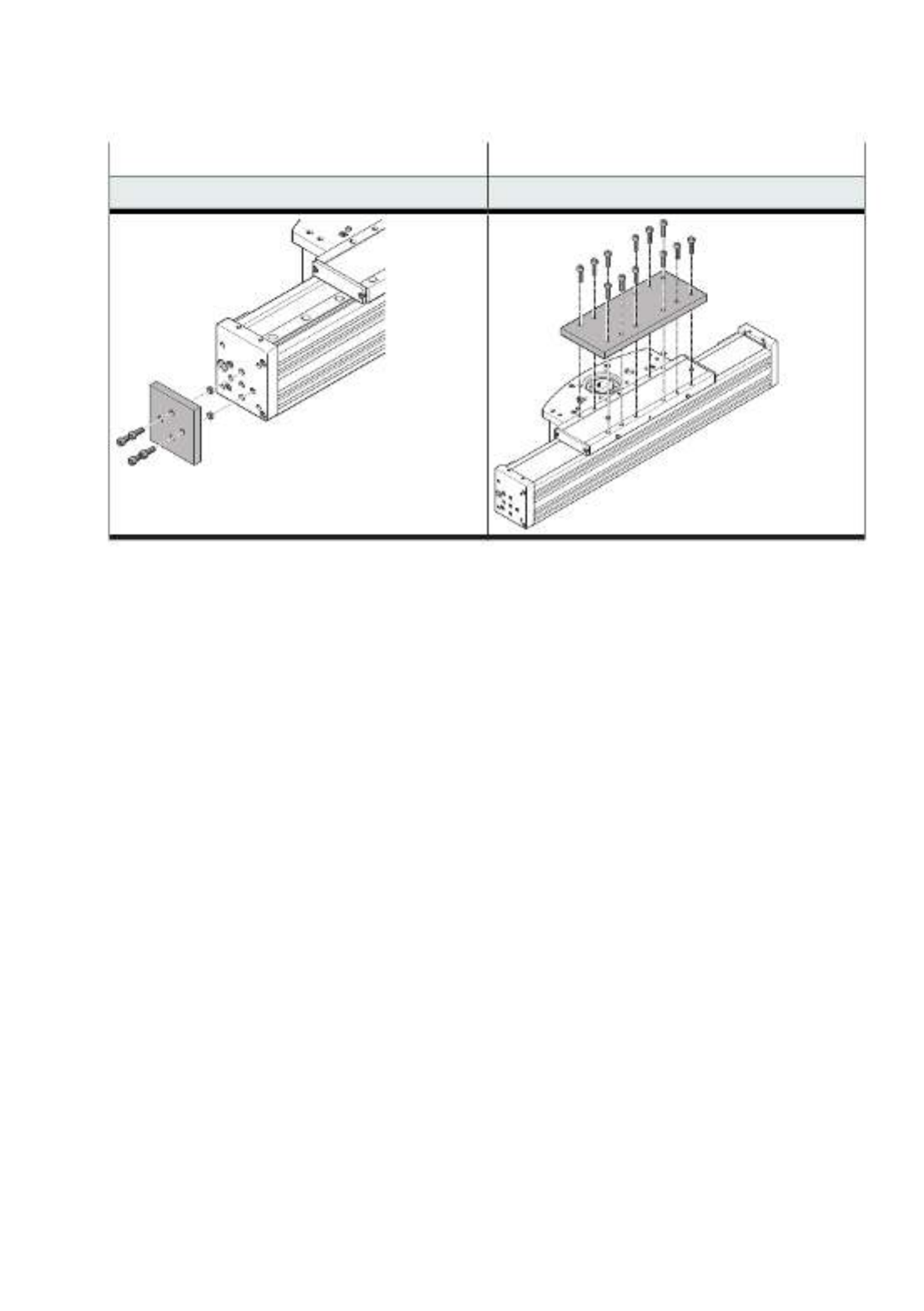
Festo — ELCC-TB — 2023-05c
Assembly
9
Cantilever operation Slide operation
Direct fastening on end cap Direct fastening on slide
Tab. 4: Mounting payload overview
Requirements:
–Adequate clearance for payload to avoid collisions with motor, mounting components and sensor
components.
–Sufficient space for maintenance work.
–A payload mounting surface flatness of 0.01mm above the slide surface.
–Minimise the guide load. Short lever arms from the guide centre to the force application points and
centres of gravity of the payload.
1. Place centring components in the centring holes.
2. Position the payload at the intended location.
–For cantilever operation position the payload on the end cap or place it on the profile.
–For slide operation position the payload on the slide. In the delivery status the centring ele-
ments are placed in centring holes.
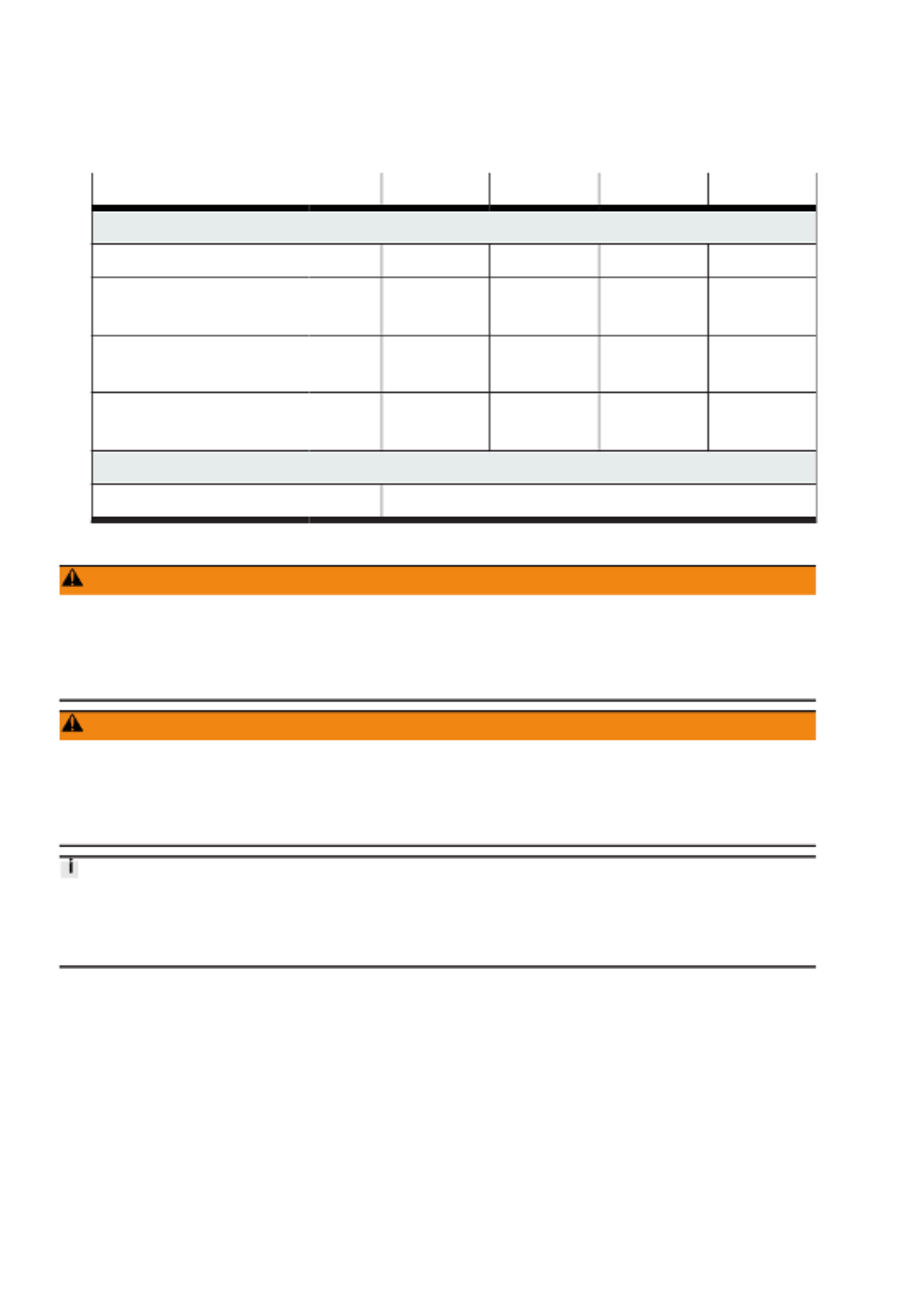
10
Festo — ELCC-TB — 2023-05c
Assembly
3. Tighten the screws. Observe the maximum tightening torque and maximum screw-in depth.
ELCC-TB-... -60 -70 -90 -110
Direct fastening on end cap
Thread, inside/outside M4 M4/M5/M6 M6/M8 M6/M8
Max. tightening torque,
inside/outside
[Nm] 3 3/6/10 10/18 10/18
Max. screw-in depth tmax,
inside/outside
[mm] 14 14/15/18 18 18
Centring element, inside/
outside
[mm] 7 H7 7 H7/ 9Æ Æ Æ
H7
Æ Æ 9 H7 9 H7
Direct fastening on slide
Thread è6.3 Mounting axis
6.5 Mounting payload on the additional slide
WARNING
Unexpected movement of components.
Injury due to impacts or crushing.
• Before working on the product, switch off the control and secure it to prevent it from being switched
back on accidentally.
WARNING
Risk of Injury due to Unexpected Movement of Components
For vertical or slanted mounting position: when power is off, moving parts can travel or fall uncon-
trolled into the lower end position.
• Bring moving parts of the product into a safe end position or secure them against falling.
• When using an additional external guide, ensure that the axes and guide are precisely parallel and
aligned.
• Recommendation: use guide mountings with tolerance compensation.
Tension due to manufacturing tolerances may be encountered with axes with additional slides when
mounting an adapter plate supplied by the customer.
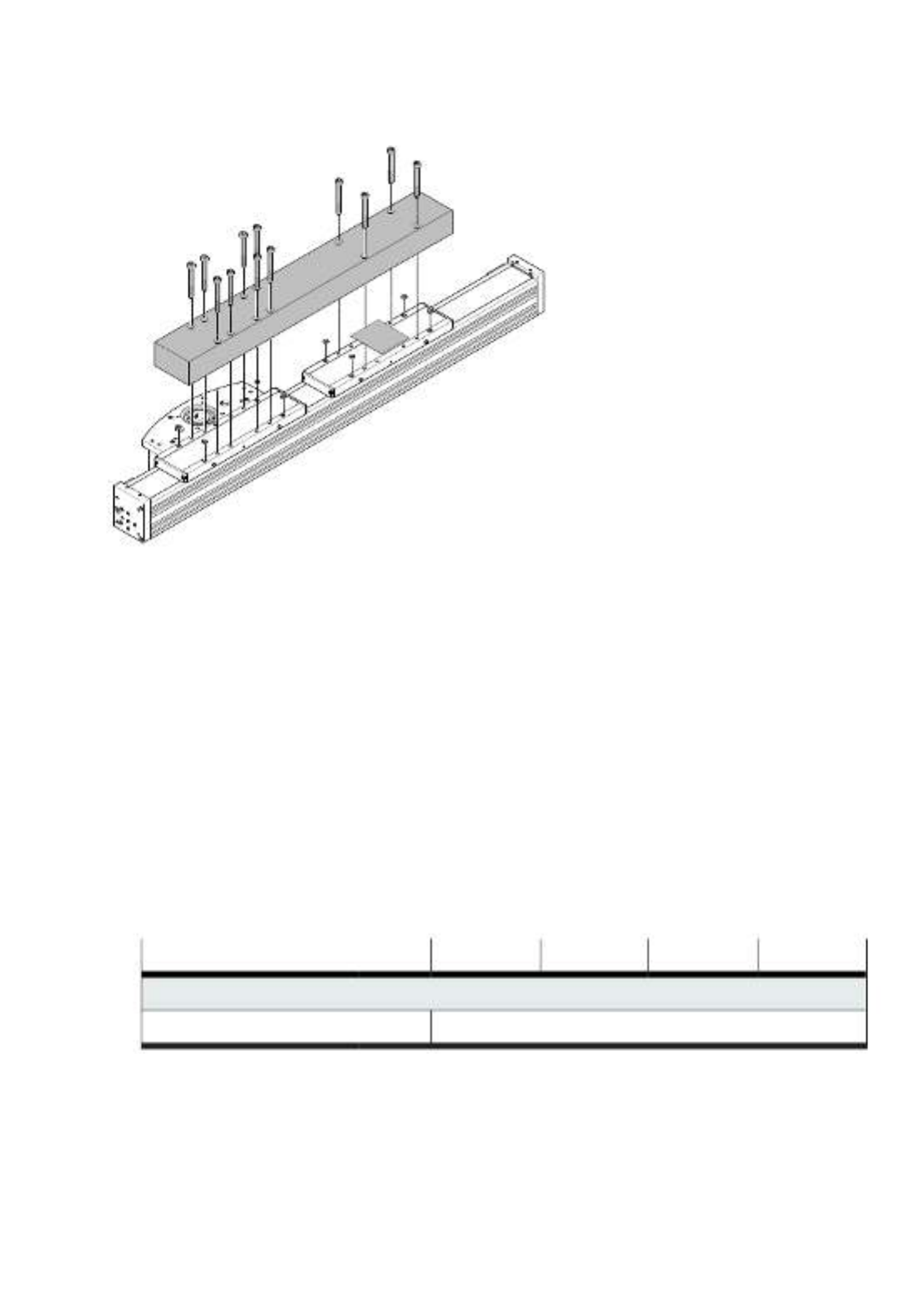
Festo — ELCC-TB — 2023-05c
Assembly
11
Fig. 3: Mounting payload, example "top mounting"
Requirements:
–A fixed-floating bearing for the carriage connection.
–Use a tolerance compensation in case of height deviation from the standard slide surface.
–Adequate clearance for payload to avoid collisions with motor, mounting components and sensor
components.
–Sufficient space for maintenance work.
–A payload mounting surface flatness of 0.01mm above the slide surfaces.
–Minimise the guide load. Short lever arms from the guide centre to the force application points and
centres of gravity of the payload.
1. Place centring components in the centring holes.
2. Mount the adapter plate on the standard slide.
3. Place the tolerance compensation elements on the additional slide.
4. Align and mount the adapter plate on the additional slide.
5. Tighten the screws. Observe the maximum tightening torque and maximum screw-in depth.
ELCC-TB-...-Z... -60 -70 -90 -110
Direct fastening on slide
Thread è6.3 Mounting axis
6. Check the running behaviour of the slides.
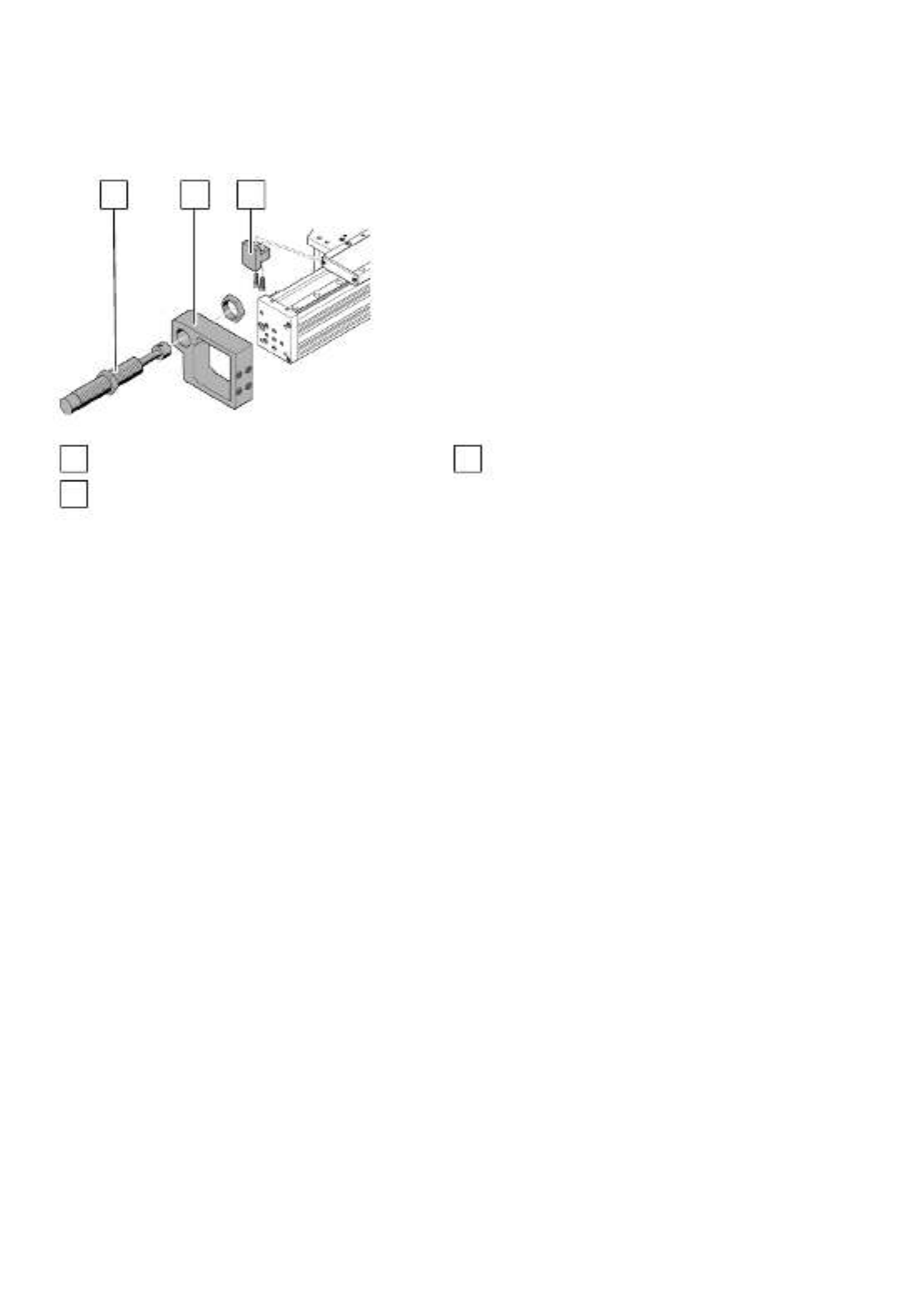
12
Festo — ELCC-TB — 2023-05c
Assembly
6.6 Mounting end position protection
1 2 3
Fig. 4: Mounting shock absorber stop, shock absorber retainer and shock absorber
1
Shock absorber
2
Shock absorber retainer
3
Shock absorber stop
1. Mount the shock absorber stop.
2. Mount the shock absorber retainer.
3. Mount the shock absorber.
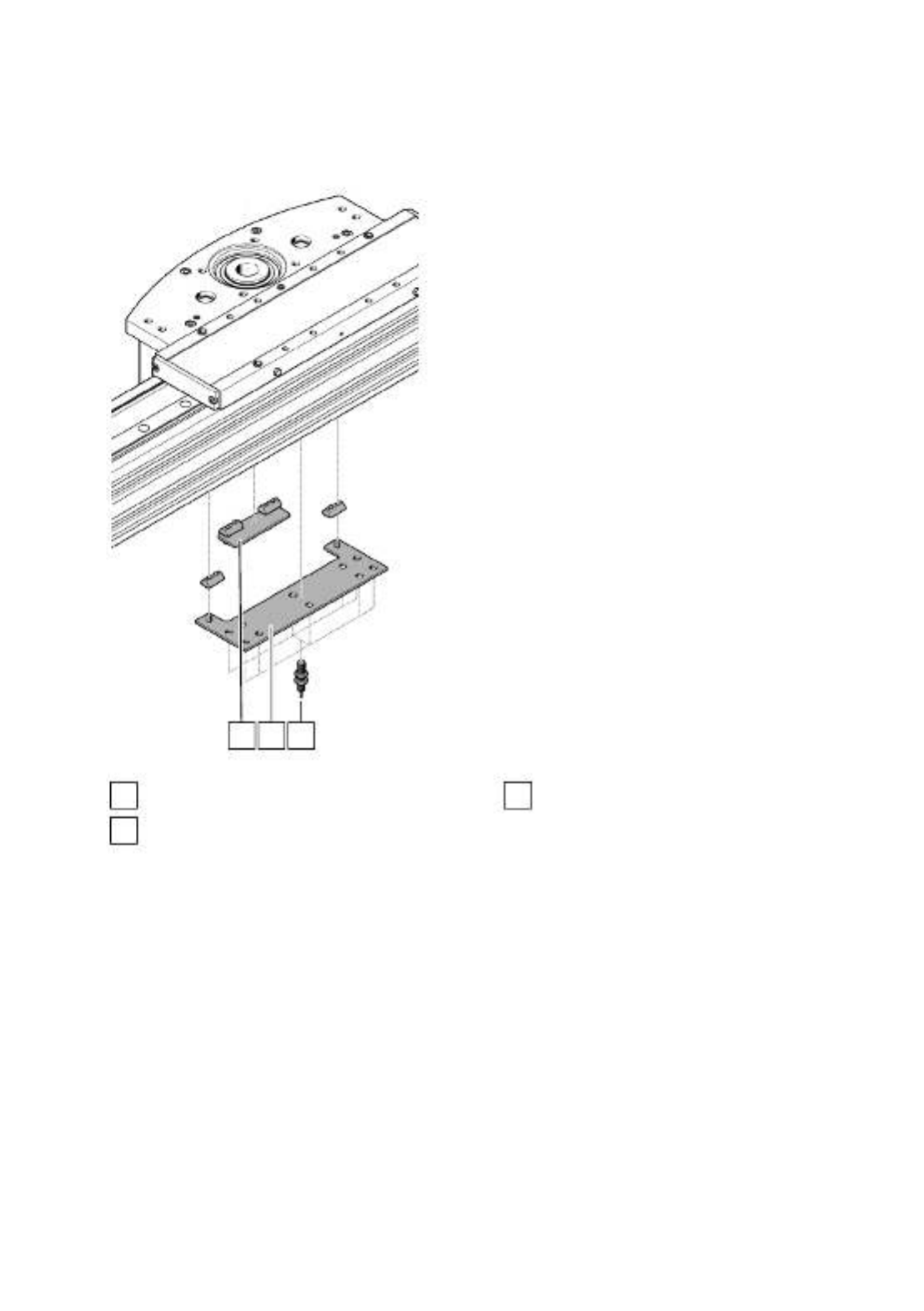
Festo — ELCC-TB — 2023-05c
Assembly
13
6.7 Mounting sensor
123
Fig. 5: Mounting switch lug, sensor and sensor bracket
1
Switch lug
2
Sensor bracket
3
Sensor
Requirements:
–Protect the sensor from external magnetic or ferritic influences with min. 10 mm distance from slot
nuts.
–Use a hardware limit switch with N/C contact function to guarantee protection in the event of a
sensor failure.
–Use an inductive sensor.
1. Mount the switch lug.
2. If necessary, mount the sensor bracket.
3. Mount the sensor.
4. If necessary, mount the cable with clips.
5. If necessary, mount the slot cover.
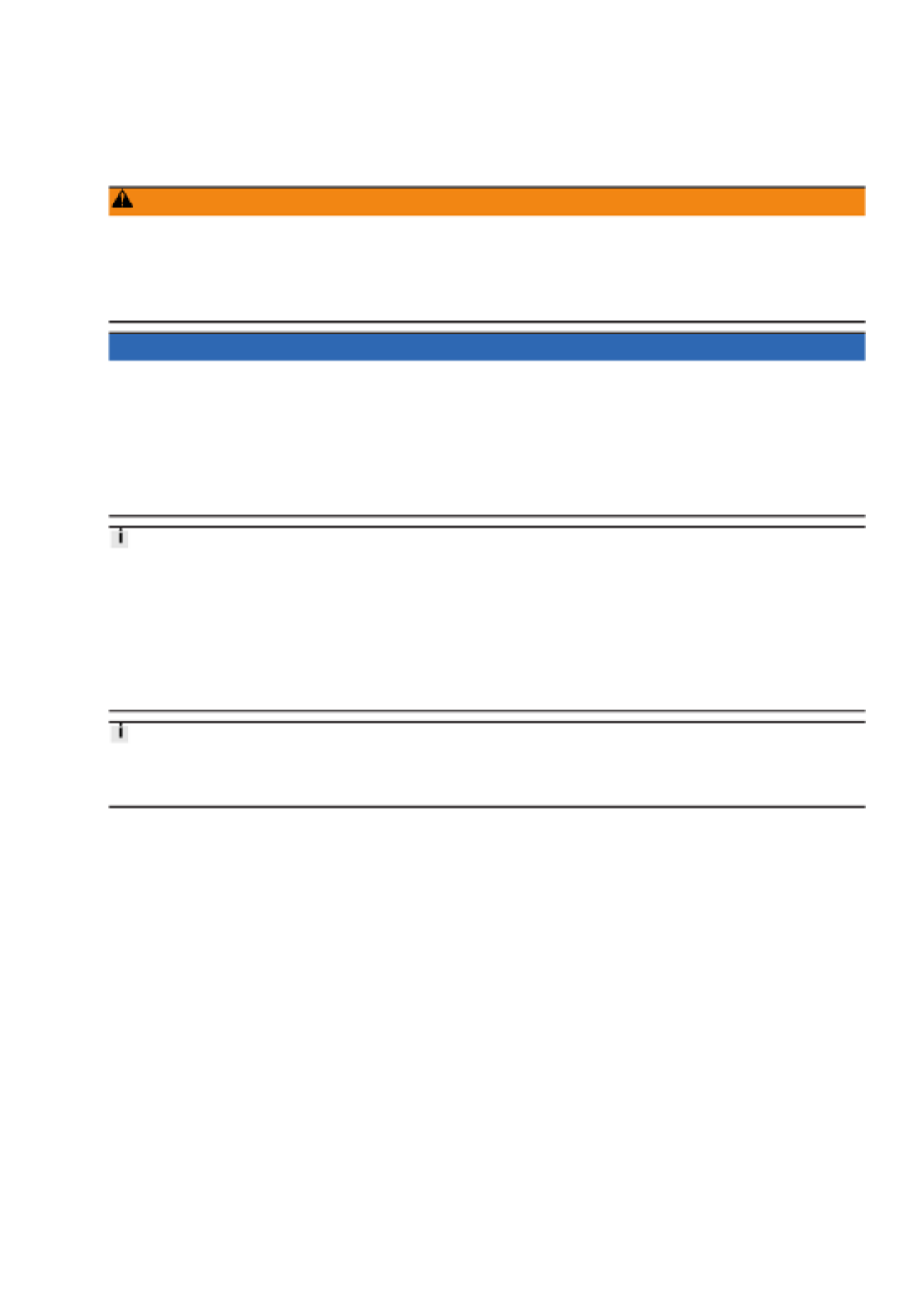
Festo — ELCC-TB — 2023-05c
Commissioning
15
7 Commissioning
WARNING
Risk of injury due to unexpected movement of components.
• Protect the positioning range from unwanted intervention.
• Keep foreign objects out of the positioning range.
• Perform commissioning with low dynamic response.
NOTICE
Elasticity of the toothed belt
The elasticity of the toothed belt generates an additional spring effect at high acceleration and
deceleration, which can lead to an inadmissible nominal/actual deviation when the slide is moved or
when the end position is reached.
• Consider the setpoint deviation determined during the test run during parameterisation of position
setpoint values.
Block-shaped acceleration profiles without jerk limitation can have the following effects:
• High mechanical loads on the lead screw due to high force peaks.
• Overshooting effects during positioning.
• Rise of the entire system.
Recommendation: reduce high force peaks in the acceleration and deceleration phases by using the
jerk limitation.
Identical axes can generate different running noises depending on the parameterisation, mode of
operation, type of mounting, installation environment and components.
Requirements:
–The motor encoder is referenced to the reference mark by a homing run.
–The motor encoder has the absolute reference to the reference mark.
–The direction of movement of the slide is determined by the direction of rotation of the motor.
–The mounting of the drive system has been checked.
–The protective cover of the cover strip is removed.
–The installation on the motor has been checked.
–There are no foreign objects in the movement space of the drive system.
–Maximum permissible feed force and drive torque as a function of acceleration, deceleration,
e.g.with stop function or quick stop, speed, moving mass and mounting position, are not exceeded.
–Axis is not mechanically overloaded and dynamic setpoint deviation is not exceeded as a result of
force peaks, torque peaks or overshoot effects, e.g.overrunning the end position.
Overloads and overruns as a result of jerk limitation must be restricted by reduced acceleration and
deceleration setpoints or optimised controller settings.
–The software end positions are not within the effective range of the mechanical stops.
–No homing or test run to mechanical end stops.
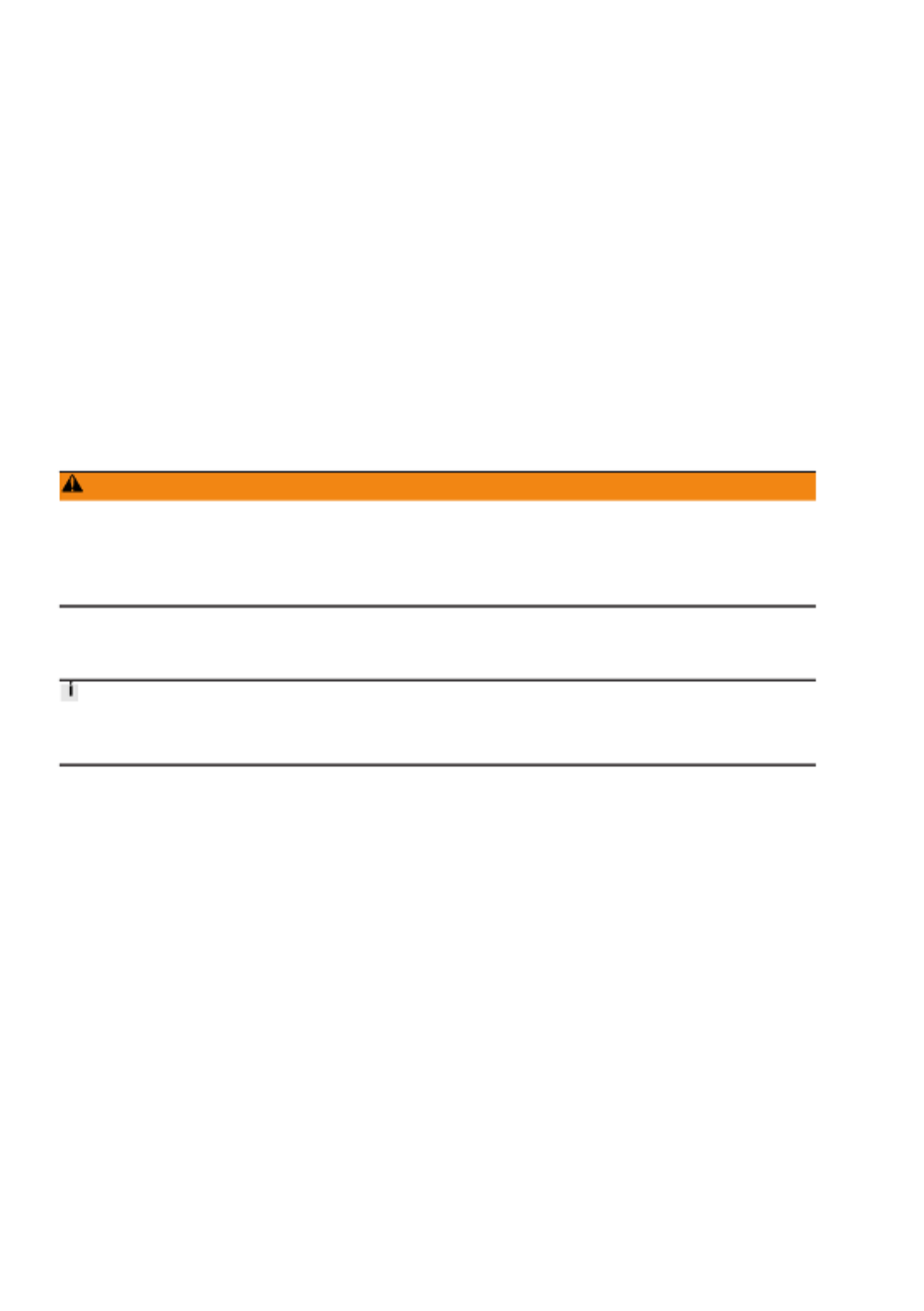
16
Festo — ELCC-TB — 2023-05c
Maintenance
1. Start check run.
2. Select permissible reference points "against reference switch" for the homing.
3. Start the homing run with reduced speed setpoints, acceleration setpoints and deceleration
setpoints.
4. Start the test run with reduced speed setpoints, acceleration setpoints and deceleration set-
points.
5. Check that the slide completes the entire travel cycle within the specified time.
ÄThe slide stops its travel when it reaches a limit switch and the drive system is ready for
operation.
8 Maintenance
8.1 Safety
WARNING
Unexpected movement of components.
Injury due to impacts or crushing.
• Before working on the product, switch off the control and secure it to prevent it from being switched
back on accidentally.
8.2 Checking toothed belt wear
Checking toothed belt wear
The toothed belt is tensioned for its entire service life.
The toothed belt must not be retensioned.
1. ELCC-...-PU1:
–Initial check: after 1000km.
–Periodic check: every 500km.
ELCC-...-CR/-PU2:
–Initial check: after 5000km.
–Periodic check: every 1000km.
2. If the toothed belt shows visible wear: send the axis to Festo or contact Festo Service
èwww.festo.com.
8.3 Checking cover strip
1. Check the cover strip for wave formation every 2000km.
2. Retension the cover strip as follows if waves are detected.
3. Replace the belt reversals and the cover strip if retension is no longer possible.
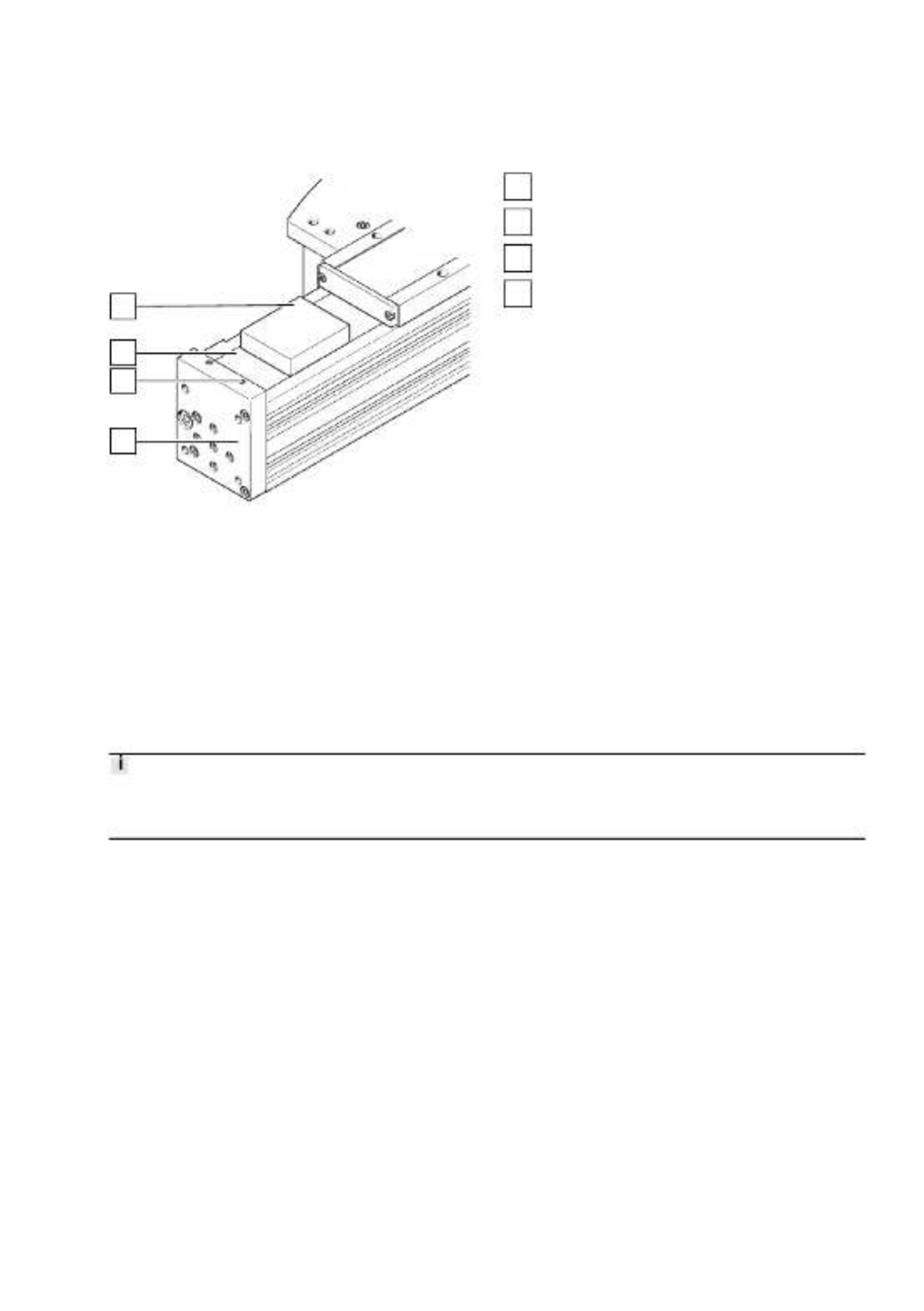
Festo — ELCC-TB — 2023-05c
Maintenance
17
Retensioning cover strip on both sides with ELCC-...-P9
1
2
3
4
Fig. 8: Retensioning cover strip
1
Clamping element
2
Cover strip
3
Screw
4
End cap
1. Unscrew the screws .3
2. Push the cover strip into the cover .2 4
3. Tighten the cover strip with a clamping element .1
4. Tighten the screws to 6Nm±10%.
8.4 Checking clamping unit
Clamping unit ELCC-...-C
Check the holding force of the clamping unit at every maintenance interval or after every emergency
braking in the event of a power failure.
The clamping unit must be replaced after 1000 emergency braking operations or after 50,000
clamping operations Contact your local Festo service centre.è
–Check holding function as follows:
1. Move the cantilever or slide to an end position.
2. Exhaust the clamping unit connection
3. Allow the test force (the test pressure) to act on the drive for at least 5s. During this time, the
cantilever or the slide must not move.
The test force and the tolerance window can be taken from the risk assessment of the application.
8.5 Cleaning axis
Clean the product with a clean, soft cloth and non-abrasive cleaning agents.
Removing abraded particles in the drive head
At every maintenance interval remove the particles from the toothed belt and cover strip wear on the
axis or in the drive head as required.
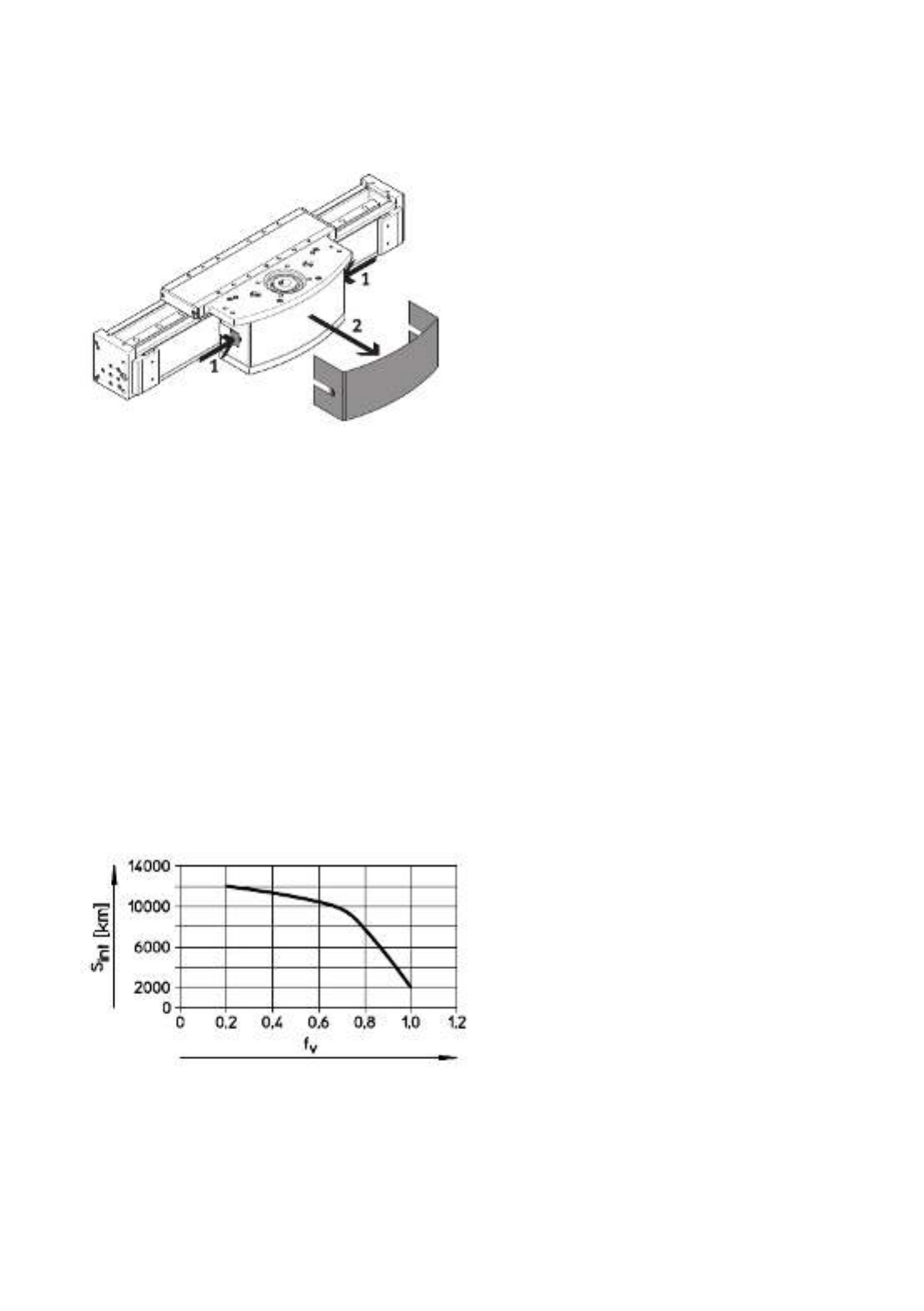
18
Festo — ELCC-TB — 2023-05c
Maintenance
1. Press both interlocks (1) simultaneously up to the stop.
2. With the interlocks (1) pressed, pull the housing (2) off the drive head.
3. Remove abraded particles in the drive head if necessary.
4. Insert the housing into the guide of the interlock and push it onto the drive head until the
interlocks engage.
8.6 Lubricating axis
Requirements:
Recirculating ball bearing guide
–The pressure grease gun LUB-1, 647958 is available.
–For ELGA-TB-KF: the roller-bearing grease LUB-KC1, 684474 is available.
–For ELGA-TB-KF-F1: roller bearing grease Elkalub VP 874 supplied by Chemie-Technik, Vöhringen, is
available.
–The lubrication adapter LUB-1-TR-I, 647959 or LUB-1-TR-L, 647960 is available.
1. Calculate the load comparison factor fv with formula for combined loads è10.1 Technical data,
mechanical.
2. Take the lubrication interval Sint as a function of the load comparison factor fv from the character-
istic curve.
3. Determine the load factors:
–Dusty and dirty environment.
–Nominal stroke 300 mm or 2000 mm.< >
–Ambient temperature +40 °C.>
–Operating age 3 years.>
–The travel profile matches triangular operation, e.g.frequent acceleration and braking.
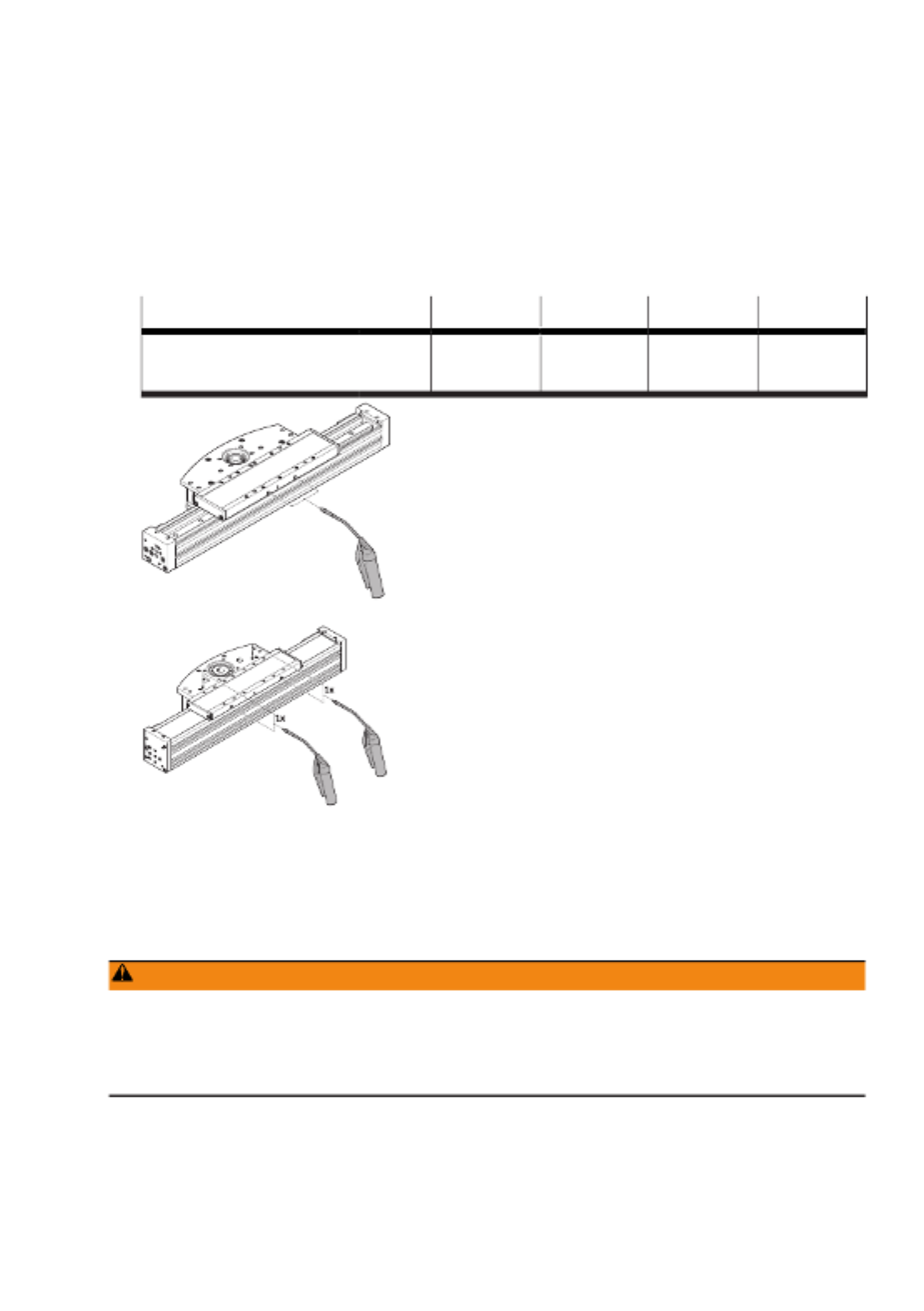
Festo — ELCC-TB — 2023-05c
Fault clearance
19
4. If there is a load factor, halve the lubrication interval Sint. If there are multiple load factors, reduce
the lubrication interval Sint to a quarter of the standard interval.
5. If necessary, replace the needle point of the pressure grease gun with the lubrication adapter,
axial outlet or radial outlet.
6. Press the pressure grease gun on the lubrication nipple of the recirculating ball bearing guide.
Press in the roller bearing grease at the front or left and right.
ELCC-TB-... -60 -70 -90 -110
Grease volume per lubri-
cating hole
[g] 1.7 5 7.5 11.2
7. Move along the complete travel distance during the lubrication process to distribute the grease
evenly in the interior.
8. If necessary, grease other components with roller bearing grease, e.g.the guide rail.
9 Fault clearance
WARNING
Unexpected movement of components.
Injury due to impacts or crushing.
• Before working on the product, switch off the control and secure it to prevent it from being switched
back on accidentally.
Produktspecifikationer
Varumärke: | Festo |
Kategori: | Inte kategoriserad |
Modell: | ELCC-TB-KF-110-200-0H-P0-CR |
Behöver du hjälp?
Om du behöver hjälp med Festo ELCC-TB-KF-110-200-0H-P0-CR ställ en fråga nedan och andra användare kommer att svara dig
Inte kategoriserad Festo Manualer

30 Mars 2025

30 Mars 2025

30 Mars 2025

30 Mars 2025

30 Mars 2025

30 Mars 2025

30 Mars 2025

30 Mars 2025

30 Mars 2025

30 Mars 2025
Inte kategoriserad Manualer
- Inte kategoriserad Zibro
- Inte kategoriserad Candy
- Inte kategoriserad Sony
- Inte kategoriserad Electrolux
- Inte kategoriserad Samsung
- Inte kategoriserad Xiaomi
- Inte kategoriserad Casio
- Inte kategoriserad ATAG
- Inte kategoriserad LG
- Inte kategoriserad Bosch
- Inte kategoriserad AEG
- Inte kategoriserad IKEA
- Inte kategoriserad Huawei
- Inte kategoriserad Braun
- Inte kategoriserad Brondi
- Inte kategoriserad HP
- Inte kategoriserad Philips
- Inte kategoriserad Panasonic
- Inte kategoriserad Bauknecht
- Inte kategoriserad BEKO
- Inte kategoriserad Delonghi
- Inte kategoriserad Daewoo
- Inte kategoriserad DeWalt
- Inte kategoriserad Epson
- Inte kategoriserad Etna
- Inte kategoriserad Ford
- Inte kategoriserad Fysic
- Inte kategoriserad Garmin
- Inte kategoriserad Grundig
- Inte kategoriserad Honeywell
- Inte kategoriserad Indesit
- Inte kategoriserad Inventum
- Inte kategoriserad JVC
- Inte kategoriserad JBL
- Inte kategoriserad Junkers
- Inte kategoriserad Kenwood
- Inte kategoriserad Krups
- Inte kategoriserad Karcher
- Inte kategoriserad Liebherr
- Inte kategoriserad Miele
- Inte kategoriserad Motorola
- Inte kategoriserad Medion
- Inte kategoriserad Nikon
- Inte kategoriserad Nokia
- Inte kategoriserad Olympus
- Inte kategoriserad Onkyo
- Inte kategoriserad Pioneer
- Inte kategoriserad Quigg
- Inte kategoriserad Ravensburger
- Inte kategoriserad Siemens
- Inte kategoriserad Toshiba
- Inte kategoriserad Unold
- Inte kategoriserad VTech
- Inte kategoriserad Whirlpool
- Inte kategoriserad WOLF-Garten
- Inte kategoriserad Wiko
- Inte kategoriserad Yamaha
- Inte kategoriserad Yealink
- Inte kategoriserad Zanussi
- Inte kategoriserad Tefal
- Inte kategoriserad Vaillant
- Inte kategoriserad Canon
- Inte kategoriserad Lego
- Inte kategoriserad Volvo
- Inte kategoriserad A.O. Smith
- Inte kategoriserad Ade
- Inte kategoriserad Adidas
- Inte kategoriserad Adler
- Inte kategoriserad Abus
- Inte kategoriserad Ag Neovo
- Inte kategoriserad Aduro
- Inte kategoriserad Acer
- Inte kategoriserad ACCU-CHEK
- Inte kategoriserad Aiwa
- Inte kategoriserad Al-ko
- Inte kategoriserad Alcatel
- Inte kategoriserad Allnet
- Inte kategoriserad Alpina
- Inte kategoriserad Ambiano
- Inte kategoriserad Albrecht
- Inte kategoriserad Amica
- Inte kategoriserad Agfa
- Inte kategoriserad Alecto
- Inte kategoriserad Airlux
- Inte kategoriserad Aligator
- Inte kategoriserad Akg
- Inte kategoriserad AOC
- Inte kategoriserad Ambrogio
- Inte kategoriserad Akai
- Inte kategoriserad Alphatronics
- Inte kategoriserad Afk
- Inte kategoriserad Apc
- Inte kategoriserad Allied Telesis
- Inte kategoriserad Allibert
- Inte kategoriserad Alienware
- Inte kategoriserad Alpine
- Inte kategoriserad Amana
- Inte kategoriserad Aluratek
- Inte kategoriserad Amfra
- Inte kategoriserad Amazfit
- Inte kategoriserad Ansmann
- Inte kategoriserad Alesis
- Inte kategoriserad Apple
- Inte kategoriserad Advance Acoustic
- Inte kategoriserad Alcon
- Inte kategoriserad Amazon
- Inte kategoriserad Airlive
- Inte kategoriserad Anker
- Inte kategoriserad A4tech
- Inte kategoriserad Ampeg
- Inte kategoriserad Amplicom
- Inte kategoriserad Amprobe
- Inte kategoriserad Archos
- Inte kategoriserad Argon
- Inte kategoriserad Ariete
- Inte kategoriserad Arendo
- Inte kategoriserad Arcelik
- Inte kategoriserad American Audio
- Inte kategoriserad Aprilia
- Inte kategoriserad Aquapur
- Inte kategoriserad Acti
- Inte kategoriserad Akasa
- Inte kategoriserad Amiko
- Inte kategoriserad Aeris
- Inte kategoriserad Ascom
- Inte kategoriserad Act
- Inte kategoriserad Arturia
- Inte kategoriserad Alpen Kreuzer
- Inte kategoriserad Asko
- Inte kategoriserad ACME
- Inte kategoriserad Alto
- Inte kategoriserad Dreamland
- Inte kategoriserad Reflecta
- Inte kategoriserad Silverline
- Inte kategoriserad Argus
- Inte kategoriserad Joie
- Inte kategoriserad Adobe
- Inte kategoriserad Suunto
- Inte kategoriserad ATN
- Inte kategoriserad Ziggo
- Inte kategoriserad Bartscher
- Inte kategoriserad Prestigio
- Inte kategoriserad Edimax
- Inte kategoriserad Intermatic
- Inte kategoriserad Strong
- Inte kategoriserad Toolland
- Inte kategoriserad Morphy Richards
- Inte kategoriserad Icy Box
- Inte kategoriserad Adventuridge
- Inte kategoriserad Brennenstuhl
- Inte kategoriserad Ferm
- Inte kategoriserad OneConcept
- Inte kategoriserad MJX
- Inte kategoriserad Hirschmann
- Inte kategoriserad Kruidvat
- Inte kategoriserad Vileda
- Inte kategoriserad Absima
- Inte kategoriserad Google
- Inte kategoriserad Hikvision
- Inte kategoriserad Audison
- Inte kategoriserad Arris
- Inte kategoriserad Workzone
- Inte kategoriserad Sabo
- Inte kategoriserad Eurom
- Inte kategoriserad Shark
- Inte kategoriserad GE
- Inte kategoriserad Orbegozo
- Inte kategoriserad Salton
- Inte kategoriserad Proteca
- Inte kategoriserad Princess
- Inte kategoriserad Generac
- Inte kategoriserad Topmove
- Inte kategoriserad Subaru
- Inte kategoriserad BenQ
- Inte kategoriserad Lexibook
- Inte kategoriserad Brother
- Inte kategoriserad Ozito
- Inte kategoriserad Gude
- Inte kategoriserad Sharp
- Inte kategoriserad Fisher And Paykel
- Inte kategoriserad Bertazzoni
- Inte kategoriserad Loewe
- Inte kategoriserad Leica
- Inte kategoriserad Klarstein
- Inte kategoriserad Fagor
- Inte kategoriserad Brandt
- Inte kategoriserad Omega
- Inte kategoriserad Severin
- Inte kategoriserad Smeg
- Inte kategoriserad Telefunken
- Inte kategoriserad Gorenje
- Inte kategoriserad Neff
- Inte kategoriserad Silvercrest
- Inte kategoriserad Jysk
- Inte kategoriserad Toorx
- Inte kategoriserad Body Solid
- Inte kategoriserad Makita
- Inte kategoriserad Draper
- Inte kategoriserad Tryton
- Inte kategoriserad Hitachi
- Inte kategoriserad Spektrum
- Inte kategoriserad Nedis
- Inte kategoriserad Thomson
- Inte kategoriserad Arthur Martin
- Inte kategoriserad Oceanic
- Inte kategoriserad Korona
- Inte kategoriserad Gembird
- Inte kategoriserad Hoover
- Inte kategoriserad Saturn
- Inte kategoriserad Black And Decker
- Inte kategoriserad Bestway
- Inte kategoriserad Breville
- Inte kategoriserad Tiger
- Inte kategoriserad KitchenAid
- Inte kategoriserad Innoliving
- Inte kategoriserad Tristar
- Inte kategoriserad Domo
- Inte kategoriserad Teka
- Inte kategoriserad Trisa
- Inte kategoriserad Yale
- Inte kategoriserad Progress
- Inte kategoriserad Lenco
- Inte kategoriserad GoPro
- Inte kategoriserad Cata
- Inte kategoriserad Pyle
- Inte kategoriserad Gaggenau
- Inte kategoriserad Vonroc
- Inte kategoriserad Hotpoint-Ariston
- Inte kategoriserad Meradiso
- Inte kategoriserad Calor
- Inte kategoriserad Remington
- Inte kategoriserad Rowenta
- Inte kategoriserad Waring Commercial
- Inte kategoriserad Maestro
- Inte kategoriserad Taylor
- Inte kategoriserad Kernau
- Inte kategoriserad Maytag
- Inte kategoriserad Miomare
- Inte kategoriserad Maxi-Cosi
- Inte kategoriserad Livoo
- Inte kategoriserad BH Fitness
- Inte kategoriserad OBH Nordica
- Inte kategoriserad Stanley
- Inte kategoriserad Manta
- Inte kategoriserad Tevion
- Inte kategoriserad Crivit
- Inte kategoriserad Asus
- Inte kategoriserad GPO
- Inte kategoriserad Thermador
- Inte kategoriserad Lucide
- Inte kategoriserad Parisot
- Inte kategoriserad Caliber
- Inte kategoriserad SereneLife
- Inte kategoriserad Beurer
- Inte kategoriserad Smoby
- Inte kategoriserad Lotus
- Inte kategoriserad Skil
- Inte kategoriserad OK
- Inte kategoriserad Hisense
- Inte kategoriserad Hyundai
- Inte kategoriserad Hanseatic
- Inte kategoriserad Vox
- Inte kategoriserad Cylinda
- Inte kategoriserad Yato
- Inte kategoriserad Dyson
- Inte kategoriserad Bestron
- Inte kategoriserad Bellini
- Inte kategoriserad BaByliss
- Inte kategoriserad Proscan
- Inte kategoriserad Eminent
- Inte kategoriserad Pressalit
- Inte kategoriserad Hilti
- Inte kategoriserad SilverStone
- Inte kategoriserad Avanti
- Inte kategoriserad Oster
- Inte kategoriserad Kichler
- Inte kategoriserad VAX
- Inte kategoriserad Trekstor
- Inte kategoriserad Renkforce
- Inte kategoriserad Westinghouse
- Inte kategoriserad Cherry
- Inte kategoriserad ECG
- Inte kategoriserad Moulinex
- Inte kategoriserad Sinbo
- Inte kategoriserad Izzy
- Inte kategoriserad Kodak
- Inte kategoriserad Bushnell
- Inte kategoriserad Pelgrim
- Inte kategoriserad Blomberg
- Inte kategoriserad Ryobi
- Inte kategoriserad Bush
- Inte kategoriserad Jata
- Inte kategoriserad Rapoo
- Inte kategoriserad LC-Power
- Inte kategoriserad Sharkoon
- Inte kategoriserad Melissa
- Inte kategoriserad Magic Chef
- Inte kategoriserad Florabest
- Inte kategoriserad VirtuFit
- Inte kategoriserad Swan
- Inte kategoriserad Emerio
- Inte kategoriserad RCA
- Inte kategoriserad Scarlett
- Inte kategoriserad Clatronic
- Inte kategoriserad Singer
- Inte kategoriserad Fritel
- Inte kategoriserad Taurus
- Inte kategoriserad Ordex
- Inte kategoriserad Itho
- Inte kategoriserad Russell Hobbs
- Inte kategoriserad Elica
- Inte kategoriserad Constructa
- Inte kategoriserad Targus
- Inte kategoriserad Summit
- Inte kategoriserad Hotpoint
- Inte kategoriserad Q-CONNECT
- Inte kategoriserad Lowrance
- Inte kategoriserad Chicco
- Inte kategoriserad Sencor
- Inte kategoriserad Midea
- Inte kategoriserad Lanaform
- Inte kategoriserad Conair
- Inte kategoriserad Jane
- Inte kategoriserad Landmann
- Inte kategoriserad Eureka
- Inte kategoriserad 3M
- Inte kategoriserad Sicce
- Inte kategoriserad Overmax
- Inte kategoriserad Pfaff
- Inte kategoriserad Vivanco
- Inte kategoriserad Niceboy
- Inte kategoriserad Cuisinart
- Inte kategoriserad GPX
- Inte kategoriserad Outwell
- Inte kategoriserad Festool
- Inte kategoriserad Sitecom
- Inte kategoriserad Blaupunkt
- Inte kategoriserad Metabo
- Inte kategoriserad TP Link
- Inte kategoriserad Juki
- Inte kategoriserad Megasat
- Inte kategoriserad Britax
- Inte kategoriserad United Office
- Inte kategoriserad Logitech
- Inte kategoriserad Concept
- Inte kategoriserad Cybex
- Inte kategoriserad Gram
- Inte kategoriserad Monogram
- Inte kategoriserad Spanninga
- Inte kategoriserad Lenovo
- Inte kategoriserad Solac
- Inte kategoriserad Manhattan
- Inte kategoriserad Frigidaire
- Inte kategoriserad Jura
- Inte kategoriserad Sunbeam
- Inte kategoriserad ZOTAC
- Inte kategoriserad BeamZ
- Inte kategoriserad Parkside
- Inte kategoriserad Worx
- Inte kategoriserad Svan
- Inte kategoriserad Hard Head
- Inte kategoriserad Exibel
- Inte kategoriserad Logik
- Inte kategoriserad Medisana
- Inte kategoriserad Medela
- Inte kategoriserad NAD
- Inte kategoriserad Easy Camp
- Inte kategoriserad Danby
- Inte kategoriserad Anslut
- Inte kategoriserad Balay
- Inte kategoriserad Texas Instruments
- Inte kategoriserad Ezviz
- Inte kategoriserad Bowers And Wilkins
- Inte kategoriserad Meec Tools
- Inte kategoriserad Stirling
- Inte kategoriserad Thermaltake
- Inte kategoriserad Energy Sistem
- Inte kategoriserad Orbit
- Inte kategoriserad Black Box
- Inte kategoriserad Harman Kardon
- Inte kategoriserad Audio-Technica
- Inte kategoriserad Humminbird
- Inte kategoriserad Auto Joe
- Inte kategoriserad Polaroid
- Inte kategoriserad Trust
- Inte kategoriserad Cardo
- Inte kategoriserad KEF
- Inte kategoriserad Milwaukee
- Inte kategoriserad Fortinet
- Inte kategoriserad PKM
- Inte kategoriserad Youin
- Inte kategoriserad Daikin
- Inte kategoriserad Hikoki
- Inte kategoriserad Carson
- Inte kategoriserad Telestar
- Inte kategoriserad Elro
- Inte kategoriserad Valore
- Inte kategoriserad Crunch
- Inte kategoriserad Accucold
- Inte kategoriserad Sun Joe
- Inte kategoriserad Frilec
- Inte kategoriserad Perfecta
- Inte kategoriserad EMOS
- Inte kategoriserad Doro
- Inte kategoriserad Sagem
- Inte kategoriserad Teesa
- Inte kategoriserad Extech
- Inte kategoriserad Jumbo
- Inte kategoriserad Rosieres
- Inte kategoriserad Cricut
- Inte kategoriserad Mesko
- Inte kategoriserad Hähnel
- Inte kategoriserad Ferplast
- Inte kategoriserad Melitta
- Inte kategoriserad Salora
- Inte kategoriserad Enduro
- Inte kategoriserad Aukey
- Inte kategoriserad Lava
- Inte kategoriserad Profilo
- Inte kategoriserad Tunturi
- Inte kategoriserad Dremel
- Inte kategoriserad Victron Energy
- Inte kategoriserad Avaya
- Inte kategoriserad Cramer
- Inte kategoriserad Ernesto
- Inte kategoriserad KlikaanKlikuit
- Inte kategoriserad KKT Kolbe
- Inte kategoriserad Gemini
- Inte kategoriserad Easypix
- Inte kategoriserad Beper
- Inte kategoriserad Denver
- Inte kategoriserad Omron
- Inte kategoriserad Thetford
- Inte kategoriserad Ei Electronics
- Inte kategoriserad Thule
- Inte kategoriserad Berg
- Inte kategoriserad Tripp Lite
- Inte kategoriserad Simplified MFG
- Inte kategoriserad Truma
- Inte kategoriserad Optoma
- Inte kategoriserad CDA
- Inte kategoriserad Vision
- Inte kategoriserad Bissell
- Inte kategoriserad ABB
- Inte kategoriserad Genie
- Inte kategoriserad Imperial
- Inte kategoriserad Cateye
- Inte kategoriserad Hendi
- Inte kategoriserad Suzuki
- Inte kategoriserad Mellerware
- Inte kategoriserad Intergas
- Inte kategoriserad President
- Inte kategoriserad Intex
- Inte kategoriserad Stinger
- Inte kategoriserad Toa
- Inte kategoriserad GLP
- Inte kategoriserad Roland
- Inte kategoriserad Silva
- Inte kategoriserad DataVideo
- Inte kategoriserad ZTE
- Inte kategoriserad Energenie
- Inte kategoriserad Optex
- Inte kategoriserad Hazet
- Inte kategoriserad Bebe Confort
- Inte kategoriserad Heinner
- Inte kategoriserad Schneider
- Inte kategoriserad BMW
- Inte kategoriserad Termozeta
- Inte kategoriserad Bella
- Inte kategoriserad Axis
- Inte kategoriserad Metrix
- Inte kategoriserad Sanyo
- Inte kategoriserad Vitek
- Inte kategoriserad Palson
- Inte kategoriserad ART
- Inte kategoriserad Benning
- Inte kategoriserad Eldom
- Inte kategoriserad Valeton
- Inte kategoriserad Nilox
- Inte kategoriserad Vango
- Inte kategoriserad Ventura
- Inte kategoriserad Einhell
- Inte kategoriserad Ultimate Speed
- Inte kategoriserad Hama
- Inte kategoriserad Tiptop Audio
- Inte kategoriserad Sonos
- Inte kategoriserad Summit Audio
- Inte kategoriserad Soundmaster
- Inte kategoriserad SKS
- Inte kategoriserad Hifonics
- Inte kategoriserad Fujifilm
- Inte kategoriserad Musway
- Inte kategoriserad Kensington
- Inte kategoriserad Nautilus
- Inte kategoriserad Byron
- Inte kategoriserad Parrot
- Inte kategoriserad Cresta
- Inte kategoriserad Maxxmee
- Inte kategoriserad Brigmton
- Inte kategoriserad Voltcraft
- Inte kategoriserad Kenmore
- Inte kategoriserad Denon
- Inte kategoriserad Sunstech
- Inte kategoriserad Bang And Olufsen
- Inte kategoriserad Vonyx
- Inte kategoriserad Gardena
- Inte kategoriserad Sennheiser
- Inte kategoriserad Philco
- Inte kategoriserad Weller
- Inte kategoriserad Theben
- Inte kategoriserad Bryton
- Inte kategoriserad Smith & Wesson
- Inte kategoriserad AVM
- Inte kategoriserad Reich
- Inte kategoriserad TCL
- Inte kategoriserad Elektrobock
- Inte kategoriserad Chamberlain
- Inte kategoriserad Gigabyte
- Inte kategoriserad Nabo
- Inte kategoriserad Guzzanti
- Inte kategoriserad Defy
- Inte kategoriserad Stiebel Eltron
- Inte kategoriserad DeLock
- Inte kategoriserad Plant Craft
- Inte kategoriserad Infiniton
- Inte kategoriserad Thorens
- Inte kategoriserad Dubatti
- Inte kategoriserad Terraillon
- Inte kategoriserad Baumr-AG
- Inte kategoriserad Bionaire
- Inte kategoriserad Maginon
- Inte kategoriserad Midland
- Inte kategoriserad Konica Minolta
- Inte kategoriserad Sylvania
- Inte kategoriserad Mitsubishi
- Inte kategoriserad Dometic
- Inte kategoriserad Lasko
- Inte kategoriserad Campomatic
- Inte kategoriserad Patton
- Inte kategoriserad Igloo
- Inte kategoriserad Aspes
- Inte kategoriserad Velleman
- Inte kategoriserad Senco
- Inte kategoriserad Hayward
- Inte kategoriserad Babymoov
- Inte kategoriserad Ninja
- Inte kategoriserad Hauck
- Inte kategoriserad Bialetti
- Inte kategoriserad Microsoft
- Inte kategoriserad Tork
- Inte kategoriserad Nec
- Inte kategoriserad SanDisk
- Inte kategoriserad Zoofari
- Inte kategoriserad Techly
- Inte kategoriserad Dimplex
- Inte kategoriserad DCG
- Inte kategoriserad Yard Force
- Inte kategoriserad Numatic
- Inte kategoriserad Swissvoice
- Inte kategoriserad Korg
- Inte kategoriserad Varta
- Inte kategoriserad Emerson
- Inte kategoriserad Vaude
- Inte kategoriserad Totolink
- Inte kategoriserad Eheim
- Inte kategoriserad GlobalTronics
- Inte kategoriserad Vemer
- Inte kategoriserad Smartwares
- Inte kategoriserad LD Systems
- Inte kategoriserad Sunny
- Inte kategoriserad Technisat
- Inte kategoriserad La Crosse Technology
- Inte kategoriserad Easymaxx
- Inte kategoriserad GoGEN
- Inte kategoriserad Inglesina
- Inte kategoriserad Suntec
- Inte kategoriserad HK Audio
- Inte kategoriserad BBB
- Inte kategoriserad BlueBuilt
- Inte kategoriserad Peugeot
- Inte kategoriserad Gazelle
- Inte kategoriserad Rockford Fosgate
- Inte kategoriserad Weber
- Inte kategoriserad Blanco
- Inte kategoriserad BDI
- Inte kategoriserad Profile
- Inte kategoriserad Marquant
- Inte kategoriserad Orima
- Inte kategoriserad Nibe
- Inte kategoriserad Damixa
- Inte kategoriserad Bogen
- Inte kategoriserad Da-Lite
- Inte kategoriserad Trebs
- Inte kategoriserad Bugaboo
- Inte kategoriserad Ferroli
- Inte kategoriserad Ednet
- Inte kategoriserad Technics
- Inte kategoriserad Luxor
- Inte kategoriserad Solis
- Inte kategoriserad Cisco
- Inte kategoriserad Bowflex
- Inte kategoriserad Husqvarna
- Inte kategoriserad AVerMedia
- Inte kategoriserad Visage
- Inte kategoriserad Koenic
- Inte kategoriserad Sena
- Inte kategoriserad Celestron
- Inte kategoriserad Falmec
- Inte kategoriserad Haier
- Inte kategoriserad American DJ
- Inte kategoriserad Master Lock
- Inte kategoriserad Krüger And Matz
- Inte kategoriserad Salus
- Inte kategoriserad Matrox
- Inte kategoriserad Seiko
- Inte kategoriserad Rangemaster
- Inte kategoriserad Maktec
- Inte kategoriserad Kubota
- Inte kategoriserad Forza
- Inte kategoriserad Gree
- Inte kategoriserad H.Koenig
- Inte kategoriserad Binatone
- Inte kategoriserad Connect IT
- Inte kategoriserad Eufy
- Inte kategoriserad Steren
- Inte kategoriserad Haeger
- Inte kategoriserad Allen & Heath
- Inte kategoriserad Perel
- Inte kategoriserad Ariston Thermo
- Inte kategoriserad Nintendo
- Inte kategoriserad Steba
- Inte kategoriserad Engenius
- Inte kategoriserad Viking
- Inte kategoriserad Nuna
- Inte kategoriserad Iiyama
- Inte kategoriserad Tanita
- Inte kategoriserad Burg-Wachter
- Inte kategoriserad Eico
- Inte kategoriserad Volkswagen
- Inte kategoriserad Polk
- Inte kategoriserad Plantronics
- Inte kategoriserad Kicker
- Inte kategoriserad Bose
- Inte kategoriserad Hansa
- Inte kategoriserad Kyoritsu
- Inte kategoriserad Polar
- Inte kategoriserad Nero
- Inte kategoriserad Lumens
- Inte kategoriserad Thor
- Inte kategoriserad Sensiplast
- Inte kategoriserad Steinel
- Inte kategoriserad Fitbit
- Inte kategoriserad Kubo
- Inte kategoriserad Exagerate
- Inte kategoriserad Benavent
- Inte kategoriserad IFM
- Inte kategoriserad Beem
- Inte kategoriserad Pro-User
- Inte kategoriserad Air King
- Inte kategoriserad Tanaka
- Inte kategoriserad Exquisit
- Inte kategoriserad Mattel
- Inte kategoriserad Gossen
- Inte kategoriserad Elba
- Inte kategoriserad Ideal
- Inte kategoriserad Flir
- Inte kategoriserad Homedics
- Inte kategoriserad Paidi
- Inte kategoriserad Steelseries
- Inte kategoriserad Clarion
- Inte kategoriserad Somfy
- Inte kategoriserad SBS
- Inte kategoriserad KiddyGuard
- Inte kategoriserad Proline
- Inte kategoriserad Livarno
- Inte kategoriserad Barkan
- Inte kategoriserad Grohe
- Inte kategoriserad Fresh N Rebel
- Inte kategoriserad Netis
- Inte kategoriserad Sanitas
- Inte kategoriserad Coby
- Inte kategoriserad Lorelli
- Inte kategoriserad Euromaid
- Inte kategoriserad Royal Sovereign
- Inte kategoriserad HTC
- Inte kategoriserad Corberó
- Inte kategoriserad King
- Inte kategoriserad Crosley
- Inte kategoriserad AcuRite
- Inte kategoriserad Domyos
- Inte kategoriserad Ergobaby
- Inte kategoriserad New Pol
- Inte kategoriserad Zelmer
- Inte kategoriserad Mackie
- Inte kategoriserad Envivo
- Inte kategoriserad Muse
- Inte kategoriserad Petzl
- Inte kategoriserad Teufel
- Inte kategoriserad Auriol
- Inte kategoriserad Marantz
- Inte kategoriserad Fujitsu
- Inte kategoriserad True
- Inte kategoriserad Ardes
- Inte kategoriserad AJA
- Inte kategoriserad Gustavsberg
- Inte kategoriserad Mac Audio
- Inte kategoriserad Galaxy Audio
- Inte kategoriserad Be Quiet!
- Inte kategoriserad Black Diamond
- Inte kategoriserad Rega
- Inte kategoriserad ESYLUX
- Inte kategoriserad Gaggia
- Inte kategoriserad Ventus
- Inte kategoriserad Melinera
- Inte kategoriserad TOTO
- Inte kategoriserad Nutrichef
- Inte kategoriserad Pro-Ject
- Inte kategoriserad Craftsman
- Inte kategoriserad Fisher Price
- Inte kategoriserad Technoline
- Inte kategoriserad Genius
- Inte kategoriserad Osann
- Inte kategoriserad Lindam
- Inte kategoriserad Metz
- Inte kategoriserad Adj
- Inte kategoriserad Kelvinator
- Inte kategoriserad Sage
- Inte kategoriserad ETA
- Inte kategoriserad Goliath
- Inte kategoriserad Oase
- Inte kategoriserad Biltema
- Inte kategoriserad Yamato
- Inte kategoriserad Dorma
- Inte kategoriserad Life Fitness
- Inte kategoriserad Belgacom
- Inte kategoriserad Digitus
- Inte kategoriserad Pelican
- Inte kategoriserad Kathrein
- Inte kategoriserad Malmbergs
- Inte kategoriserad Phoenix
- Inte kategoriserad Asrock
- Inte kategoriserad Nitecore
- Inte kategoriserad Draytek
- Inte kategoriserad AV:link
- Inte kategoriserad Olympia
- Inte kategoriserad Power Craft
- Inte kategoriserad GBC
- Inte kategoriserad Belkin
- Inte kategoriserad Prenatal
- Inte kategoriserad Champion
- Inte kategoriserad Irobot
- Inte kategoriserad Soler And Palau
- Inte kategoriserad Tvilum
- Inte kategoriserad Razer
- Inte kategoriserad Stadler Form
- Inte kategoriserad Devolo
- Inte kategoriserad Heylo
- Inte kategoriserad Mio
- Inte kategoriserad TacTic
- Inte kategoriserad Neumann
- Inte kategoriserad Nolte
- Inte kategoriserad Geuther
- Inte kategoriserad G3
- Inte kategoriserad Zephyr
- Inte kategoriserad Peach
- Inte kategoriserad Trixie
- Inte kategoriserad Bomann
- Inte kategoriserad Snow Joe
- Inte kategoriserad GRE
- Inte kategoriserad Finnlo
- Inte kategoriserad DJI
- Inte kategoriserad Proficare
- Inte kategoriserad Hamilton Beach
- Inte kategoriserad Novy
- Inte kategoriserad Dymo
- Inte kategoriserad Linksys
- Inte kategoriserad Lescha
- Inte kategoriserad Capital Sports
- Inte kategoriserad Pulsar
- Inte kategoriserad RCF
- Inte kategoriserad Kuppersbusch
- Inte kategoriserad Barco
- Inte kategoriserad Buffalo
- Inte kategoriserad Continental Edison
- Inte kategoriserad Vello
- Inte kategoriserad Lamax
- Inte kategoriserad Wmf
- Inte kategoriserad Jenn-Air
- Inte kategoriserad Powerplus
- Inte kategoriserad R-Vent
- Inte kategoriserad Graef
- Inte kategoriserad Stiga
- Inte kategoriserad Audioline
- Inte kategoriserad Porter-Cable
- Inte kategoriserad Woood
- Inte kategoriserad Uniden
- Inte kategoriserad Dahua Technology
- Inte kategoriserad Klipsch
- Inte kategoriserad Audiovox
- Inte kategoriserad Carpigiani
- Inte kategoriserad Ion
- Inte kategoriserad Cotech
- Inte kategoriserad Insignia
- Inte kategoriserad Renegade
- Inte kategoriserad Davis
- Inte kategoriserad ICU
- Inte kategoriserad Rossmax
- Inte kategoriserad Nacon
- Inte kategoriserad Daitsu
- Inte kategoriserad Edesa
- Inte kategoriserad Sanus
- Inte kategoriserad Farberware
- Inte kategoriserad Ufesa
- Inte kategoriserad CasaFan
- Inte kategoriserad Viessmann
- Inte kategoriserad Milectric
- Inte kategoriserad Vicks
- Inte kategoriserad Mobicool
- Inte kategoriserad Supermicro
- Inte kategoriserad Yaesu
- Inte kategoriserad Microlife
- Inte kategoriserad Rommelsbacher
- Inte kategoriserad Walkstool
- Inte kategoriserad Rollei
- Inte kategoriserad Macally
- Inte kategoriserad Wilfa
- Inte kategoriserad GeoVision
- Inte kategoriserad Kidde
- Inte kategoriserad Apogee
- Inte kategoriserad Carrier
- Inte kategoriserad Peerless-AV
- Inte kategoriserad Netgear
- Inte kategoriserad Vogels
- Inte kategoriserad Growatt
- Inte kategoriserad Artsound
- Inte kategoriserad Grothe
- Inte kategoriserad LevelOne
- Inte kategoriserad Kwantum
- Inte kategoriserad Olimpia Splendid
- Inte kategoriserad Genesis
- Inte kategoriserad Pyle Pro
- Inte kategoriserad Peavey
- Inte kategoriserad BT
- Inte kategoriserad MXL
- Inte kategoriserad Testboy
- Inte kategoriserad Transcend
- Inte kategoriserad Goclever
- Inte kategoriserad Wehkamp
- Inte kategoriserad Evenflo
- Inte kategoriserad Profoon
- Inte kategoriserad Svedbergs
- Inte kategoriserad Kaiser
- Inte kategoriserad QNAP
- Inte kategoriserad Salter
- Inte kategoriserad Dual
- Inte kategoriserad Osprey
- Inte kategoriserad Bunn
- Inte kategoriserad Trotec
- Inte kategoriserad Graco
- Inte kategoriserad Maglite
- Inte kategoriserad DIO
- Inte kategoriserad Boss
- Inte kategoriserad Ninebot
- Inte kategoriserad Siedle
- Inte kategoriserad George Foreman
- Inte kategoriserad Cilio
- Inte kategoriserad McIntosh
- Inte kategoriserad LaCie
- Inte kategoriserad Itho-Daalderop
- Inte kategoriserad Maul
- Inte kategoriserad Sigma
- Inte kategoriserad BabyOno
- Inte kategoriserad Bixolon
- Inte kategoriserad Karibu
- Inte kategoriserad Troy-Bilt
- Inte kategoriserad Fellowes
- Inte kategoriserad Asaklitt
- Inte kategoriserad Ricoh
- Inte kategoriserad Oricom
- Inte kategoriserad Behringer
- Inte kategoriserad Laica
- Inte kategoriserad Enders
- Inte kategoriserad Rusta
- Inte kategoriserad Samac
- Inte kategoriserad Brevi
- Inte kategoriserad Waterpik
- Inte kategoriserad Franke
- Inte kategoriserad Stokke
- Inte kategoriserad Sodastream
- Inte kategoriserad SMA
- Inte kategoriserad Kayser
- Inte kategoriserad AYA
- Inte kategoriserad Autotek
- Inte kategoriserad Safety 1st
- Inte kategoriserad PreSonus
- Inte kategoriserad Evga
- Inte kategoriserad Hive
- Inte kategoriserad Danfoss
- Inte kategoriserad Peg Perego
- Inte kategoriserad Brabantia
- Inte kategoriserad Camry
- Inte kategoriserad AS - Schwabe
- Inte kategoriserad Fissler
- Inte kategoriserad Kayoba
- Inte kategoriserad NOCO
- Inte kategoriserad Lexmark
- Inte kategoriserad Native Instruments
- Inte kategoriserad Cobra
- Inte kategoriserad MB Quart
- Inte kategoriserad Inkbird
- Inte kategoriserad NGS
- Inte kategoriserad Nodor
- Inte kategoriserad Shimano
- Inte kategoriserad Godox
- Inte kategoriserad Marshall
- Inte kategoriserad Dell
- Inte kategoriserad Electro-Voice
- Inte kategoriserad Valcom
- Inte kategoriserad Goobay
- Inte kategoriserad Hammer
- Inte kategoriserad Switel
- Inte kategoriserad Hager
- Inte kategoriserad Michelin
- Inte kategoriserad Magnus
- Inte kategoriserad Bresser
- Inte kategoriserad Olight
- Inte kategoriserad Liftmaster
- Inte kategoriserad Bopita
- Inte kategoriserad FireAngel
- Inte kategoriserad Challenge
- Inte kategoriserad Tascam
- Inte kategoriserad Duux
- Inte kategoriserad Mercusys
- Inte kategoriserad Chacon
- Inte kategoriserad Astro
- Inte kategoriserad Imetec
- Inte kategoriserad Focal
- Inte kategoriserad Salta
- Inte kategoriserad InFocus
- Inte kategoriserad Focusrite
- Inte kategoriserad Bigben
- Inte kategoriserad Playseat
- Inte kategoriserad Topcraft
- Inte kategoriserad Kraftwerk
- Inte kategoriserad Texas
- Inte kategoriserad Naish
- Inte kategoriserad Olivetti
- Inte kategoriserad Massive
- Inte kategoriserad Barska
- Inte kategoriserad Wacom
- Inte kategoriserad Auna
- Inte kategoriserad Weihrauch Sport
- Inte kategoriserad Blaze
- Inte kategoriserad Dirt Devil
- Inte kategoriserad Hombli
- Inte kategoriserad Martha Stewart
- Inte kategoriserad Reolink
- Inte kategoriserad Milan
- Inte kategoriserad Lümme
- Inte kategoriserad Jocel
- Inte kategoriserad First Alert
- Inte kategoriserad Springfree
- Inte kategoriserad Ansco
- Inte kategoriserad Crock-Pot
- Inte kategoriserad Glem Gas
- Inte kategoriserad Xblitz
- Inte kategoriserad IK Multimedia
- Inte kategoriserad Elation
- Inte kategoriserad Goodram
- Inte kategoriserad MADE
- Inte kategoriserad Noma
- Inte kategoriserad TFA
- Inte kategoriserad Spear & Jackson
- Inte kategoriserad Jabra
- Inte kategoriserad Scheppach
- Inte kategoriserad IDance
- Inte kategoriserad Habitat
- Inte kategoriserad Body Sculpture
- Inte kategoriserad Samson
- Inte kategoriserad Atika
- Inte kategoriserad Maxview
- Inte kategoriserad Bifinett
- Inte kategoriserad U-Line
- Inte kategoriserad Honda
- Inte kategoriserad Planet
- Inte kategoriserad Yongnuo
- Inte kategoriserad Zhiyun
- Inte kategoriserad Boso
- Inte kategoriserad Wagner
- Inte kategoriserad Gamma
- Inte kategoriserad Proctor Silex
- Inte kategoriserad Elite
- Inte kategoriserad Zodiac
- Inte kategoriserad Rupert Neve Designs
- Inte kategoriserad Carel
- Inte kategoriserad BOHLT
- Inte kategoriserad Handicare
- Inte kategoriserad ZyXEL
- Inte kategoriserad McCulloch
- Inte kategoriserad Primo
- Inte kategoriserad Rocketfish
- Inte kategoriserad Little Tikes
- Inte kategoriserad Hunter
- Inte kategoriserad Speed-Link
- Inte kategoriserad Laser
- Inte kategoriserad Creda
- Inte kategoriserad Western Digital
- Inte kategoriserad Tower
- Inte kategoriserad Comfee
- Inte kategoriserad Alba
- Inte kategoriserad Honor
- Inte kategoriserad Clas Ohlson
- Inte kategoriserad Baninni
- Inte kategoriserad Gastroback
- Inte kategoriserad Naxa
- Inte kategoriserad Nemef
- Inte kategoriserad TomTom
- Inte kategoriserad Viper
- Inte kategoriserad Atlantic
- Inte kategoriserad Meireles
- Inte kategoriserad Powerfix
- Inte kategoriserad RugGear
- Inte kategoriserad Sven
- Inte kategoriserad Dacor
- Inte kategoriserad Umidigi
- Inte kategoriserad Technika
- Inte kategoriserad Saro
- Inte kategoriserad Millenium
- Inte kategoriserad Vogue
- Inte kategoriserad Grixx
- Inte kategoriserad Navitel
- Inte kategoriserad Topeak
- Inte kategoriserad Scandomestic
- Inte kategoriserad Owon
- Inte kategoriserad V-Zug
- Inte kategoriserad SuperFish
- Inte kategoriserad Luvion
- Inte kategoriserad Godrej
- Inte kategoriserad Sauber
- Inte kategoriserad Aqua Joe
- Inte kategoriserad Shure
- Inte kategoriserad Innovaphone
- Inte kategoriserad Intel
- Inte kategoriserad Futaba
- Inte kategoriserad Mamiya
- Inte kategoriserad MPM
- Inte kategoriserad Zuiver
- Inte kategoriserad Pentax
- Inte kategoriserad Fantec
- Inte kategoriserad Konig
- Inte kategoriserad Nextbase
- Inte kategoriserad Reloop
- Inte kategoriserad Delta
- Inte kategoriserad Valueline
- Inte kategoriserad Active Era
- Inte kategoriserad Rotel
- Inte kategoriserad Becken
- Inte kategoriserad Trigano
- Inte kategoriserad Icom
- Inte kategoriserad Chandler
- Inte kategoriserad Corel
- Inte kategoriserad Teac
- Inte kategoriserad Hozelock
- Inte kategoriserad Esatto
- Inte kategoriserad Sweex
- Inte kategoriserad Busch And Müller
- Inte kategoriserad Trevi
- Inte kategoriserad Reer
- Inte kategoriserad Vizio
- Inte kategoriserad Tesla
- Inte kategoriserad Schuberth
- Inte kategoriserad MSI
- Inte kategoriserad Rademacher
- Inte kategoriserad Char-Broil
- Inte kategoriserad Nebula
- Inte kategoriserad Cello
- Inte kategoriserad RDL
- Inte kategoriserad Foscam
- Inte kategoriserad Austrian Audio
- Inte kategoriserad Vakoss
- Inte kategoriserad Silkn
- Inte kategoriserad Eberspacher
- Inte kategoriserad Kress
- Inte kategoriserad Hobby
- Inte kategoriserad Busch-Jaeger
- Inte kategoriserad Zehnder
- Inte kategoriserad Sogo
- Inte kategoriserad Stihl
- Inte kategoriserad Laurastar
- Inte kategoriserad Bavaria
- Inte kategoriserad Mx Onda
- Inte kategoriserad Zenit
- Inte kategoriserad Orion
- Inte kategoriserad JL Audio
- Inte kategoriserad Juwel
- Inte kategoriserad Zebra
- Inte kategoriserad Wacker Neuson
- Inte kategoriserad Nûby
- Inte kategoriserad EVE
- Inte kategoriserad Wharfedale
- Inte kategoriserad Marvel
- Inte kategoriserad Magnat
- Inte kategoriserad Chord
- Inte kategoriserad Xterra
- Inte kategoriserad Soundcraft
- Inte kategoriserad Fredenstein
- Inte kategoriserad Viewsonic
- Inte kategoriserad Dolmar
- Inte kategoriserad Playmobil
- Inte kategoriserad Tesy
- Inte kategoriserad Invacare
- Inte kategoriserad Napoleon
- Inte kategoriserad Metronic
- Inte kategoriserad Nanni
- Inte kategoriserad Fuji
- Inte kategoriserad Swissonic
- Inte kategoriserad Razor
- Inte kategoriserad Schütte
- Inte kategoriserad Shindaiwa
- Inte kategoriserad Technaxx
- Inte kategoriserad D-Link
- Inte kategoriserad BRIO
- Inte kategoriserad Aruba
- Inte kategoriserad Waeco
- Inte kategoriserad Natec
- Inte kategoriserad Hobart
- Inte kategoriserad Fiio
- Inte kategoriserad RGV
- Inte kategoriserad Ikan
- Inte kategoriserad Elkay
- Inte kategoriserad IHealth
- Inte kategoriserad Hapro
- Inte kategoriserad Tamiya
- Inte kategoriserad Anthem
- Inte kategoriserad Mestic
- Inte kategoriserad Logicom
- Inte kategoriserad Swann
- Inte kategoriserad Alfen
- Inte kategoriserad Rexel
- Inte kategoriserad Sound Machines
- Inte kategoriserad Tepro
- Inte kategoriserad Team
- Inte kategoriserad Lionelo
- Inte kategoriserad Petsafe
- Inte kategoriserad Lezyne
- Inte kategoriserad Sunding
- Inte kategoriserad Nelson
- Inte kategoriserad Nilfisk
- Inte kategoriserad Foppapedretti
- Inte kategoriserad TranzX
- Inte kategoriserad Chauvet
- Inte kategoriserad Flex
- Inte kategoriserad Aviom
- Inte kategoriserad Tenda
- Inte kategoriserad Cooler Master
- Inte kategoriserad UPM
- Inte kategoriserad Happy Plugs
- Inte kategoriserad BABY Born
- Inte kategoriserad Miniland
- Inte kategoriserad Privileg
- Inte kategoriserad One For All
- Inte kategoriserad Dynacord
- Inte kategoriserad T'nB
- Inte kategoriserad ProfiCook
- Inte kategoriserad Ematic
- Inte kategoriserad Finder
- Inte kategoriserad Fluke
- Inte kategoriserad Levoit
- Inte kategoriserad Palm
- Inte kategoriserad QSC
- Inte kategoriserad Nivona
- Inte kategoriserad Vivax
- Inte kategoriserad Phonak
- Inte kategoriserad Winix
- Inte kategoriserad Emporia
- Inte kategoriserad Faber
- Inte kategoriserad Cardiostrong
- Inte kategoriserad Hartan
- Inte kategoriserad Hasbro
- Inte kategoriserad Hamax
- Inte kategoriserad Xavax
- Inte kategoriserad Emmaljunga
- Inte kategoriserad Fantini Cosmi
- Inte kategoriserad X4-Tech
- Inte kategoriserad Traxxas
- Inte kategoriserad Tracer
- Inte kategoriserad Audac
- Inte kategoriserad Cosori
- Inte kategoriserad Nevir
- Inte kategoriserad Eltako
- Inte kategoriserad Marmitek
- Inte kategoriserad Sekonic
- Inte kategoriserad Azden
- Inte kategoriserad Kyocera
- Inte kategoriserad Leifheit
- Inte kategoriserad Minox
- Inte kategoriserad Ilve
- Inte kategoriserad Crosscall
- Inte kategoriserad Countryman
- Inte kategoriserad Minolta
- Inte kategoriserad Aerial
- Inte kategoriserad Delta Dore
- Inte kategoriserad Navman
- Inte kategoriserad Prime3
- Inte kategoriserad Silver Cross
- Inte kategoriserad Victor
- Inte kategoriserad Zagg
- Inte kategoriserad ESI
- Inte kategoriserad Blumfeldt
- Inte kategoriserad SuperTooth
- Inte kategoriserad Grillmeister
- Inte kategoriserad M-e
- Inte kategoriserad Corsair
- Inte kategoriserad Edgestar
- Inte kategoriserad Orbis
- Inte kategoriserad ACE
- Inte kategoriserad Maxicool
- Inte kategoriserad For_Q
- Inte kategoriserad Schaudt
- Inte kategoriserad Avocor
- Inte kategoriserad Lanzar
- Inte kategoriserad DoorBird
- Inte kategoriserad KDK
- Inte kategoriserad FoodSaver
- Inte kategoriserad Vroomshoop
- Inte kategoriserad SureFlap
- Inte kategoriserad Lorex
- Inte kategoriserad GVM
- Inte kategoriserad McGregor
- Inte kategoriserad Coyote
- Inte kategoriserad Rain Bird
- Inte kategoriserad Leitz
- Inte kategoriserad Nvidia
- Inte kategoriserad Jilong
- Inte kategoriserad Teltonika
- Inte kategoriserad Vortex
- Inte kategoriserad Irritrol
- Inte kategoriserad Boneco
- Inte kategoriserad Ubiquiti Networks
- Inte kategoriserad Rapid
- Inte kategoriserad Simpson
- Inte kategoriserad Hertz
- Inte kategoriserad Exit
- Inte kategoriserad CaterChef
- Inte kategoriserad Echowell
- Inte kategoriserad Gys
- Inte kategoriserad Recaro
- Inte kategoriserad Zoom
- Inte kategoriserad Kasda
- Inte kategoriserad Marshall Electronics
- Inte kategoriserad Veho
- Inte kategoriserad Kambrook
- Inte kategoriserad EBERLE
- Inte kategoriserad Hartke
- Inte kategoriserad Nevadent
- Inte kategoriserad Plum
- Inte kategoriserad Simrad
- Inte kategoriserad Grasslin
- Inte kategoriserad Creative
- Inte kategoriserad Cellular Line
- Inte kategoriserad Puky
- Inte kategoriserad Jensen
- Inte kategoriserad GFI System
- Inte kategoriserad Omnitronic
- Inte kategoriserad Ctek
- Inte kategoriserad Roadstar
- Inte kategoriserad Humax
- Inte kategoriserad Eaton
- Inte kategoriserad Vaddio
- Inte kategoriserad Thrustmaster
- Inte kategoriserad G3 Ferrari
- Inte kategoriserad Berner
- Inte kategoriserad Zipper
- Inte kategoriserad Swarovski Optik
- Inte kategoriserad Gira
- Inte kategoriserad Scott
- Inte kategoriserad Caple
- Inte kategoriserad Jung
- Inte kategoriserad Mafell
- Inte kategoriserad Audiolab
- Inte kategoriserad Seagate
- Inte kategoriserad Greenworks
- Inte kategoriserad Vacmaster
- Inte kategoriserad Golden Age Project
- Inte kategoriserad Newstar
- Inte kategoriserad Harvia
- Inte kategoriserad Britax-Romer
- Inte kategoriserad Spin Master
- Inte kategoriserad Technicolor
- Inte kategoriserad Bravilor Bonamat
- Inte kategoriserad CyberPower
- Inte kategoriserad Huion
- Inte kategoriserad Fieldmann
- Inte kategoriserad Newline
- Inte kategoriserad Tronic
- Inte kategoriserad Blue
- Inte kategoriserad Efbe-schott
- Inte kategoriserad Brinsea
- Inte kategoriserad Genexis
- Inte kategoriserad Genelec
- Inte kategoriserad Sangean
- Inte kategoriserad Inspire
- Inte kategoriserad Gourmetmaxx
- Inte kategoriserad Basetech
- Inte kategoriserad Apart
- Inte kategoriserad Datalogic
- Inte kategoriserad Saramonic
- Inte kategoriserad Rode
- Inte kategoriserad Line 6
- Inte kategoriserad 4ms
- Inte kategoriserad Venta
- Inte kategoriserad Cadac
- Inte kategoriserad Anchor Audio
- Inte kategoriserad 4moms
- Inte kategoriserad Wolf
- Inte kategoriserad Dantherm
- Inte kategoriserad Polisport
- Inte kategoriserad Stabila
- Inte kategoriserad Hecht
- Inte kategoriserad Interlogix
- Inte kategoriserad Projecta
- Inte kategoriserad Eizo
- Inte kategoriserad Krontaler
- Inte kategoriserad Lyman
- Inte kategoriserad Etekcity
- Inte kategoriserad Genaray
- Inte kategoriserad Balance
- Inte kategoriserad Equator
- Inte kategoriserad Thermex
- Inte kategoriserad Zenec
- Inte kategoriserad Qualcast
- Inte kategoriserad TC Electronic
- Inte kategoriserad Cablexpert
- Inte kategoriserad Iomega
- Inte kategoriserad Ring
- Inte kategoriserad Phil And Teds
- Inte kategoriserad Tornado
- Inte kategoriserad Baby Jogger
- Inte kategoriserad Primus
- Inte kategoriserad Velux
- Inte kategoriserad GoDEX
- Inte kategoriserad Stelton
- Inte kategoriserad Synology
- Inte kategoriserad Mr Handsfree
- Inte kategoriserad Pattfield
- Inte kategoriserad Joovy
- Inte kategoriserad Sommer
- Inte kategoriserad Bodum
- Inte kategoriserad Saitek
- Inte kategoriserad DAS Audio
- Inte kategoriserad Bimar
- Inte kategoriserad Vivitar
- Inte kategoriserad Edilkamin
- Inte kategoriserad Vestfrost
- Inte kategoriserad Elac
- Inte kategoriserad Trendnet
- Inte kategoriserad DSC
- Inte kategoriserad Leen Bakker
- Inte kategoriserad Eventide
- Inte kategoriserad Steinberg
- Inte kategoriserad Audio Pro
- Inte kategoriserad OSO
- Inte kategoriserad JLab
- Inte kategoriserad Sevenoak
- Inte kategoriserad Roxio
- Inte kategoriserad Vermeiren
- Inte kategoriserad OnePlus
- Inte kategoriserad Kunft
- Inte kategoriserad Cambridge
- Inte kategoriserad Radial Engineering
- Inte kategoriserad Fito
- Inte kategoriserad Ewent
- Inte kategoriserad Jotul
- Inte kategoriserad Blackmagic Design
- Inte kategoriserad Mikrotik
- Inte kategoriserad Caso
- Inte kategoriserad Shoprider
- Inte kategoriserad WHALE
- Inte kategoriserad Shuttle
- Inte kategoriserad Furuno
- Inte kategoriserad HQ
- Inte kategoriserad Max
- Inte kategoriserad Brita
- Inte kategoriserad Be Cool
- Inte kategoriserad Autel
- Inte kategoriserad Clage
- Inte kategoriserad Tetra
- Inte kategoriserad Fluval
- Inte kategoriserad Noveen
- Inte kategoriserad Master
- Inte kategoriserad ATen
- Inte kategoriserad Dualit
- Inte kategoriserad Cre8audio
- Inte kategoriserad Nanlite
- Inte kategoriserad Fuxtec
- Inte kategoriserad Kupper
- Inte kategoriserad Bluesound
- Inte kategoriserad Ledger
- Inte kategoriserad Expobar
- Inte kategoriserad Koenig
- Inte kategoriserad Contour
- Inte kategoriserad BakkerElkhuizen
- Inte kategoriserad Lupilu
- Inte kategoriserad Showtec
- Inte kategoriserad Outdoorchef
- Inte kategoriserad Boyo
- Inte kategoriserad Nobo
- Inte kategoriserad IKRA
- Inte kategoriserad Turmix
- Inte kategoriserad Fakir
- Inte kategoriserad IOttie
- Inte kategoriserad Horizon Fitness
- Inte kategoriserad Profoto
- Inte kategoriserad Laserliner
- Inte kategoriserad BOYA
- Inte kategoriserad Veritas
- Inte kategoriserad Digi
- Inte kategoriserad Verizon
- Inte kategoriserad Astralpool
- Inte kategoriserad Ultimate
- Inte kategoriserad ADATA
- Inte kategoriserad XPG
- Inte kategoriserad Valco Baby
- Inte kategoriserad Trio Lighting
- Inte kategoriserad Argoclima
- Inte kategoriserad Integra
- Inte kategoriserad Upo
- Inte kategoriserad Vitamix
- Inte kategoriserad Metra
- Inte kategoriserad Xtorm
- Inte kategoriserad Blade
- Inte kategoriserad Hestan
- Inte kategoriserad Rio
- Inte kategoriserad Cadel
- Inte kategoriserad Baxi
- Inte kategoriserad ThinkFun
- Inte kategoriserad Ipevo
- Inte kategoriserad Rommer
- Inte kategoriserad Mophie
- Inte kategoriserad Fibaro
- Inte kategoriserad Princeton Tec
- Inte kategoriserad Iget
- Inte kategoriserad Revox
- Inte kategoriserad Emtec
- Inte kategoriserad Ranex
- Inte kategoriserad Russound
- Inte kategoriserad Truper
- Inte kategoriserad Easy Home
- Inte kategoriserad ISDT
- Inte kategoriserad Abac
- Inte kategoriserad Stannah
- Inte kategoriserad Celly
- Inte kategoriserad Kindermann
- Inte kategoriserad Comica
- Inte kategoriserad CRUX
- Inte kategoriserad Tommee Tippee
- Inte kategoriserad Globo
- Inte kategoriserad Conceptronic
- Inte kategoriserad ZLine
- Inte kategoriserad EverFocus
- Inte kategoriserad Watson
- Inte kategoriserad Fusion
- Inte kategoriserad Eurolite
- Inte kategoriserad Sebo
- Inte kategoriserad Audient
- Inte kategoriserad Heller
- Inte kategoriserad Geemarc
- Inte kategoriserad Vornado
- Inte kategoriserad Adesso
- Inte kategoriserad Hegel
- Inte kategoriserad Paradigm
- Inte kategoriserad Infantino
- Inte kategoriserad RGBlink
- Inte kategoriserad Gefen
- Inte kategoriserad C3
- Inte kategoriserad Nexa
- Inte kategoriserad Reebok
- Inte kategoriserad EMSA
- Inte kategoriserad Waldbeck
- Inte kategoriserad Natuzzi
- Inte kategoriserad Grunkel
- Inte kategoriserad Satel
- Inte kategoriserad Scosche
- Inte kategoriserad Bazooka
- Inte kategoriserad PAX
- Inte kategoriserad K&K Sound
- Inte kategoriserad Vivotek
- Inte kategoriserad Dutchbone
- Inte kategoriserad MyPhone
- Inte kategoriserad Fanvil
- Inte kategoriserad Noise Engineering
- Inte kategoriserad PAC
- Inte kategoriserad Beretta
- Inte kategoriserad Wentronic
- Inte kategoriserad Peerless
- Inte kategoriserad RAVPower
- Inte kategoriserad Mooer
- Inte kategoriserad Hooker
- Inte kategoriserad Polti
- Inte kategoriserad Dynaudio
- Inte kategoriserad Terratec
- Inte kategoriserad IHome
- Inte kategoriserad August
- Inte kategoriserad Atomos
- Inte kategoriserad Luxman
- Inte kategoriserad Dormakaba
- Inte kategoriserad Adder
- Inte kategoriserad Gitzo
- Inte kategoriserad M-Audio
- Inte kategoriserad SeaLife
- Inte kategoriserad Infinity
- Inte kategoriserad DBX
- Inte kategoriserad Nesco
- Inte kategoriserad Wago
- Inte kategoriserad AIC
- Inte kategoriserad ECS
- Inte kategoriserad Concept2
- Inte kategoriserad Cleanmaxx
- Inte kategoriserad Dali
- Inte kategoriserad Brydge
- Inte kategoriserad Smart
- Inte kategoriserad Selec
- Inte kategoriserad Aiphone
- Inte kategoriserad Tivoli Audio
- Inte kategoriserad Senal
- Inte kategoriserad JETI
- Inte kategoriserad Waves
- Inte kategoriserad EQ3
- Inte kategoriserad Karlik
- Inte kategoriserad Comark
- Inte kategoriserad Homematic IP
- Inte kategoriserad Lervia
- Inte kategoriserad Coline
- Inte kategoriserad N8WERK
- Inte kategoriserad Petri
- Inte kategoriserad Calex
- Inte kategoriserad Scancool
- Inte kategoriserad Satechi
- Inte kategoriserad REV
- Inte kategoriserad Skullcandy
- Inte kategoriserad Hansgrohe
- Inte kategoriserad Masport
- Inte kategoriserad Jamo
- Inte kategoriserad NZXT
- Inte kategoriserad Veripart
- Inte kategoriserad Grizzly
- Inte kategoriserad Rocktrail
- Inte kategoriserad 4smarts
- Inte kategoriserad ILive
- Inte kategoriserad Xaoc
- Inte kategoriserad Beyerdynamic
- Inte kategoriserad Oppo
- Inte kategoriserad Qute
- Inte kategoriserad Syma
- Inte kategoriserad Schwinn
- Inte kategoriserad Victrola
- Inte kategoriserad Lanberg
- Inte kategoriserad Friedland
- Inte kategoriserad Kopul
- Inte kategoriserad AENO
- Inte kategoriserad Interstuhl
- Inte kategoriserad Proaim
- Inte kategoriserad Megableu
- Inte kategoriserad Nexxt
- Inte kategoriserad Coleman
- Inte kategoriserad Bora
- Inte kategoriserad Magic Care
- Inte kategoriserad Raclet
- Inte kategoriserad Butler
- Inte kategoriserad Intenso
- Inte kategoriserad Weishaupt
- Inte kategoriserad Hammond
- Inte kategoriserad Testo
- Inte kategoriserad Glock
- Inte kategoriserad Revo
- Inte kategoriserad Baby Lock
- Inte kategoriserad Linn
- Inte kategoriserad Martin Logan
- Inte kategoriserad Quantum
- Inte kategoriserad Swift
- Inte kategoriserad Elta
- Inte kategoriserad Iluv
- Inte kategoriserad Monitor Audio
- Inte kategoriserad Vorago
- Inte kategoriserad REMKO
- Inte kategoriserad Anton/Bauer
- Inte kategoriserad Monoprice
- Inte kategoriserad Ibiza Sound
- Inte kategoriserad Echo
- Inte kategoriserad Croozer
- Inte kategoriserad TELEX
- Inte kategoriserad Dynamic
- Inte kategoriserad Sauter
- Inte kategoriserad Promethean
- Inte kategoriserad HyperIce
- Inte kategoriserad Home Easy
- Inte kategoriserad Clean Air Optima
- Inte kategoriserad Basil
- Inte kategoriserad Chipolino
- Inte kategoriserad Munchkin
- Inte kategoriserad Solo
- Inte kategoriserad Vitalmaxx
- Inte kategoriserad Yorkville
- Inte kategoriserad Nxg
- Inte kategoriserad AGM
- Inte kategoriserad DPA
- Inte kategoriserad Autodesk
- Inte kategoriserad Cocraft
- Inte kategoriserad Diana
- Inte kategoriserad Tandberg Data
- Inte kategoriserad Toyotomi
- Inte kategoriserad GA.MA
- Inte kategoriserad Plustek
- Inte kategoriserad Prowise
- Inte kategoriserad Impact
- Inte kategoriserad Areca
- Inte kategoriserad Mousetrapper
- Inte kategoriserad SKROSS
- Inte kategoriserad Sikkens
- Inte kategoriserad DEXP
- Inte kategoriserad Burris
- Inte kategoriserad GolfBuddy
- Inte kategoriserad Lynx
- Inte kategoriserad Barazza
- Inte kategoriserad Vantec
- Inte kategoriserad Proel
- Inte kategoriserad FBT
- Inte kategoriserad Tiptel
- Inte kategoriserad Roccat
- Inte kategoriserad Thermor
- Inte kategoriserad NodOn
- Inte kategoriserad Edge
- Inte kategoriserad Endorphin.es
- Inte kategoriserad Crofton
- Inte kategoriserad Deutz
- Inte kategoriserad Optimum
- Inte kategoriserad FIMI
- Inte kategoriserad MIPRO
- Inte kategoriserad Flavel
- Inte kategoriserad Bravilor
- Inte kategoriserad HQ Power
- Inte kategoriserad Bracketron
- Inte kategoriserad Solid State Logic
- Inte kategoriserad Pointer
- Inte kategoriserad XYZprinting
- Inte kategoriserad HyperX
- Inte kategoriserad Computherm
- Inte kategoriserad Edision
- Inte kategoriserad ICE Watch
- Inte kategoriserad Carmen
- Inte kategoriserad MTM
- Inte kategoriserad X-Sense
- Inte kategoriserad Broan
- Inte kategoriserad Avidsen
- Inte kategoriserad De Buyer
- Inte kategoriserad Metapace
- Inte kategoriserad Cougar
- Inte kategoriserad Zeiss
- Inte kategoriserad Neets
- Inte kategoriserad Beaba
- Inte kategoriserad NAV-TV
- Inte kategoriserad Wooden Camera
- Inte kategoriserad Maclaren
- Inte kategoriserad Stamina
- Inte kategoriserad AdHoc
- Inte kategoriserad Chief
- Inte kategoriserad SEH
- Inte kategoriserad AudioQuest
- Inte kategoriserad Eurochron
- Inte kategoriserad Powerblade
- Inte kategoriserad HiFi ROSE
- Inte kategoriserad Hayter
- Inte kategoriserad Furrion
- Inte kategoriserad Pinolino
- Inte kategoriserad Cecotec
- Inte kategoriserad Antari
- Inte kategoriserad Gianni Ferrari
- Inte kategoriserad OSD Audio
- Inte kategoriserad WMD
- Inte kategoriserad Andover
- Inte kategoriserad Simpark
- Inte kategoriserad Arctic Cooling
- Inte kategoriserad Beafon
- Inte kategoriserad Maruyama
- Inte kategoriserad SPC
- Inte kategoriserad Stabo
- Inte kategoriserad Blackstar
- Inte kategoriserad Oreck
- Inte kategoriserad FABER CASTELL
- Inte kategoriserad Ergotron
- Inte kategoriserad Stairville
- Inte kategoriserad Zepter
- Inte kategoriserad Crestron
- Inte kategoriserad Giordani
- Inte kategoriserad RME
- Inte kategoriserad Black Lion Audio
- Inte kategoriserad Cowon
- Inte kategoriserad Soundstream
- Inte kategoriserad Crayola
- Inte kategoriserad Fischer
- Inte kategoriserad Xoro
- Inte kategoriserad Medel
- Inte kategoriserad Livington
- Inte kategoriserad REVITIVE
- Inte kategoriserad Herkules
- Inte kategoriserad CTOUCH
- Inte kategoriserad Instant
- Inte kategoriserad Adastra
- Inte kategoriserad Gabor
- Inte kategoriserad Konig & Meyer
- Inte kategoriserad Meister Craft
- Inte kategoriserad Meade
- Inte kategoriserad Unify
- Inte kategoriserad Sagemcom
- Inte kategoriserad Yeastar
- Inte kategoriserad Laserworld
- Inte kategoriserad Billow
- Inte kategoriserad Chuango
- Inte kategoriserad Kelty
- Inte kategoriserad West Elm
- Inte kategoriserad Block
- Inte kategoriserad Keter
- Inte kategoriserad Hori
- Inte kategoriserad Ozone
- Inte kategoriserad Truelife
- Inte kategoriserad Bikemate
- Inte kategoriserad Klavis
- Inte kategoriserad Garden Lights
- Inte kategoriserad Monster
- Inte kategoriserad ORNO
- Inte kategoriserad ETiger
- Inte kategoriserad Jabsco
- Inte kategoriserad Dash
- Inte kategoriserad Yukon
- Inte kategoriserad Foxconn
- Inte kategoriserad Segway
- Inte kategoriserad Icy Dock
- Inte kategoriserad Wasco
- Inte kategoriserad IMC Toys
- Inte kategoriserad Baby Brezza
- Inte kategoriserad Make Noise
- Inte kategoriserad Toolcraft
- Inte kategoriserad Telstra
- Inte kategoriserad TeachLogic
- Inte kategoriserad Maytronics
- Inte kategoriserad ASSA ABLOY
- Inte kategoriserad Sole Fitness
- Inte kategoriserad Power Dynamics
- Inte kategoriserad Lumag
- Inte kategoriserad Charge Amps
- Inte kategoriserad Berker
- Inte kategoriserad Eufab
- Inte kategoriserad Manfrotto
- Inte kategoriserad Crucial
- Inte kategoriserad Snom
- Inte kategoriserad RIDGID
- Inte kategoriserad Premier
- Inte kategoriserad Aeon Labs
- Inte kategoriserad Ibm
- Inte kategoriserad Unilux
- Inte kategoriserad Shokz
- Inte kategoriserad Citronic
- Inte kategoriserad Pontec
- Inte kategoriserad Maxell
- Inte kategoriserad Cosatto
- Inte kategoriserad Weasy
- Inte kategoriserad Aerotec
- Inte kategoriserad Atlas
- Inte kategoriserad Datacard
- Inte kategoriserad Dreamgear
- Inte kategoriserad ZYCOO
- Inte kategoriserad Macrom
- Inte kategoriserad Kontakt Chemie
- Inte kategoriserad Purell
- Inte kategoriserad Riccar
- Inte kategoriserad Contax
- Inte kategoriserad OpenVox
- Inte kategoriserad Electro Harmonix
- Inte kategoriserad Erica Synths
- Inte kategoriserad SkyRC
- Inte kategoriserad Atdec
- Inte kategoriserad Grandstream
- Inte kategoriserad Batavia
- Inte kategoriserad Klarfit
- Inte kategoriserad Proxxon
- Inte kategoriserad Kalorik
- Inte kategoriserad Mercury
- Inte kategoriserad Gutfels
- Inte kategoriserad Marklin
- Inte kategoriserad Bruynzeel
- Inte kategoriserad Toro
- Inte kategoriserad Definitive Technology
- Inte kategoriserad Fender
- Inte kategoriserad Gardenline
- Inte kategoriserad MSpa
- Inte kategoriserad View Quest
- Inte kategoriserad Drayton
- Inte kategoriserad Crane
- Inte kategoriserad Formuler
- Inte kategoriserad Maximum
- Inte kategoriserad Eden
- Inte kategoriserad Sonnet
- Inte kategoriserad Oertli
- Inte kategoriserad UX
- Inte kategoriserad Moog
- Inte kategoriserad Buzz Rack
- Inte kategoriserad Cruz
- Inte kategoriserad Nerf
- Inte kategoriserad Gamdias
- Inte kategoriserad KidKraft
- Inte kategoriserad SPL
- Inte kategoriserad Westfalia
- Inte kategoriserad Monacor
- Inte kategoriserad Metrel
- Inte kategoriserad Multimetrix
- Inte kategoriserad Solid
- Inte kategoriserad NUK
- Inte kategoriserad Morris
- Inte kategoriserad Ruger
- Inte kategoriserad Aputure
- Inte kategoriserad Gerni
- Inte kategoriserad Jupio
- Inte kategoriserad PCE
- Inte kategoriserad MedFolio
- Inte kategoriserad Baby Annabell
- Inte kategoriserad Warm Audio
- Inte kategoriserad Brandson
- Inte kategoriserad Heatit
- Inte kategoriserad Endress
- Inte kategoriserad Deaf Bonce
- Inte kategoriserad ProForm
- Inte kategoriserad UTEPO
- Inte kategoriserad Lindell Audio
- Inte kategoriserad ARRI
- Inte kategoriserad Max Pro
- Inte kategoriserad Think Tank
- Inte kategoriserad Portech
- Inte kategoriserad Twelve South
- Inte kategoriserad Lec
- Inte kategoriserad Geomag
- Inte kategoriserad LTC
- Inte kategoriserad Martin
- Inte kategoriserad Koala
- Inte kategoriserad Drawmer
- Inte kategoriserad Audeze
- Inte kategoriserad Blue Sky
- Inte kategoriserad Dunlop
- Inte kategoriserad Valeo
- Inte kategoriserad Noxon
- Inte kategoriserad GW Instek
- Inte kategoriserad Galanz
- Inte kategoriserad Velbus
- Inte kategoriserad Babyzen
- Inte kategoriserad Logilink
- Inte kategoriserad Woonexpress
- Inte kategoriserad IQAir
- Inte kategoriserad Sanus Systems
- Inte kategoriserad BabyDan
- Inte kategoriserad ColorKey
- Inte kategoriserad Tormatic
- Inte kategoriserad After Later Audio
- Inte kategoriserad Aqara
- Inte kategoriserad Verbatim
- Inte kategoriserad 2hp
- Inte kategoriserad Energizer
- Inte kategoriserad Samlex
- Inte kategoriserad Navionics
- Inte kategoriserad AirTurn
- Inte kategoriserad Zalman
- Inte kategoriserad Turbo Air
- Inte kategoriserad Zega
- Inte kategoriserad Leatherman
- Inte kategoriserad Khind
- Inte kategoriserad Havis
- Inte kategoriserad Orava
- Inte kategoriserad Horizon
- Inte kategoriserad Gastronoma
- Inte kategoriserad Moxa
- Inte kategoriserad Ultimate Support
- Inte kategoriserad POLARIS
- Inte kategoriserad Rösle
- Inte kategoriserad Interphone
- Inte kategoriserad Smart-AVI
- Inte kategoriserad Osram
- Inte kategoriserad StarTech.com
- Inte kategoriserad AXI
- Inte kategoriserad Inter-Tech
- Inte kategoriserad Thomann
- Inte kategoriserad Holzmann
- Inte kategoriserad EMG
- Inte kategoriserad James
- Inte kategoriserad Bicker Elektronik
- Inte kategoriserad Iadea
- Inte kategoriserad Blizzard
- Inte kategoriserad Geneva
- Inte kategoriserad Nimble
- Inte kategoriserad SIIG
- Inte kategoriserad Reginox
- Inte kategoriserad BIOS Medical
- Inte kategoriserad Eero
- Inte kategoriserad Realme
- Inte kategoriserad Advantech
- Inte kategoriserad PSSO
- Inte kategoriserad Levenhuk
- Inte kategoriserad Wise
- Inte kategoriserad SIG Sauer
- Inte kategoriserad Merkel
- Inte kategoriserad Patching Panda
- Inte kategoriserad Harley Benton
- Inte kategoriserad Biohort
- Inte kategoriserad Crest Audio
- Inte kategoriserad Globe
- Inte kategoriserad Rossi
- Inte kategoriserad IOGEAR
- Inte kategoriserad Hercules
- Inte kategoriserad Grace Design
- Inte kategoriserad Contour Design
- Inte kategoriserad Heckler Design
- Inte kategoriserad Propellerhead
- Inte kategoriserad Nanuk
- Inte kategoriserad Digital Watchdog
- Inte kategoriserad Sonifex
- Inte kategoriserad Riviera And Bar
- Inte kategoriserad Apelson
- Inte kategoriserad EcoFlow
- Inte kategoriserad Kreiling
- Inte kategoriserad Xantech
- Inte kategoriserad Scanstrut
- Inte kategoriserad Kohler
- Inte kategoriserad Safco
- Inte kategoriserad Xunzel
- Inte kategoriserad Fein
- Inte kategoriserad Oklahoma Sound
- Inte kategoriserad Thames & Kosmos
- Inte kategoriserad Kali Audio
- Inte kategoriserad Audioengine
- Inte kategoriserad Fortia
- Inte kategoriserad Moen
- Inte kategoriserad IFi Audio
- Inte kategoriserad Babysense
- Inte kategoriserad Namco Bandai Games
- Inte kategoriserad Witt
- Inte kategoriserad Revel
- Inte kategoriserad Sealy
- Inte kategoriserad Ferguson
- Inte kategoriserad Wet Sounds
- Inte kategoriserad CRU
- Inte kategoriserad Avantone Pro
- Inte kategoriserad Sanitaire
- Inte kategoriserad Umarex
- Inte kategoriserad Televés
- Inte kategoriserad AbleNet
- Inte kategoriserad Exalux
- Inte kategoriserad IBasso
- Inte kategoriserad Bolt
- Inte kategoriserad Leap Frog
- Inte kategoriserad Sightmark
- Inte kategoriserad Eissound
- Inte kategoriserad Ganz
- Inte kategoriserad Hughes & Kettner
- Inte kategoriserad Manley
- Inte kategoriserad JOBY
- Inte kategoriserad Micro Matic
- Inte kategoriserad Audix
- Inte kategoriserad MEE Audio
- Inte kategoriserad DAP Audio
- Inte kategoriserad Thermomate
- Inte kategoriserad Steiner
- Inte kategoriserad Kingston
- Inte kategoriserad Acard
- Inte kategoriserad NordicTrack
- Inte kategoriserad Burigotto
- Inte kategoriserad Redmond
- Inte kategoriserad Sencys
- Inte kategoriserad Norton Clipper
- Inte kategoriserad Extron
- Inte kategoriserad KanexPro
- Inte kategoriserad Blustream
- Inte kategoriserad Avocent
- Inte kategoriserad Geze
- Inte kategoriserad SVS
- Inte kategoriserad Franklin
- Inte kategoriserad RTS
- Inte kategoriserad Ontech
- Inte kategoriserad HyperJuice
- Inte kategoriserad Koss
- Inte kategoriserad Swingline
- Inte kategoriserad Kwikset
- Inte kategoriserad Infomir
- Inte kategoriserad RaySafe
- Inte kategoriserad Di4
- Inte kategoriserad Hohner
- Inte kategoriserad Dahle
- Inte kategoriserad Ashly
- Inte kategoriserad Sanli
- Inte kategoriserad Shelly
- Inte kategoriserad Husky
- Inte kategoriserad Philos
- Inte kategoriserad Legamaster
- Inte kategoriserad Antec
- Inte kategoriserad Elmo
- Inte kategoriserad Siemon
- Inte kategoriserad Block & Block
- Inte kategoriserad Brondell
- Inte kategoriserad NutriBullet
- Inte kategoriserad Four Hands
- Inte kategoriserad Oregon Scientific
- Inte kategoriserad Oben
- Inte kategoriserad ASA
- Inte kategoriserad XGIMI
- Inte kategoriserad Thronmax
- Inte kategoriserad Axkid
- Inte kategoriserad Botex
- Inte kategoriserad Intellinet
- Inte kategoriserad Maxsa
- Inte kategoriserad Park Tool
- Inte kategoriserad Tripp
- Inte kategoriserad TRIUS
- Inte kategoriserad Ankarsrum
- Inte kategoriserad MTD
- Inte kategoriserad Dangerous Music
- Inte kategoriserad Etymotic
- Inte kategoriserad Foster
- Inte kategoriserad Fine Dine
- Inte kategoriserad ClearOne
- Inte kategoriserad Everdure
- Inte kategoriserad ELO
- Inte kategoriserad Heidemann
- Inte kategoriserad OneTouch
- Inte kategoriserad Medeli
- Inte kategoriserad Superrollo
- Inte kategoriserad Goldtouch
- Inte kategoriserad Gamewright
- Inte kategoriserad Kerbl
- Inte kategoriserad Reflexion
- Inte kategoriserad Roidmi
- Inte kategoriserad Braun Phototechnik
- Inte kategoriserad Black Decker
- Inte kategoriserad Muller
- Inte kategoriserad Scala
- Inte kategoriserad SXT
- Inte kategoriserad Essenza
- Inte kategoriserad Seecode
- Inte kategoriserad Thomas
- Inte kategoriserad Duronic
- Inte kategoriserad Rugged Geek
- Inte kategoriserad Nubert
- Inte kategoriserad Dave Smith
- Inte kategoriserad Skymaster
- Inte kategoriserad Lancom
- Inte kategoriserad Dorr
- Inte kategoriserad PATLITE
- Inte kategoriserad Minn Kota
- Inte kategoriserad Lian Li
- Inte kategoriserad Match
- Inte kategoriserad Vocopro
- Inte kategoriserad Gardol
- Inte kategoriserad Helix
- Inte kategoriserad TFA Dostmann
- Inte kategoriserad Werma
- Inte kategoriserad Walrus Audio
- Inte kategoriserad Durable
- Inte kategoriserad Zenza Bronica
- Inte kategoriserad Spypoint
- Inte kategoriserad Greisinger
- Inte kategoriserad Suprema
- Inte kategoriserad Ziehl
- Inte kategoriserad VAIS
- Inte kategoriserad Revlon
- Inte kategoriserad Glide Gear
- Inte kategoriserad Perma
- Inte kategoriserad Scandes
- Inte kategoriserad ModeCom
- Inte kategoriserad Testec
- Inte kategoriserad Enovate
- Inte kategoriserad Lofrans
- Inte kategoriserad Winegard
- Inte kategoriserad Pigtronix
- Inte kategoriserad ProTeam
- Inte kategoriserad Wagner SprayTech
- Inte kategoriserad Libec
- Inte kategoriserad Hoshizaki
- Inte kategoriserad Pardini
- Inte kategoriserad Ledlenser
- Inte kategoriserad Beha-Amprobe
- Inte kategoriserad KWC
- Inte kategoriserad Soul
- Inte kategoriserad Laney
- Inte kategoriserad Compex
- Inte kategoriserad BirdDog
- Inte kategoriserad Theragun
- Inte kategoriserad Weil
- Inte kategoriserad Plantiflor
- Inte kategoriserad LAS
- Inte kategoriserad Rosseto
- Inte kategoriserad Redrock Micro
- Inte kategoriserad Motu
- Inte kategoriserad Kata
- Inte kategoriserad Minix
- Inte kategoriserad Lazer
- Inte kategoriserad EarthQuaker Devices
- Inte kategoriserad AVer
- Inte kategoriserad The Grainfather
- Inte kategoriserad Kessler
- Inte kategoriserad Emga
- Inte kategoriserad Devialet
- Inte kategoriserad Briggs & Stratton
- Inte kategoriserad USAopoly
- Inte kategoriserad Gami
- Inte kategoriserad Igloohome
- Inte kategoriserad Kenko
- Inte kategoriserad Zennio
- Inte kategoriserad Vixen
- Inte kategoriserad B-tech
- Inte kategoriserad Praktica
- Inte kategoriserad WAGAN
- Inte kategoriserad Elinchrom
- Inte kategoriserad Kopp
- Inte kategoriserad Boori
- Inte kategoriserad Universal Audio
- Inte kategoriserad CamRanger
- Inte kategoriserad ETON
- Inte kategoriserad Hasselblad
- Inte kategoriserad Madrix
- Inte kategoriserad ResMed
- Inte kategoriserad Q Acoustics
- Inte kategoriserad Spacedec
- Inte kategoriserad Auray
- Inte kategoriserad Bontempi
- Inte kategoriserad Furman
- Inte kategoriserad Summer Infant
- Inte kategoriserad Cooper & Quint
- Inte kategoriserad Infasecure
- Inte kategoriserad Deltex
- Inte kategoriserad Adax
- Inte kategoriserad Thinkware
- Inte kategoriserad Xplora
- Inte kategoriserad Eonon
- Inte kategoriserad SMC
- Inte kategoriserad Crimson
- Inte kategoriserad Ibico
- Inte kategoriserad OXO Good Grips
- Inte kategoriserad Exit Toys
- Inte kategoriserad Lifespan
- Inte kategoriserad Triton
- Inte kategoriserad Profizelt24
- Inte kategoriserad Helios Preisser
- Inte kategoriserad YSI
- Inte kategoriserad Yeyian
- Inte kategoriserad Paulmann
- Inte kategoriserad Nitek
- Inte kategoriserad Snoes
- Inte kategoriserad Alpatronix
- Inte kategoriserad Labelmate
- Inte kategoriserad Playtive
- Inte kategoriserad Martin Audio
- Inte kategoriserad Schertler
- Inte kategoriserad Teradek
- Inte kategoriserad Kern
- Inte kategoriserad Sissel
- Inte kategoriserad Kunath
- Inte kategoriserad Vimar
- Inte kategoriserad Penclic
- Inte kategoriserad Escort
- Inte kategoriserad SolarEdge
- Inte kategoriserad GOgroove
- Inte kategoriserad ViewCast
- Inte kategoriserad Crown
- Inte kategoriserad Kogan
- Inte kategoriserad Wolfcraft
- Inte kategoriserad Tennsco
- Inte kategoriserad FireKing
- Inte kategoriserad Tannoy
- Inte kategoriserad RAM Mounts
- Inte kategoriserad Ocean Matrix
- Inte kategoriserad Novus
- Inte kategoriserad Dedra
- Inte kategoriserad Getac
- Inte kategoriserad Arebos
- Inte kategoriserad Kreg
- Inte kategoriserad Bentley
- Inte kategoriserad Morningstar
- Inte kategoriserad DMax
- Inte kategoriserad Lenoxx
- Inte kategoriserad Speco Technologies
- Inte kategoriserad Backyard Discovery
- Inte kategoriserad Minuteman
- Inte kategoriserad Brady
- Inte kategoriserad Ortofon
- Inte kategoriserad Cameo
- Inte kategoriserad RéVive
- Inte kategoriserad ZKTeco
- Inte kategoriserad Mega
- Inte kategoriserad Esperanza
- Inte kategoriserad PowerXL
- Inte kategoriserad Star Micronics
- Inte kategoriserad Kemo
- Inte kategoriserad Tamron
- Inte kategoriserad Woodland Scenics
- Inte kategoriserad Chapin
- Inte kategoriserad Morel
- Inte kategoriserad Gloria
- Inte kategoriserad J. Rockett Audio Designs
- Inte kategoriserad Pancontrol
- Inte kategoriserad Satisfyer
- Inte kategoriserad Hämmerli
- Inte kategoriserad Verto
- Inte kategoriserad Maxcom
- Inte kategoriserad Soma
- Inte kategoriserad Posiflex
- Inte kategoriserad SRS
- Inte kategoriserad Little Giant
- Inte kategoriserad Signature
- Inte kategoriserad Point 65
- Inte kategoriserad ReTrak
- Inte kategoriserad Avantree
- Inte kategoriserad Akuvox
- Inte kategoriserad LYYT
- Inte kategoriserad Jay-tech
- Inte kategoriserad Old Blood Noise
- Inte kategoriserad Vulcan
- Inte kategoriserad CradlePoint
- Inte kategoriserad GAO
- Inte kategoriserad Rovo Kids
- Inte kategoriserad Catalyst
- Inte kategoriserad Uni-T
- Inte kategoriserad Dension
- Inte kategoriserad Antelope Audio
- Inte kategoriserad Kugoo
- Inte kategoriserad Brinno
- Inte kategoriserad Venom
- Inte kategoriserad H-Tronic
- Inte kategoriserad CE Labs
- Inte kategoriserad Mean Well
- Inte kategoriserad Legrand
- Inte kategoriserad Z CAM
- Inte kategoriserad Digium
- Inte kategoriserad Giardino
- Inte kategoriserad Mulex
- Inte kategoriserad Panduit
- Inte kategoriserad Raymarine
- Inte kategoriserad Novation
- Inte kategoriserad I.safe Mobile
- Inte kategoriserad Socomec
- Inte kategoriserad System Sensor
- Inte kategoriserad San Jamar
- Inte kategoriserad Fiskars
- Inte kategoriserad REL Acoustics
- Inte kategoriserad IPort
- Inte kategoriserad X-Rite
- Inte kategoriserad Wetelux
- Inte kategoriserad Talkaphone
- Inte kategoriserad Merax
- Inte kategoriserad GermGuardian
- Inte kategoriserad R-Go Tools
- Inte kategoriserad Urbanista
- Inte kategoriserad SLV
- Inte kategoriserad Sagitter
- Inte kategoriserad Rainbow
- Inte kategoriserad Duracell
- Inte kategoriserad Riello
- Inte kategoriserad Gagato
- Inte kategoriserad Traeger
- Inte kategoriserad General
- Inte kategoriserad Ooni
- Inte kategoriserad ECTIVE
- Inte kategoriserad Elgato
- Inte kategoriserad Gymform
- Inte kategoriserad Savio
- Inte kategoriserad Ebro
- Inte kategoriserad Doffler
- Inte kategoriserad Tzumi
- Inte kategoriserad BERTSCHAT
- Inte kategoriserad Schumacher
- Inte kategoriserad Michael Todd Beauty
- Inte kategoriserad Cygnett
- Inte kategoriserad Germania
- Inte kategoriserad Victorio
- Inte kategoriserad Platinum
- Inte kategoriserad Foreo
- Inte kategoriserad Trimble
- Inte kategoriserad JAYS
- Inte kategoriserad Playtive Junior
- Inte kategoriserad Intertechno
- Inte kategoriserad Parklands
- Inte kategoriserad Avid
- Inte kategoriserad Vipack
- Inte kategoriserad Helios
- Inte kategoriserad Schwaiger
- Inte kategoriserad Consul
- Inte kategoriserad EKO
- Inte kategoriserad BIG
- Inte kategoriserad Emeril Lagasse
- Inte kategoriserad SureFire
- Inte kategoriserad POGS
- Inte kategoriserad Graflex
- Inte kategoriserad Coolaroo
- Inte kategoriserad Insta360
- Inte kategoriserad Hikmicro
- Inte kategoriserad Wurth
- Inte kategoriserad Ketron
- Inte kategoriserad Mebus
- Inte kategoriserad Gioteck
- Inte kategoriserad Kenton
- Inte kategoriserad Cypress
- Inte kategoriserad Foliatec
- Inte kategoriserad Mauser
- Inte kategoriserad Silhouette
- Inte kategoriserad South Shore
- Inte kategoriserad Discovery
- Inte kategoriserad T4E
- Inte kategoriserad Speck
- Inte kategoriserad Generation
- Inte kategoriserad Iseki
- Inte kategoriserad 8BitDo
- Inte kategoriserad MOZA
- Inte kategoriserad Ecler
- Inte kategoriserad Turbosound
- Inte kategoriserad Phase One
- Inte kategoriserad Röhm
- Inte kategoriserad Ulanzi
- Inte kategoriserad Bluetti
- Inte kategoriserad Tineco
- Inte kategoriserad Anova
- Inte kategoriserad Viscount
- Inte kategoriserad Hurricane
- Inte kategoriserad JennAir
- Inte kategoriserad Newland
- Inte kategoriserad DAB
- Inte kategoriserad Anex
- Inte kategoriserad Flama
- Inte kategoriserad Pawa
- Inte kategoriserad V-Tac
- Inte kategoriserad LERAN
- Inte kategoriserad Majella
- Inte kategoriserad GMB Audio
- Inte kategoriserad Ashdown Engineering
- Inte kategoriserad Century
- Inte kategoriserad EQ-3
- Inte kategoriserad Unger
- Inte kategoriserad Naim
- Inte kategoriserad Inverto
- Inte kategoriserad Special-T
- Inte kategoriserad Ygnis
- Inte kategoriserad Esotec
- Inte kategoriserad True & Tidy
- Inte kategoriserad NovaStar
- Inte kategoriserad Petkit
- Inte kategoriserad Icon
- Inte kategoriserad Fuzzix
- Inte kategoriserad Kitchen Brains
- Inte kategoriserad Challenge Xtreme
- Inte kategoriserad Best
- Inte kategoriserad Flycam
- Inte kategoriserad NetAlly
- Inte kategoriserad Triax
- Inte kategoriserad Peltor
- Inte kategoriserad JAR Systems
- Inte kategoriserad Global
- Inte kategoriserad Moleskine
- Inte kategoriserad Bytecc
- Inte kategoriserad Strex
- Inte kategoriserad Xlyne
- Inte kategoriserad Premier Mounts
- Inte kategoriserad One Stop Systems
- Inte kategoriserad Cool Maker
- Inte kategoriserad PeakTech
- Inte kategoriserad Neo
- Inte kategoriserad EVOline
- Inte kategoriserad Mtx Audio
- Inte kategoriserad Ursus Trotter
- Inte kategoriserad DoughXpress
- Inte kategoriserad Ground Zero
- Inte kategoriserad Aquatic AV
- Inte kategoriserad Parasound
- Inte kategoriserad MSR
- Inte kategoriserad Keurig
- Inte kategoriserad Gravity
- Inte kategoriserad Cabstone
- Inte kategoriserad SPT
- Inte kategoriserad DB Technologies
- Inte kategoriserad T.I.P.
- Inte kategoriserad Promate
- Inte kategoriserad Sonel
- Inte kategoriserad Berger & Schröter
- Inte kategoriserad Tru Components
- Inte kategoriserad Step2
- Inte kategoriserad Crystal Quest
- Inte kategoriserad Emko
- Inte kategoriserad Mistral
- Inte kategoriserad Pit Boss
- Inte kategoriserad Needit
- Inte kategoriserad MiPow
- Inte kategoriserad GoldenEar Technology
- Inte kategoriserad Colt
- Inte kategoriserad Elite Screens
- Inte kategoriserad Sungrow
- Inte kategoriserad Quadro
- Inte kategoriserad Ultron
- Inte kategoriserad Choice
- Inte kategoriserad Roswell
- Inte kategoriserad King Craft
- Inte kategoriserad FOX ESS
- Inte kategoriserad Airman
- Inte kategoriserad Cascade Audio Engineering
- Inte kategoriserad B-Speech
- Inte kategoriserad Apa
- Inte kategoriserad Vanish
- Inte kategoriserad Nostalgia
- Inte kategoriserad Grosfillex
- Inte kategoriserad Solplanet
- Inte kategoriserad Beemoo
- Inte kategoriserad Hollyland
- Inte kategoriserad Platinet
- Inte kategoriserad Santos
- Inte kategoriserad Entes
- Inte kategoriserad Evoc
- Inte kategoriserad Versare
- Inte kategoriserad Enphase
- Inte kategoriserad Tractive
- Inte kategoriserad SpeakerCraft
- Inte kategoriserad Celexon
- Inte kategoriserad Epcom
- Inte kategoriserad EVOLVEO
- Inte kategoriserad Kanto
- Inte kategoriserad Prixton
- Inte kategoriserad ZeeVee
- Inte kategoriserad Primera
- Inte kategoriserad Siku
- Inte kategoriserad Viatek
- Inte kategoriserad ADDAC System
- Inte kategoriserad Simplicity
- Inte kategoriserad Doomoo
- Inte kategoriserad MBZ
- Inte kategoriserad Davey
- Inte kategoriserad Mettler
- Inte kategoriserad Metalux
- Inte kategoriserad Heitech
- Inte kategoriserad Potenza
- Inte kategoriserad LOQED
- Inte kategoriserad Hatco
- Inte kategoriserad Fulgor Milano
- Inte kategoriserad KONFTEL
- Inte kategoriserad Canicom
- Inte kategoriserad EGO
- Inte kategoriserad Mitsai
- Inte kategoriserad Selfsat
- Inte kategoriserad Leef
- Inte kategoriserad Tusa
- Inte kategoriserad Hovicon
- Inte kategoriserad TC Helicon
- Inte kategoriserad Starlyf
- Inte kategoriserad Kramer
- Inte kategoriserad RCBS
- Inte kategoriserad American BioTech Supply
- Inte kategoriserad Lagrange
- Inte kategoriserad Noris
- Inte kategoriserad JANDY
- Inte kategoriserad KS Tools
- Inte kategoriserad Koliber
- Inte kategoriserad Schmidt & Bender
- Inte kategoriserad Mesa Boogie
- Inte kategoriserad Improv
- Inte kategoriserad InLine
- Inte kategoriserad LandRoller
- Inte kategoriserad Wegman
- Inte kategoriserad Lockncharge
- Inte kategoriserad Merlin
- Inte kategoriserad Standard Horizon
- Inte kategoriserad V7
- Inte kategoriserad Goal Zero
- Inte kategoriserad Pabobo
- Inte kategoriserad HealthPostures
- Inte kategoriserad Dreadbox
- Inte kategoriserad Joranalogue
- Inte kategoriserad CYP
- Inte kategoriserad Heaven Fresh
- Inte kategoriserad Lutec
- Inte kategoriserad Champion Sports
- Inte kategoriserad Molotow
- Inte kategoriserad Rothenberger
- Inte kategoriserad Creamsource
- Inte kategoriserad Herlag
- Inte kategoriserad Dux
- Inte kategoriserad FALLER
- Inte kategoriserad Miditech
- Inte kategoriserad SE Electronics
- Inte kategoriserad TTM
- Inte kategoriserad Paw Patrol
- Inte kategoriserad ISi
- Inte kategoriserad LELO
- Inte kategoriserad AudioControl
- Inte kategoriserad Apricorn
- Inte kategoriserad Timbersled
- Inte kategoriserad Creality3D
- Inte kategoriserad Mermade
- Inte kategoriserad MXR
- Inte kategoriserad SKLZ
- Inte kategoriserad Herma
- Inte kategoriserad Cyrus
- Inte kategoriserad BWT
- Inte kategoriserad Syrp
- Inte kategoriserad Ugolini
- Inte kategoriserad Cosina
- Inte kategoriserad Heckler & Koch
- Inte kategoriserad Whistler
- Inte kategoriserad Twisper
- Inte kategoriserad Suevia
- Inte kategoriserad Manitowoc
- Inte kategoriserad Palmer
- Inte kategoriserad J5create
- Inte kategoriserad Lund
- Inte kategoriserad Hushmat
- Inte kategoriserad Xigmatek
- Inte kategoriserad Tema
- Inte kategoriserad Intellijel
- Inte kategoriserad ALM
- Inte kategoriserad Topaz
- Inte kategoriserad Toddy
- Inte kategoriserad Aicon
- Inte kategoriserad Astell&Kern
- Inte kategoriserad Doepfer
- Inte kategoriserad Fun Generation
- Inte kategoriserad Xvive
- Inte kategoriserad Karma
- Inte kategoriserad TV One
- Inte kategoriserad Berkel
- Inte kategoriserad Empress Effects
- Inte kategoriserad Dreame
- Inte kategoriserad Hugo Muller
- Inte kategoriserad Vinci
- Inte kategoriserad Jordan
- Inte kategoriserad Duromax
- Inte kategoriserad DataComm
- Inte kategoriserad Powercube
- Inte kategoriserad Kasp
- Inte kategoriserad Dimavery
- Inte kategoriserad Hanwha
- Inte kategoriserad WestBend
- Inte kategoriserad Mr Coffee
- Inte kategoriserad Sherlock
- Inte kategoriserad Sloan
- Inte kategoriserad SEA-PRO
- Inte kategoriserad Livarno Lux
- Inte kategoriserad Omiindustriies
- Inte kategoriserad Weltevree
- Inte kategoriserad Phoenix Contact
- Inte kategoriserad AMS Neve
- Inte kategoriserad LVSUN
- Inte kategoriserad Aston Microphones
- Inte kategoriserad Netsys
- Inte kategoriserad Alfi
- Inte kategoriserad Gtech
- Inte kategoriserad Polarlite
- Inte kategoriserad Companion
- Inte kategoriserad Mr. Beams
- Inte kategoriserad Morphor
- Inte kategoriserad Lapp
- Inte kategoriserad XO
- Inte kategoriserad PcDuino
- Inte kategoriserad LECO
- Inte kategoriserad Maretron
- Inte kategoriserad Hortus
- Inte kategoriserad Razorri
- Inte kategoriserad Fetch
- Inte kategoriserad Calligaris .com
- Inte kategoriserad Zoetis
- Inte kategoriserad Prem-i-air
- Inte kategoriserad NWS
- Inte kategoriserad GAM
- Inte kategoriserad Knog
- Inte kategoriserad Scale Computing
- Inte kategoriserad Broil King
- Inte kategoriserad Media-tech
- Inte kategoriserad Naturn Living
- Inte kategoriserad Aeotec
- Inte kategoriserad Catlink
- Inte kategoriserad FitterFirst
- Inte kategoriserad Raveland
- Inte kategoriserad Mr. Heater
- Inte kategoriserad Welltech
- Inte kategoriserad Trumeter
- Inte kategoriserad Seidio
- Inte kategoriserad Sincreative
- Inte kategoriserad JDC
- Inte kategoriserad HammerSmith
- Inte kategoriserad Hidrate
- Inte kategoriserad Sonicware
- Inte kategoriserad Nexibo
- Inte kategoriserad Jolin
- Inte kategoriserad MoTip
- Inte kategoriserad Stenda
- Inte kategoriserad Pro-Lift
- Inte kategoriserad HIOAZO
- Inte kategoriserad Malstrom
- Inte kategoriserad Laserluchs
- Inte kategoriserad Powersoft
- Inte kategoriserad Casetastic
- Inte kategoriserad UClear
- Inte kategoriserad BikeLogger
- Inte kategoriserad Tor Rey
- Inte kategoriserad Momo Design
- Inte kategoriserad Esdec
- Inte kategoriserad Ruark Audio
- Inte kategoriserad Neewer
- Inte kategoriserad AJH Synth
- Inte kategoriserad LifeStraw
- Inte kategoriserad Magnavox
- Inte kategoriserad Lincoln Electric
- Inte kategoriserad Toolit
- Inte kategoriserad Egnater
- Inte kategoriserad DutchOne
- Inte kategoriserad Feitian
- Inte kategoriserad Cranborne Audio
- Inte kategoriserad Ergie
- Inte kategoriserad Reltech
- Inte kategoriserad Guide
- Inte kategoriserad Armcross
- Inte kategoriserad Focus Electrics
- Inte kategoriserad Huntleigh
- Inte kategoriserad Beeletix
- Inte kategoriserad Gehmann
- Inte kategoriserad Batronix
- Inte kategoriserad Franzis
- Inte kategoriserad Gridbyt
- Inte kategoriserad TDK-Lambda
- Inte kategoriserad LONQ
- Inte kategoriserad Em-Trak
- Inte kategoriserad Wonky Monkey
- Inte kategoriserad Dresden Elektronik
- Inte kategoriserad Atmel
- Inte kategoriserad Flavour Blaster
- Inte kategoriserad Esoteric
- Inte kategoriserad SmartAVI
- Inte kategoriserad EPH Elektronik
- Inte kategoriserad InfiRay
- Inte kategoriserad Best Service
- Inte kategoriserad Microchip
- Inte kategoriserad Markbass
- Inte kategoriserad IMG Stage Line
- Inte kategoriserad IMAC
- Inte kategoriserad Metz Connect
- Inte kategoriserad MGL Avionics
- Inte kategoriserad Eikon
- Inte kategoriserad Casablanca
- Inte kategoriserad Nemco
- Inte kategoriserad Wireless Solution
- Inte kategoriserad Beverage-Air
- Inte kategoriserad Sparco
- Inte kategoriserad Barber Tech
- Inte kategoriserad Estella
- Inte kategoriserad EarFun
- Inte kategoriserad Oehlbach
- Inte kategoriserad Minkels
- Inte kategoriserad Kipor
- Inte kategoriserad Lenmar
- Inte kategoriserad HMS Premium
- Inte kategoriserad Arduino
- Inte kategoriserad Ave Six
- Inte kategoriserad Bestar
- Inte kategoriserad Pelco
- Inte kategoriserad Gardigo
- Inte kategoriserad Highpoint
- Inte kategoriserad Puls Dimension
- Inte kategoriserad Studiologic
- Inte kategoriserad Fischer Amps
- Inte kategoriserad CHINT
- Inte kategoriserad Sirus
- Inte kategoriserad Digitech
- Inte kategoriserad Leviton
- Inte kategoriserad Chauvin Arnoux
- Inte kategoriserad Gretsch
- Inte kategoriserad Pentacon
- Inte kategoriserad Winia
- Inte kategoriserad Atlas Sound
- Inte kategoriserad Bolsey
- Inte kategoriserad Louis Tellier
- Inte kategoriserad EtiamPro
- Inte kategoriserad Simeo
- Inte kategoriserad Baracuda
- Inte kategoriserad Kstar
- Inte kategoriserad BeSafe
- Inte kategoriserad Air Guard
- Inte kategoriserad Neutrik
- Inte kategoriserad MediaMatrix
- Inte kategoriserad ESX
- Inte kategoriserad Anywhere Cart
- Inte kategoriserad Tuur
- Inte kategoriserad ONE Smart Control
- Inte kategoriserad Megger
- Inte kategoriserad Edelkrone
- Inte kategoriserad OBSBOT
- Inte kategoriserad InSinkErator
- Inte kategoriserad AREXX
- Inte kategoriserad Artusi
- Inte kategoriserad Gossen Metrawatt
- Inte kategoriserad Omnires
- Inte kategoriserad IVT
- Inte kategoriserad Elite Force
- Inte kategoriserad JK Audio
- Inte kategoriserad DEHN
- Inte kategoriserad Piko
- Inte kategoriserad Lifan
- Inte kategoriserad Jomox
- Inte kategoriserad Pentatech
- Inte kategoriserad Burley
- Inte kategoriserad Lexicon
- Inte kategoriserad Graphite
- Inte kategoriserad Icarus Blue
- Inte kategoriserad Command
- Inte kategoriserad IRIS
- Inte kategoriserad Neno
- Inte kategoriserad Rigol
- Inte kategoriserad Starburst
- Inte kategoriserad Futurelight
- Inte kategoriserad AVPro Edge
- Inte kategoriserad Fluance
- Inte kategoriserad PCE Instruments
- Inte kategoriserad Garden Place
- Inte kategoriserad Rinnai
- Inte kategoriserad Moldex
- Inte kategoriserad Cudy
- Inte kategoriserad MaximaVida
- Inte kategoriserad Firefriend
- Inte kategoriserad DOD
- Inte kategoriserad LightZone
- Inte kategoriserad KRK
- Inte kategoriserad Robinhood
- Inte kategoriserad Bliss Outdoors
- Inte kategoriserad Fontiso
- Inte kategoriserad Varytec
- Inte kategoriserad Altra
- Inte kategoriserad Omnilux
- Inte kategoriserad Socket Mobile
- Inte kategoriserad Brilliant
- Inte kategoriserad Enermax
- Inte kategoriserad Quartet
- Inte kategoriserad Heitronic
- Inte kategoriserad Shadow
- Inte kategoriserad IP-COM
- Inte kategoriserad Comtek
- Inte kategoriserad Fishman
- Inte kategoriserad Tams Elektronik
- Inte kategoriserad Digital Juice
- Inte kategoriserad Eschenbach
- Inte kategoriserad Neumärker
- Inte kategoriserad ASM
- Inte kategoriserad Bretford
- Inte kategoriserad Elektron
- Inte kategoriserad Ltech
- Inte kategoriserad Kiev
- Inte kategoriserad RetroSound
- Inte kategoriserad PowerBass
- Inte kategoriserad Caroline
- Inte kategoriserad Zomo
- Inte kategoriserad VAIS Technology
- Inte kategoriserad NEO Tools
- Inte kategoriserad Synco
- Inte kategoriserad Buchla & TipTop Audio
- Inte kategoriserad Kiloview
- Inte kategoriserad Pyramid
- Inte kategoriserad Maico
- Inte kategoriserad Lindy
- Inte kategoriserad SHX
- Inte kategoriserad On-Q
- Inte kategoriserad Govee
- Inte kategoriserad Sirius
- Inte kategoriserad SetonixSynth
- Inte kategoriserad Horex
- Inte kategoriserad Inno-Hit
- Inte kategoriserad Sime
- Inte kategoriserad AvaValley
- Inte kategoriserad INTIMINA
- Inte kategoriserad Monzana
- Inte kategoriserad FCC BBQ
- Inte kategoriserad Auto XS
- Inte kategoriserad Toomax
- Inte kategoriserad Aqua Marina
- Inte kategoriserad Hameg
- Inte kategoriserad Greemotion
- Inte kategoriserad Winter Modular
- Inte kategoriserad Salewa
- Inte kategoriserad FED
- Inte kategoriserad Platinum Tools
- Inte kategoriserad Synamodec
- Inte kategoriserad Nuance
- Inte kategoriserad Grotime
- Inte kategoriserad Pico Macom
- Inte kategoriserad RadonTec
- Inte kategoriserad Katrin
- Inte kategoriserad TDE Instruments
- Inte kategoriserad Kendau
- Inte kategoriserad Kisag
- Inte kategoriserad NUX
- Inte kategoriserad Coxreels
- Inte kategoriserad Nous
- Inte kategoriserad Morley
- Inte kategoriserad Overade
- Inte kategoriserad Liemke
- Inte kategoriserad Copco
- Inte kategoriserad Vanson
- Inte kategoriserad Canyon
- Inte kategoriserad Carcomm
- Inte kategoriserad Style Me Up
- Inte kategoriserad Swedish Posture
- Inte kategoriserad GoldAir
- Inte kategoriserad JIMMY
- Inte kategoriserad Melnor
- Inte kategoriserad CDVI
- Inte kategoriserad Excalibur
- Inte kategoriserad Sôlt
- Inte kategoriserad Holman
- Inte kategoriserad HomePilot
- Inte kategoriserad Leaptel
- Inte kategoriserad Lifenaxx
- Inte kategoriserad Powertec
- Inte kategoriserad Waterbird
- Inte kategoriserad Joy-it
- Inte kategoriserad Dreambaby
- Inte kategoriserad AOpen
- Inte kategoriserad Angler
- Inte kategoriserad GP
- Inte kategoriserad Akrobat
- Inte kategoriserad Casaria
- Inte kategoriserad Techno Line
- Inte kategoriserad Selleys
- Inte kategoriserad WindFall
- Inte kategoriserad Ameristep
- Inte kategoriserad Rikon
- Inte kategoriserad KM-fit
- Inte kategoriserad X Rocker
- Inte kategoriserad Mircom
- Inte kategoriserad ESUN
- Inte kategoriserad TSC
- Inte kategoriserad Durex
- Inte kategoriserad Ravanson
- Inte kategoriserad Wachendorff
- Inte kategoriserad Sensei
- Inte kategoriserad AeroCool
- Inte kategoriserad Klein Tools
- Inte kategoriserad Vantage Point
- Inte kategoriserad Jokari
- Inte kategoriserad BeeSecure
- Inte kategoriserad MantelMount
- Inte kategoriserad Unicol
- Inte kategoriserad Fisher Paykel
- Inte kategoriserad Lasita Maja
- Inte kategoriserad Meccano
- Inte kategoriserad Parallels
- Inte kategoriserad Oatey
- Inte kategoriserad QUIO
- Inte kategoriserad Fisher
- Inte kategoriserad Gretsch Guitars
- Inte kategoriserad Banoch
- Inte kategoriserad XP-PEN
- Inte kategoriserad Atmotube
- Inte kategoriserad Sun Pumps
- Inte kategoriserad Electrify
- Inte kategoriserad Leatt
- Inte kategoriserad Bleep Labs
- Inte kategoriserad FontaFit
- Inte kategoriserad Gossmann
- Inte kategoriserad Comatec
- Inte kategoriserad Jonard Tools
- Inte kategoriserad WEG
- Inte kategoriserad Atech Flash Technology
- Inte kategoriserad AutoParkTime
- Inte kategoriserad Hudora
- Inte kategoriserad Ernitec
- Inte kategoriserad Facal
- Inte kategoriserad Planet Audio
- Inte kategoriserad Datacolor
- Inte kategoriserad Silicon Power
- Inte kategoriserad Sabrent
- Inte kategoriserad Aim TTi
- Inte kategoriserad JAXY
- Inte kategoriserad WARN
- Inte kategoriserad Aarke
- Inte kategoriserad TikkTokk
- Inte kategoriserad Roadinger
- Inte kategoriserad Roco
- Inte kategoriserad Flexson
- Inte kategoriserad Camec
- Inte kategoriserad Wibrain
- Inte kategoriserad Rolly Toys
- Inte kategoriserad Deditec
- Inte kategoriserad Level Mount
- Inte kategoriserad Teenage Engineering
- Inte kategoriserad Elipson
- Inte kategoriserad STANDIVARIUS
- Inte kategoriserad CommScope
- Inte kategoriserad Videotec
- Inte kategoriserad Orange
- Inte kategoriserad Extralife Instruments
- Inte kategoriserad Genki Instruments
- Inte kategoriserad Industrial Music Electronics
- Inte kategoriserad Mauser Sitzkultur
- Inte kategoriserad Accezz
- Inte kategoriserad Create
- Inte kategoriserad A4 Tech
- Inte kategoriserad Full Boar
- Inte kategoriserad Zedar
- Inte kategoriserad Yli Electronic
- Inte kategoriserad Dals
- Inte kategoriserad Bulman
- Inte kategoriserad TOOLMATE
- Inte kategoriserad SleepPro
- Inte kategoriserad Muama
- Inte kategoriserad Lepu Medical
- Inte kategoriserad Michigan
- Inte kategoriserad Wiha
- Inte kategoriserad Beringer
- Inte kategoriserad Waterdrop
- Inte kategoriserad Revamp
- Inte kategoriserad Phonic
- Inte kategoriserad ZCover
- Inte kategoriserad Vasagle
- Inte kategoriserad Lewitt
- Inte kategoriserad Aquatica
- Inte kategoriserad Girmi
- Inte kategoriserad Goaliath
- Inte kategoriserad 909 Outdoor
- Inte kategoriserad Viomi
- Inte kategoriserad Grimm Audio
- Inte kategoriserad Kahayan
- Inte kategoriserad Better Life
- Inte kategoriserad Dayclocks
- Inte kategoriserad Phidgets
- Inte kategoriserad TK Audio
- Inte kategoriserad Postium
- Inte kategoriserad Hawk-Woods
- Inte kategoriserad Novo
- Inte kategoriserad XS Power
- Inte kategoriserad Anthro
- Inte kategoriserad Commercial Chef
- Inte kategoriserad Novis
- Inte kategoriserad Dexibell
- Inte kategoriserad IsoAcoustics
- Inte kategoriserad Memphis
- Inte kategoriserad Alpha Tools
- Inte kategoriserad Engel
- Inte kategoriserad Clifford
- Inte kategoriserad Atlona
- Inte kategoriserad AVMATRIX
- Inte kategoriserad Cambo
- Inte kategoriserad Hedbox
- Inte kategoriserad Campart
- Inte kategoriserad Lansinoh
- Inte kategoriserad Adviti
- Inte kategoriserad Maclean
- Inte kategoriserad 9.solutions
- Inte kategoriserad Grundfos
- Inte kategoriserad Hotone
- Inte kategoriserad WEN
- Inte kategoriserad Trace Elliot
- Inte kategoriserad Lockwood
- Inte kategoriserad Kospel
- Inte kategoriserad Nexera
- Inte kategoriserad Goodway
- Inte kategoriserad BlueDri
- Inte kategoriserad Seenergy
- Inte kategoriserad Meinl
- Inte kategoriserad Analogis
- Inte kategoriserad BBQ Premium
- Inte kategoriserad Stäubli
- Inte kategoriserad RAB
- Inte kategoriserad Schabus
- Inte kategoriserad Eoslift
- Inte kategoriserad Bron-Coucke
- Inte kategoriserad Steelton
- Inte kategoriserad FeinTech
- Inte kategoriserad BioChef
- Inte kategoriserad Masterbuilt
- Inte kategoriserad T-Rex
- Inte kategoriserad Waterco
- Inte kategoriserad Koolatron
- Inte kategoriserad Kindercraft
- Inte kategoriserad Euro Cuisine
- Inte kategoriserad GFM
- Inte kategoriserad Tot Tutors
- Inte kategoriserad X4 Life
- Inte kategoriserad Ugreen
- Inte kategoriserad Tonar
- Inte kategoriserad Peterson
- Inte kategoriserad CFH
- Inte kategoriserad BOB Gear
- Inte kategoriserad Emeril Everyday
- Inte kategoriserad Könner & Söhnen
- Inte kategoriserad Rockboard
- Inte kategoriserad Goodis
- Inte kategoriserad Nivian
- Inte kategoriserad L.R.Baggs
- Inte kategoriserad Millennia
- Inte kategoriserad Vermona Modular
- Inte kategoriserad Adventure Kings
- Inte kategoriserad Drive Medical
- Inte kategoriserad Hitron
- Inte kategoriserad Bliss Hammocks
- Inte kategoriserad Singular Sound
- Inte kategoriserad Maneco Labs
- Inte kategoriserad BISWIND
- Inte kategoriserad ABE Arnhold
- Inte kategoriserad Mermade Hair
- Inte kategoriserad Hover-1
- Inte kategoriserad VCM
- Inte kategoriserad BodyCraft
- Inte kategoriserad Auer Signal
- Inte kategoriserad BrightSign
- Inte kategoriserad Mamas & Papas
- Inte kategoriserad Manduca
- Inte kategoriserad HELGI
- Inte kategoriserad Forge Adour
- Inte kategoriserad Eliminator Lighting
- Inte kategoriserad Darkglass
- Inte kategoriserad Blow
- Inte kategoriserad Paasche
- Inte kategoriserad Vistus
- Inte kategoriserad GMW
- Inte kategoriserad AER
- Inte kategoriserad Dynavox
- Inte kategoriserad Columbus
- Inte kategoriserad IWH
- Inte kategoriserad UGo
- Inte kategoriserad Code Mercenaries
- Inte kategoriserad SoundMagic
- Inte kategoriserad Diamex
- Inte kategoriserad Sunset
- Inte kategoriserad IPEGA
- Inte kategoriserad Avital
- Inte kategoriserad Ondis24
- Inte kategoriserad D'Addario
- Inte kategoriserad BBE
- Inte kategoriserad Lemair
- Inte kategoriserad Warwick
- Inte kategoriserad MyAVR
- Inte kategoriserad EBS
- Inte kategoriserad WEICON
- Inte kategoriserad Rotronic
- Inte kategoriserad Edsyn
- Inte kategoriserad Urban Glide
- Inte kategoriserad EISL
- Inte kategoriserad RCS
- Inte kategoriserad ARC
- Inte kategoriserad Nicai Systems
- Inte kategoriserad IDENTsmart
- Inte kategoriserad Sharper Image
- Inte kategoriserad Altrad
- Inte kategoriserad Revier Manager
- Inte kategoriserad Homak
- Inte kategoriserad Statron
- Inte kategoriserad Tycon Systems
- Inte kategoriserad Selve
- Inte kategoriserad Lumel
- Inte kategoriserad Paingone
- Inte kategoriserad Howard Leight
- Inte kategoriserad Plugwise
- Inte kategoriserad Martens
- Inte kategoriserad Palmako
- Inte kategoriserad Desview
- Inte kategoriserad ActiveJet
- Inte kategoriserad Global Water
- Inte kategoriserad Allsee
- Inte kategoriserad Softing
- Inte kategoriserad Pulse ShowerSpas
- Inte kategoriserad Alogic
- Inte kategoriserad GFB
- Inte kategoriserad Sonicsmith
- Inte kategoriserad Toraiz
- Inte kategoriserad Ergodyne
- Inte kategoriserad Maturmeat
- Inte kategoriserad D-Jix
- Inte kategoriserad Orbsmart
- Inte kategoriserad Eowave
- Inte kategoriserad Arkon
- Inte kategoriserad Imperia
- Inte kategoriserad Nature2
- Inte kategoriserad Baby Trend
- Inte kategoriserad AMERRY
- Inte kategoriserad Walther
- Inte kategoriserad ShelterLogic
- Inte kategoriserad Varad
- Inte kategoriserad Dr. Browns
- Inte kategoriserad Woods
- Inte kategoriserad UDG Gear
- Inte kategoriserad KMA Machines
- Inte kategoriserad CEDAR
- Inte kategoriserad Klark Teknik
- Inte kategoriserad Elcom
- Inte kategoriserad Source Audio
- Inte kategoriserad AtomoSynth
- Inte kategoriserad Innr
- Inte kategoriserad Benidub
- Inte kategoriserad Protector
- Inte kategoriserad Winston
- Inte kategoriserad Solidsteel
- Inte kategoriserad Lectrosonics
- Inte kategoriserad Dracast
- Inte kategoriserad Dream
- Inte kategoriserad Malouf
- Inte kategoriserad Roba
- Inte kategoriserad Ravelli
- Inte kategoriserad Piet Boon
- Inte kategoriserad PureTools
- Inte kategoriserad JML
- Inte kategoriserad Reber
- Inte kategoriserad SiriusXM
- Inte kategoriserad Earthwise
- Inte kategoriserad DoubleSight
- Inte kategoriserad Raya
- Inte kategoriserad NANO Modules
- Inte kategoriserad Artex
- Inte kategoriserad Bobrick
- Inte kategoriserad Verbos Electronics
- Inte kategoriserad Ark
- Inte kategoriserad DLO
- Inte kategoriserad ENS
- Inte kategoriserad Listen
- Inte kategoriserad Pentair
- Inte kategoriserad Oscium
- Inte kategoriserad Benchmark USA
- Inte kategoriserad Python
- Inte kategoriserad Littelfuse
- Inte kategoriserad Game Factor
- Inte kategoriserad NComputing
- Inte kategoriserad Brändi
- Inte kategoriserad Mode Machines
- Inte kategoriserad Legends
- Inte kategoriserad AS Synthesizers
- Inte kategoriserad Itechworld
- Inte kategoriserad Nexcom
- Inte kategoriserad Janitza
- Inte kategoriserad SatKing
- Inte kategoriserad Fulltone
- Inte kategoriserad Advantix
- Inte kategoriserad Wampler
- Inte kategoriserad Hosa
- Inte kategoriserad VAEMI
- Inte kategoriserad Aguilar
- Inte kategoriserad Narva
- Inte kategoriserad DOK
- Inte kategoriserad OzCharge
- Inte kategoriserad MIYO
- Inte kategoriserad Cioks
- Inte kategoriserad Neopower
- Inte kategoriserad AvMap
- Inte kategoriserad Arlec
- Inte kategoriserad Sanwa
- Inte kategoriserad REDARC
- Inte kategoriserad Guardian
- Inte kategoriserad Radio Flyer
- Inte kategoriserad Gaslock
- Inte kategoriserad Gaffgun
- Inte kategoriserad AquaMAX
- Inte kategoriserad DigitSole
- Inte kategoriserad Portsmith
- Inte kategoriserad Flame
- Inte kategoriserad Rome
- Inte kategoriserad DW
- Inte kategoriserad BEA
- Inte kategoriserad Disty
- Inte kategoriserad OXI Instruments
- Inte kategoriserad AvaTime
- Inte kategoriserad Xhose
- Inte kategoriserad MYVU
- Inte kategoriserad Kopykake
- Inte kategoriserad Konstant Lab
- Inte kategoriserad Turbo Scrub
- Inte kategoriserad Tenderfoot Electronics
- Inte kategoriserad Kask
- Inte kategoriserad Callpod
- Inte kategoriserad Dorman
- Inte kategoriserad 2box
- Inte kategoriserad Enlight
- Inte kategoriserad Franken
- Inte kategoriserad RUBI
- Inte kategoriserad Europa Leisure
- Inte kategoriserad GAMO
- Inte kategoriserad Musser
- Inte kategoriserad Edge Products
- Inte kategoriserad IClever
- Inte kategoriserad HN-Power
- Inte kategoriserad BIONIK
- Inte kategoriserad King Canopy
- Inte kategoriserad HeadRush
- Inte kategoriserad Flover
- Inte kategoriserad Milestone Systems
- Inte kategoriserad Micsig
- Inte kategoriserad Dodow
- Inte kategoriserad Spring
- Inte kategoriserad Red Panda
- Inte kategoriserad OJ ELECTRONICS
- Inte kategoriserad Aquasure
- Inte kategoriserad Banana Pi
- Inte kategoriserad Ilford
- Inte kategoriserad TensCare
- Inte kategoriserad American International
- Inte kategoriserad Crazy Tube Circuits
- Inte kategoriserad J.P. Instruments
- Inte kategoriserad GMB Gaming
- Inte kategoriserad Proclip
- Inte kategoriserad SainSmart
- Inte kategoriserad Kaona
- Inte kategoriserad Baja Mobility
- Inte kategoriserad DPW Design
- Inte kategoriserad SinuPulse
- Inte kategoriserad The T.bone
- Inte kategoriserad DIEZEL
- Inte kategoriserad VMB
- Inte kategoriserad Z.Vex
- Inte kategoriserad Seymour Duncan
- Inte kategoriserad BluGuitar
- Inte kategoriserad Lehle
- Inte kategoriserad Bricasti Design
- Inte kategoriserad T.akustik
- Inte kategoriserad Dwarf Connection
- Inte kategoriserad JL Cooper
- Inte kategoriserad StrikeMaster
- Inte kategoriserad ProUser
- Inte kategoriserad Bēm Wireless
- Inte kategoriserad Aqua-Vu
- Inte kategoriserad Millecroquettes
- Inte kategoriserad GR Bass
- Inte kategoriserad WilTec
- Inte kategoriserad Sure-Fi
- Inte kategoriserad Copernicus
- Inte kategoriserad Gumdrop
- Inte kategoriserad Tellur
- Inte kategoriserad Woox
- Inte kategoriserad Gallien-Krueger
- Inte kategoriserad Jetway
- Inte kategoriserad Texsport
- Inte kategoriserad SSV Works
- Inte kategoriserad Terre
- Inte kategoriserad Sanitec
- Inte kategoriserad Pangea Audio
- Inte kategoriserad Hogue
- Inte kategoriserad ATP
- Inte kategoriserad Pfannenberg
- Inte kategoriserad Scytek
- Inte kategoriserad MotorScrubber
- Inte kategoriserad Krone
- Inte kategoriserad Lupine
- Inte kategoriserad Kraftmax
- Inte kategoriserad Steelplay
- Inte kategoriserad PCTV Systems
- Inte kategoriserad Cooper Lighting
- Inte kategoriserad Sound Devices
- Inte kategoriserad Code Corporation
- Inte kategoriserad Now TV
- Inte kategoriserad Beautiful
- Inte kategoriserad Best Fitness
- Inte kategoriserad Voodoo Lab
- Inte kategoriserad Strymon
- Inte kategoriserad Insect Lore
- Inte kategoriserad FSR
- Inte kategoriserad Faytech
- Inte kategoriserad Chrome-Q
- Inte kategoriserad Kitronik
- Inte kategoriserad Trasman
- Inte kategoriserad Hamlet
- Inte kategoriserad Garden Feelings
- Inte kategoriserad SumUp
- Inte kategoriserad Microlab
- Inte kategoriserad Rotolight
- Inte kategoriserad Mr Gardener
- Inte kategoriserad Paladin
- Inte kategoriserad Lumu
- Inte kategoriserad Salicru
- Inte kategoriserad WAYDOO
- Inte kategoriserad Fimer
- Inte kategoriserad ASIWO
- Inte kategoriserad Vankyo
- Inte kategoriserad OWC
- Inte kategoriserad Lexar
- Inte kategoriserad Equip
- Inte kategoriserad Vivolink
- Inte kategoriserad Vent-Axia
- Inte kategoriserad Firefield
- Inte kategoriserad E-Power
- Inte kategoriserad RectorSeal
- Inte kategoriserad Red Digital Cinema
- Inte kategoriserad Beautifly
- Inte kategoriserad Marathon
- Inte kategoriserad Kaiser Nienhaus
- Inte kategoriserad Freeplay
- Inte kategoriserad Roller Grill
- Inte kategoriserad DCS
- Inte kategoriserad Zaor
- Inte kategoriserad Glorious
- Inte kategoriserad Cleco
- Inte kategoriserad AVTech
- Inte kategoriserad Cubot
- Inte kategoriserad Dataflex
- Inte kategoriserad Bugera
- Inte kategoriserad Handy Lux
- Inte kategoriserad Rossum Electro-Music
- Inte kategoriserad Panta
- Inte kategoriserad Pentel
- Inte kategoriserad Wallas
- Inte kategoriserad Gima
- Inte kategoriserad MagnaPool
- Inte kategoriserad Aquadon
- Inte kategoriserad Raidsonic
- Inte kategoriserad Approx
- Inte kategoriserad Gamesir
- Inte kategoriserad Neunaber
- Inte kategoriserad ENDORFY
- Inte kategoriserad Leotec
- Inte kategoriserad DPM
- Inte kategoriserad VOREL
- Inte kategoriserad Ciarra
- Inte kategoriserad Ocean Way Audio
- Inte kategoriserad DayStar Filters
- Inte kategoriserad Flexispot
- Inte kategoriserad OP/TECH
- Inte kategoriserad Alfatron
- Inte kategoriserad ETC
- Inte kategoriserad Vertex
- Inte kategoriserad Nuki
- Inte kategoriserad SWIT
- Inte kategoriserad EOTech
- Inte kategoriserad Cinderella
- Inte kategoriserad Bauhn
- Inte kategoriserad Aspen
- Inte kategoriserad Cottons
- Inte kategoriserad Key Digital
- Inte kategoriserad TVLogic
- Inte kategoriserad CAD Audio
- Inte kategoriserad Frequency Central
- Inte kategoriserad Sacrament
- Inte kategoriserad The Box
- Inte kategoriserad AudioThing
- Inte kategoriserad Feelworld
- Inte kategoriserad SoundPEATS
- Inte kategoriserad Cambium Networks
- Inte kategoriserad Trident
- Inte kategoriserad Schoeps
- Inte kategoriserad HPI Racing
- Inte kategoriserad COLBOR
- Inte kategoriserad Trijicon
- Inte kategoriserad Favini
- Inte kategoriserad Dnipro
- Inte kategoriserad Dot Line
- Inte kategoriserad Polsen
- Inte kategoriserad KJB Security Products
- Inte kategoriserad IFootage
- Inte kategoriserad Sonuus
- Inte kategoriserad Whirlwind
- Inte kategoriserad Cabasse
- Inte kategoriserad Jonsered
- Inte kategoriserad Saint Algue
- Inte kategoriserad Cactus
- Inte kategoriserad Musical Fidelity
- Inte kategoriserad Oecolux
- Inte kategoriserad Core SWX
- Inte kategoriserad Multibrackets
- Inte kategoriserad SoundLAB
- Inte kategoriserad ACL
- Inte kategoriserad SurgeX
- Inte kategoriserad Mars Gaming
- Inte kategoriserad Radiant
- Inte kategoriserad G.Skill
- Inte kategoriserad Edbak
- Inte kategoriserad Integral LED
- Inte kategoriserad Integral
- Inte kategoriserad Roline
- Inte kategoriserad Virax
- Inte kategoriserad MSW
- Inte kategoriserad Amaran
- Inte kategoriserad Gill
- Inte kategoriserad AMC
- Inte kategoriserad Triangle
- Inte kategoriserad Rittal
- Inte kategoriserad I-Tec
- Inte kategoriserad Majestic
- Inte kategoriserad Oras
- Inte kategoriserad Tumbleweed
- Inte kategoriserad Alutruss
- Inte kategoriserad Sunpentown
- Inte kategoriserad Hamstra
- Inte kategoriserad PVI
- Inte kategoriserad OKAY
- Inte kategoriserad Avenview
- Inte kategoriserad Grendel
- Inte kategoriserad Coravin
- Inte kategoriserad Phoenix Gold
- Inte kategoriserad Weidmüller
- Inte kategoriserad BSS Audio
- Inte kategoriserad O&O Software
- Inte kategoriserad Wasp
- Inte kategoriserad Chef's Choice
- Inte kategoriserad Ciclo
- Inte kategoriserad Warmup
- Inte kategoriserad Brastemp
- Inte kategoriserad Wavtech
- Inte kategoriserad Satco
- Inte kategoriserad AMT
- Inte kategoriserad Royal Catering
- Inte kategoriserad Artrom
- Inte kategoriserad Lowell
- Inte kategoriserad Adonit
- Inte kategoriserad Point Source Audio
- Inte kategoriserad ANDYCINE
- Inte kategoriserad Beghelli
- Inte kategoriserad AmpliVox
- Inte kategoriserad SEIKI
- Inte kategoriserad Pippi
- Inte kategoriserad Memphis Audio
- Inte kategoriserad Casalux
- Inte kategoriserad CyberData Systems
- Inte kategoriserad Omnitron Systems
- Inte kategoriserad Stewart Systems
- Inte kategoriserad SwitchBot
- Inte kategoriserad AMX
- Inte kategoriserad Qubino
- Inte kategoriserad Eurosound
- Inte kategoriserad BZBGear
- Inte kategoriserad Rolls
- Inte kategoriserad WyreStorm
- Inte kategoriserad K&M
- Inte kategoriserad Williams Sound
- Inte kategoriserad Magewell
- Inte kategoriserad Rocstor
- Inte kategoriserad Globalo
- Inte kategoriserad Adam Hall
- Inte kategoriserad SoundTube
- Inte kategoriserad Flaem
- Inte kategoriserad Therabody
- Inte kategoriserad Infortrend
- Inte kategoriserad STI
- Inte kategoriserad Rug Doctor
- Inte kategoriserad Mad Dog
- Inte kategoriserad Raspberry Pi
- Inte kategoriserad Bals
- Inte kategoriserad Balt
- Inte kategoriserad FIAP
- Inte kategoriserad Perixx
- Inte kategoriserad AJ.BA
- Inte kategoriserad ESKA
- Inte kategoriserad Lascar Electronics
- Inte kategoriserad EWON
- Inte kategoriserad Sport-Tronic
- Inte kategoriserad Alga
- Inte kategoriserad WesAudio
- Inte kategoriserad Hamron
- Inte kategoriserad Robust
- Inte kategoriserad Heritage Audio
- Inte kategoriserad Quik Lok
- Inte kategoriserad Tsakalis AudioWorks
- Inte kategoriserad MagTek
- Inte kategoriserad QOMO
- Inte kategoriserad SmallRig
- Inte kategoriserad MAK
- Inte kategoriserad Drake
- Inte kategoriserad Jupiter
- Inte kategoriserad Sony Optiarc
- Inte kategoriserad Colortone
- Inte kategoriserad Lowel
- Inte kategoriserad Anybus
- Inte kategoriserad Super Rod
- Inte kategoriserad Carnielli
- Inte kategoriserad Luminex
- Inte kategoriserad Epiphan
- Inte kategoriserad HiLook
- Inte kategoriserad Babybjörn
- Inte kategoriserad Deltaco Gaming
- Inte kategoriserad P3 International
- Inte kategoriserad Idec
- Inte kategoriserad Beckmann & Egle
- Inte kategoriserad Seek Thermal
- Inte kategoriserad VintageView
- Inte kategoriserad Alfresco
- Inte kategoriserad Bintec-elmeg
- Inte kategoriserad Crane Song
- Inte kategoriserad W'eau
- Inte kategoriserad Ixxat
- Inte kategoriserad Belena
- Inte kategoriserad Fanox
- Inte kategoriserad Crouzet
- Inte kategoriserad Megarevo
- Inte kategoriserad Tech 21
- Inte kategoriserad Petmate
- Inte kategoriserad BlendMount
- Inte kategoriserad Perlick
- Inte kategoriserad Sedona
- Inte kategoriserad Tecnoinox
- Inte kategoriserad CaterRacks
- Inte kategoriserad Besco
- Inte kategoriserad Prologue
- Inte kategoriserad Scotsman
- Inte kategoriserad Atosa
- Inte kategoriserad Nanoleaf
- Inte kategoriserad Mach Power
- Inte kategoriserad Soltection
- Inte kategoriserad Kool-It
- Inte kategoriserad Cool Head
- Inte kategoriserad KeepOut
- Inte kategoriserad LawnMaster
- Inte kategoriserad Deltronic
- Inte kategoriserad Eligent
- Inte kategoriserad Meris
- Inte kategoriserad Procare
- Inte kategoriserad AmerBox
- Inte kategoriserad Elbe
- Inte kategoriserad Qu-Bit
- Inte kategoriserad Blue Lantern
- Inte kategoriserad CTA Digital
- Inte kategoriserad DivKid
- Inte kategoriserad Uniross
- Inte kategoriserad Panamax
- Inte kategoriserad MBM
- Inte kategoriserad FaseLunare
- Inte kategoriserad Götze & Jensen
- Inte kategoriserad (Recovery)
- Inte kategoriserad Twinkly
- Inte kategoriserad Acefast
- Inte kategoriserad Squarp Instruments
- Inte kategoriserad EtherWAN
- Inte kategoriserad Econ Connect
- Inte kategoriserad META
- Inte kategoriserad Shimbol
- Inte kategoriserad GC Audio
- Inte kategoriserad Einhell Bavaria
- Inte kategoriserad Motrona
- Inte kategoriserad Thalheimer
- Inte kategoriserad Ergotools Pattfield
- Inte kategoriserad Proviel
- Inte kategoriserad FeiYu-Tech
- Inte kategoriserad Aida
- Inte kategoriserad Apantac
- Inte kategoriserad VisionTek
- Inte kategoriserad MuxLab
- Inte kategoriserad Accsoon
- Inte kategoriserad FeiyuTech
- Inte kategoriserad Losi
- Inte kategoriserad Bessey
- Inte kategoriserad A3
- Inte kategoriserad Ledvance
- Inte kategoriserad Serge
- Inte kategoriserad Gladiator
- Inte kategoriserad Nyko
- Inte kategoriserad Mobli
- Inte kategoriserad Sonoff
- Inte kategoriserad G-Technology
- Inte kategoriserad Caroma
- Inte kategoriserad Sungale
- Inte kategoriserad Befaco
- Inte kategoriserad Waltec
- Inte kategoriserad Eartec
- Inte kategoriserad Elvid
- Inte kategoriserad Portkeys
- Inte kategoriserad Westcott
- Inte kategoriserad Sky-Watcher
- Inte kategoriserad Tempo
- Inte kategoriserad EXSYS
- Inte kategoriserad Digiquest
- Inte kategoriserad Gewiss
- Inte kategoriserad Hagor
- Inte kategoriserad Glyph
- Inte kategoriserad Seco-Larm
- Inte kategoriserad Camille Bauer
- Inte kategoriserad Murr Elektronik
- Inte kategoriserad Massoth
- Inte kategoriserad Envitec
- Inte kategoriserad Mimo Monitors
- Inte kategoriserad Alula
- Inte kategoriserad Blebox
- Inte kategoriserad VS Sassoon
- Inte kategoriserad Redsbaby
- Inte kategoriserad Bright Spark
- Inte kategoriserad Algo
- Inte kategoriserad Peloton
- Inte kategoriserad Gentrax
- Inte kategoriserad Gamber-Johnson
- Inte kategoriserad Brocade
- Inte kategoriserad ICC
- Inte kategoriserad Insteon
- Inte kategoriserad Amer
- Inte kategoriserad Altronix
- Inte kategoriserad Juniper
- Inte kategoriserad Longvie
- Inte kategoriserad Warner Bros
- Inte kategoriserad Vinotemp
- Inte kategoriserad Silent Knight
- Inte kategoriserad Tiny Love
- Inte kategoriserad Mosconi
- Inte kategoriserad Ditek
- Inte kategoriserad Kingston Technology
- Inte kategoriserad Axxess
- Inte kategoriserad Wilson
- Inte kategoriserad Goki
- Inte kategoriserad CGV
- Inte kategoriserad My Arcade
- Inte kategoriserad Enttec
- Inte kategoriserad Tescoma
- Inte kategoriserad RF Elements
- Inte kategoriserad ALC
- Inte kategoriserad Holland Electronics
- Inte kategoriserad Arista
- Inte kategoriserad Chenbro Micom
- Inte kategoriserad Brentwood
- Inte kategoriserad Triumph Sports
- Inte kategoriserad Gasmate
- Inte kategoriserad Crelando
- Inte kategoriserad Novo Nordisk
- Inte kategoriserad Ionmax
- Inte kategoriserad Seville Classics
- Inte kategoriserad DeepCool
- Inte kategoriserad TechLogix Networx
- Inte kategoriserad SunBriteTV
- Inte kategoriserad NuTone
- Inte kategoriserad Thermalright
- Inte kategoriserad Meross
- Inte kategoriserad EchoMaster
- Inte kategoriserad Bxterra
- Inte kategoriserad Bea-fon
- Inte kategoriserad Renogy
- Inte kategoriserad Babylonia
- Inte kategoriserad HeartSine
- Inte kategoriserad Bullet
- Inte kategoriserad Morrison
- Inte kategoriserad Ordo
- Inte kategoriserad Noctua
- Inte kategoriserad Alphacool
- Inte kategoriserad Asetek
- Inte kategoriserad Biostar
- Inte kategoriserad AZZA
- Inte kategoriserad Audibax
- Inte kategoriserad TechN
- Inte kategoriserad Eversolo
- Inte kategoriserad Davita
- Inte kategoriserad Giga Copper
- Inte kategoriserad Elsner
- Inte kategoriserad Séura
- Inte kategoriserad Cube Controls
- Inte kategoriserad Meridian
- Inte kategoriserad IMG Stageline
- Inte kategoriserad Donexon
- Inte kategoriserad Eve Audio
- Inte kategoriserad Axagon
- Inte kategoriserad Linq
- Inte kategoriserad Wortmann AG
- Inte kategoriserad AEA
- Inte kategoriserad DiGiGrid
- Inte kategoriserad Sanofi
- Inte kategoriserad Mitzu
- Inte kategoriserad Avteq
- Inte kategoriserad Seaward
- Inte kategoriserad Omega Altise
- Inte kategoriserad Fizzics
- Inte kategoriserad XFX
- Inte kategoriserad Leynew
- Inte kategoriserad Lauten Audio
- Inte kategoriserad Cropico
- Inte kategoriserad Sunwoda
- Inte kategoriserad Schleich
- Inte kategoriserad Unitech
- Inte kategoriserad FXLab
- Inte kategoriserad Middle Atlantic
- Inte kategoriserad Kincrome
- Inte kategoriserad Vincent
- Inte kategoriserad BC Acoustique
- Inte kategoriserad Brockhaus HEUER
- Inte kategoriserad National Geographic
- Inte kategoriserad Reishunger
- Inte kategoriserad Ergotec
- Inte kategoriserad Dupla
- Inte kategoriserad APSystems
- Inte kategoriserad IODD
- Inte kategoriserad BYD
- Inte kategoriserad Tektronix
- Inte kategoriserad Aqua Medic
- Inte kategoriserad Gold Note
- Inte kategoriserad Oromed
- Inte kategoriserad Pylontech
- Inte kategoriserad Fire Sense
- Inte kategoriserad Grüniq
- Inte kategoriserad Goodwe
- Inte kategoriserad Moki
- Inte kategoriserad Enertex
- Inte kategoriserad IOTAVX
- Inte kategoriserad Creality
- Inte kategoriserad Ovation
- Inte kategoriserad InAlto
- Inte kategoriserad MDT
- Inte kategoriserad Enviroswim
- Inte kategoriserad Dobar
- Inte kategoriserad Vevor
- Inte kategoriserad Ovente
- Inte kategoriserad PowerColor
- Inte kategoriserad ISpring
- Inte kategoriserad WeFix
- Inte kategoriserad BCA
- Inte kategoriserad Serpent
- Inte kategoriserad Saki
- Inte kategoriserad Smart365
- Inte kategoriserad Fosi Audio
- Inte kategoriserad ChargeHub
- Inte kategoriserad PUR
- Inte kategoriserad Eldat
- Inte kategoriserad NEP
- Inte kategoriserad SoundSwitch
- Inte kategoriserad Sera
- Inte kategoriserad Dostmann Electronic
- Inte kategoriserad A-NeuVideo
- Inte kategoriserad Murideo
- Inte kategoriserad ToughTested
- Inte kategoriserad JBC
- Inte kategoriserad DV Mark
- Inte kategoriserad MOON
- Inte kategoriserad Cuggl
- Inte kategoriserad HABAU
- Inte kategoriserad CVW
- Inte kategoriserad Majority
- Inte kategoriserad Earbreeze
- Inte kategoriserad S.M.S.L
- Inte kategoriserad Möhlenhoff
- Inte kategoriserad Taqua
- Inte kategoriserad NightStick
- Inte kategoriserad ChyTV
- Inte kategoriserad Brainstorm
- Inte kategoriserad Colonial Elegance
- Inte kategoriserad Overtone Labs
- Inte kategoriserad IBEAM
- Inte kategoriserad Bühnen
- Inte kategoriserad Blukac
- Inte kategoriserad BendixKing
- Inte kategoriserad Tube-Tech
- Inte kategoriserad TCW Technologies
- Inte kategoriserad UNITEK
- Inte kategoriserad CoolerMaster
- Inte kategoriserad Rexing
- Inte kategoriserad NuPrime
- Inte kategoriserad The T.mix
- Inte kategoriserad Regula-Werk King
- Inte kategoriserad Inter-M
- Inte kategoriserad MIDI Solutions
- Inte kategoriserad Positive Grid
- Inte kategoriserad Amgrow
- Inte kategoriserad Xaphoon
- Inte kategoriserad Winchester
- Inte kategoriserad Lampa
- Inte kategoriserad Sinus Live
- Inte kategoriserad Sureguard
- Inte kategoriserad QuickCool
- Inte kategoriserad Smit Visual
- Inte kategoriserad NZR
- Inte kategoriserad Toparc
- Inte kategoriserad Oro-Med
- Inte kategoriserad Hex
- Inte kategoriserad Baby Cakes
- Inte kategoriserad Deflecto
- Inte kategoriserad ELMEKO
- Inte kategoriserad Tesseract Modular
- Inte kategoriserad Sport Dog
- Inte kategoriserad Nowsonic
- Inte kategoriserad On Air
- Inte kategoriserad Acoustic Solutions
- Inte kategoriserad E-ast
- Inte kategoriserad Hubble Connected
- Inte kategoriserad ELTA Music
- Inte kategoriserad Oliveri
- Inte kategoriserad Dragonshock
- Inte kategoriserad We-Vibe
- Inte kategoriserad Budda
- Inte kategoriserad Electronics International
- Inte kategoriserad Lamar
- Inte kategoriserad Atlantis Land
- Inte kategoriserad White Lightning
- Inte kategoriserad Deye
- Inte kategoriserad My Wall
- Inte kategoriserad GEV
- Inte kategoriserad Frient
- Inte kategoriserad Kaiser Fototechnik
- Inte kategoriserad Hoymiles
- Inte kategoriserad Vishay
- Inte kategoriserad Sonorous
- Inte kategoriserad Rooboost
- Inte kategoriserad Bitspower
- Inte kategoriserad JMAZ Lighting
- Inte kategoriserad EAT
- Inte kategoriserad Comar
- Inte kategoriserad Freedor
- Inte kategoriserad Start International
- Inte kategoriserad C2G
- Inte kategoriserad AXITEC
- Inte kategoriserad Lingg & Janke
- Inte kategoriserad Auralex
- Inte kategoriserad Pieps
- Inte kategoriserad Innovative
- Inte kategoriserad Lynx Technik
- Inte kategoriserad Yuede
- Inte kategoriserad ClimeMET
- Inte kategoriserad Pliant Technologies
- Inte kategoriserad Prompter People
- Inte kategoriserad Astropet
- Inte kategoriserad Busch + Müller
- Inte kategoriserad Canopia
- Inte kategoriserad Wabeco
- Inte kategoriserad Swingline GBC
- Inte kategoriserad Spelsberg
- Inte kategoriserad Staudte-Hirsch
- Inte kategoriserad Evolis
- Inte kategoriserad Universal Remote Control
- Inte kategoriserad Soundsphere
- Inte kategoriserad Lantronix
- Inte kategoriserad Kino Flo
- Inte kategoriserad Aqua Computer
- Inte kategoriserad HEDD
- Inte kategoriserad Vinpower Digital
- Inte kategoriserad Magivaac
- Inte kategoriserad Lindemann
- Inte kategoriserad Silent Angel
- Inte kategoriserad Bavaria By Einhell
- Inte kategoriserad Healthy Choice
- Inte kategoriserad IOptron
- Inte kategoriserad ZWO
- Inte kategoriserad Bbf
- Inte kategoriserad Club 3D
- Inte kategoriserad Sprolink
- Inte kategoriserad Thermionic Culture
- Inte kategoriserad Watercool
- Inte kategoriserad Moultrie
- Inte kategoriserad Skaarhoj
- Inte kategoriserad Microboards
- Inte kategoriserad Whitestone
- Inte kategoriserad BMB
- Inte kategoriserad Advance
- Inte kategoriserad Arylic
- Inte kategoriserad Gem Toys
- Inte kategoriserad Mount-It!
- Inte kategoriserad Cloud
- Inte kategoriserad Sandia Aerospace
- Inte kategoriserad EK Water Blocks
- Inte kategoriserad Lamptron
- Inte kategoriserad PS Audio
- Inte kategoriserad Gudsen
- Inte kategoriserad Café
- Inte kategoriserad Zendure
- Inte kategoriserad Envertech
- Inte kategoriserad Phanteks
- Inte kategoriserad Prism Sound
- Inte kategoriserad MoFi
- Inte kategoriserad Gosund
- Inte kategoriserad ID-Tech
- Inte kategoriserad Artecta
- Inte kategoriserad DMT
- Inte kategoriserad FSP/Fortron
- Inte kategoriserad IDIS
- Inte kategoriserad CM Storm
- Inte kategoriserad Meopta
- Inte kategoriserad MARTOR
- Inte kategoriserad SMART Technologies
- Inte kategoriserad Lumantek
- Inte kategoriserad Transparent
- Inte kategoriserad Audiotec Fischer
- Inte kategoriserad SEADA
- Inte kategoriserad Honey-Can-Do
- Inte kategoriserad Promise Technology
- Inte kategoriserad Deity
- Inte kategoriserad Patriot
- Inte kategoriserad Taga Harmony
- Inte kategoriserad B.E.G.
- Inte kategoriserad Fixpoint
- Inte kategoriserad Enerdrive
- Inte kategoriserad Respironics
- Inte kategoriserad ChamSys
- Inte kategoriserad TESLA Electronics
- Inte kategoriserad Intesis
- Inte kategoriserad Nethix
- Inte kategoriserad Pluto
- Inte kategoriserad Laine
- Inte kategoriserad 3Doodler
- Inte kategoriserad Soundskins
- Inte kategoriserad Middle Atlantic Products
- Inte kategoriserad Doepke
- Inte kategoriserad Datapath
- Inte kategoriserad Loctite
- Inte kategoriserad Antelope
- Inte kategoriserad Vertiv
- Inte kategoriserad Astera
- Inte kategoriserad Polyend
- Inte kategoriserad BASSBOSS
- Inte kategoriserad Sabco
- Inte kategoriserad Sensative
- Inte kategoriserad Plasma Cloud
- Inte kategoriserad Flo
- Inte kategoriserad Sheeran Looper
- Inte kategoriserad Applico
- Inte kategoriserad Jungle Gym
- Inte kategoriserad Smart Media
- Inte kategoriserad TOGU
- Inte kategoriserad BLUEPALM
- Inte kategoriserad Hacienda
- Inte kategoriserad Christmaxx
- Inte kategoriserad IStarUSA
- Inte kategoriserad Code
- Inte kategoriserad Mivar
- Inte kategoriserad SolaX Power
- Inte kategoriserad IPGARD
- Inte kategoriserad Weston
- Inte kategoriserad EZ Dupe
- Inte kategoriserad AURALiC
- Inte kategoriserad Qian
- Inte kategoriserad AkYtec
- Inte kategoriserad Absco
- Inte kategoriserad Schatten Design
- Inte kategoriserad LEDs-ON
- Inte kategoriserad Bestgreen
- Inte kategoriserad MyPOS
- Inte kategoriserad Truetone
- Inte kategoriserad Stages
- Inte kategoriserad Starlink
- Inte kategoriserad HDFury
- Inte kategoriserad Favero
- Inte kategoriserad Durvet
- Inte kategoriserad MAAS
- Inte kategoriserad KNEKT
- Inte kategoriserad Gator Frameworks
- Inte kategoriserad Teia
- Inte kategoriserad The Joy Factory
- Inte kategoriserad Yuer
- Inte kategoriserad OSEE
- Inte kategoriserad OLLO
- Inte kategoriserad Axor
- Inte kategoriserad Gustard
- Inte kategoriserad Enhance
- Inte kategoriserad MEPROLIGHT
- Inte kategoriserad Tactical Fiber Systems
- Inte kategoriserad GVision
- Inte kategoriserad Veber
- Inte kategoriserad PurAthletics
- Inte kategoriserad SMS
- Inte kategoriserad Carlo Gavazzi
- Inte kategoriserad Richgro
- Inte kategoriserad Varaluz
- Inte kategoriserad Milesight
- Inte kategoriserad Dehner
- Inte kategoriserad Edwards
- Inte kategoriserad Victor Technology
- Inte kategoriserad Lastolite
- Inte kategoriserad Lowepro
- Inte kategoriserad MIOPS
- Inte kategoriserad WiiM
- Inte kategoriserad Bluebird
- Inte kategoriserad Cotek
- Inte kategoriserad EA Elektro Automatik
- Inte kategoriserad CMI
- Inte kategoriserad Grand Effects
- Inte kategoriserad SunPower
- Inte kategoriserad Hensel
- Inte kategoriserad Westland
- Inte kategoriserad Bahr
- Inte kategoriserad Black Line
- Inte kategoriserad Sodapop
- Inte kategoriserad Enbrighten
- Inte kategoriserad Vicoustic
- Inte kategoriserad Albert Heijn
- Inte kategoriserad Yphix
- Inte kategoriserad TAURUS Titanium
- Inte kategoriserad Magliner
- Inte kategoriserad Magmatic
- Inte kategoriserad PulseAudio
- Inte kategoriserad Comfortisse
- Inte kategoriserad Cayin
- Inte kategoriserad Ambient Weather
- Inte kategoriserad Videotel Digital
- Inte kategoriserad Zylight
- Inte kategoriserad Smith-Victor
- Inte kategoriserad HuddleCamHD
- Inte kategoriserad Technical Pro
- Inte kategoriserad MooreCo
- Inte kategoriserad BIOS Living
- Inte kategoriserad Connection
- Inte kategoriserad Blind Spot
- Inte kategoriserad Badiona
- Inte kategoriserad VMV
- Inte kategoriserad Digigram
- Inte kategoriserad Mutec
- Inte kategoriserad Black Hydra
- Inte kategoriserad Expressive E
- Inte kategoriserad Merging
- Inte kategoriserad Bellari
- Inte kategoriserad CSL
- Inte kategoriserad Altman
- Inte kategoriserad EXO
- Inte kategoriserad Hawke
- Inte kategoriserad Defender
- Inte kategoriserad Betty Bossi
- Inte kategoriserad FoxFury
- Inte kategoriserad Eller
- Inte kategoriserad Rotatrim
- Inte kategoriserad Peak Design
- Inte kategoriserad Uniropa
- Inte kategoriserad Eura
- Inte kategoriserad ESE
- Inte kategoriserad Claypaky
- Inte kategoriserad Casa Deco
- Inte kategoriserad Hecate
- Inte kategoriserad Jinbei
- Inte kategoriserad Christmas Time
- Inte kategoriserad Comprehensive
- Inte kategoriserad Dobot
- Inte kategoriserad Nearity
- Inte kategoriserad Easyrig
- Inte kategoriserad Digitalinx
- Inte kategoriserad Gra-Vue
- Inte kategoriserad WHD
- Inte kategoriserad On-Stage
- Inte kategoriserad Sumiko
- Inte kategoriserad Indiana Line
- Inte kategoriserad TechBite
- Inte kategoriserad Blackburn
- Inte kategoriserad Inverx
- Inte kategoriserad Primewire
- Inte kategoriserad XCell
- Inte kategoriserad Yellow Garden Line
- Inte kategoriserad Titanwolf
- Inte kategoriserad Uplink
- Inte kategoriserad Mybeo
- Inte kategoriserad Medicinalis
- Inte kategoriserad Bearware
- Inte kategoriserad Liam&Daan
- Inte kategoriserad Traco Power
- Inte kategoriserad Microair
- Inte kategoriserad Perfect Christmas
- Inte kategoriserad Bebob
- Inte kategoriserad Fiilex
- Inte kategoriserad PTZ Optics
- Inte kategoriserad Xcellon
- Inte kategoriserad Sescom
- Inte kategoriserad Robus
- Inte kategoriserad CAME-TV
- Inte kategoriserad Rosco
- Inte kategoriserad Wimberley
- Inte kategoriserad Nureva
- Inte kategoriserad Revic
- Inte kategoriserad Galcon
- Inte kategoriserad Telmax
- Inte kategoriserad Apollo Design
- Inte kategoriserad DEERSYNC
- Inte kategoriserad Gen Energy
- Inte kategoriserad JoeCo
- Inte kategoriserad Holosun
- Inte kategoriserad Aconatic
- Inte kategoriserad Kluge
- Inte kategoriserad Arovec
- Inte kategoriserad SecureSafe
- Inte kategoriserad CubuSynth
- Inte kategoriserad Exelpet
- Inte kategoriserad Aplic
- Inte kategoriserad Imarflex
- Inte kategoriserad Analog Way
- Inte kategoriserad Tempmate
- Inte kategoriserad Stalco
- Inte kategoriserad Carlsbro
- Inte kategoriserad Ventev
- Inte kategoriserad Mobotix
- Inte kategoriserad Steelbody
- Inte kategoriserad PureLink
- Inte kategoriserad UNYKAch
- Inte kategoriserad VAVA
- Inte kategoriserad Mammut
- Inte kategoriserad Modbap Modular
- Inte kategoriserad Bluestork
- Inte kategoriserad INOGENI
- Inte kategoriserad Linhof
- Inte kategoriserad Carry-on
- Inte kategoriserad AddLiving
- Inte kategoriserad IOIO
- Inte kategoriserad Nimbus
- Inte kategoriserad Coca-Cola
- Inte kategoriserad City Theatrical
- Inte kategoriserad Acros
- Inte kategoriserad Redback Technologies
- Inte kategoriserad Vent-A-Hood
- Inte kategoriserad GoXtreme
- Inte kategoriserad Bome
- Inte kategoriserad One Control
- Inte kategoriserad EQ Acoustics
- Inte kategoriserad AV Tool
- Inte kategoriserad Aquael
- Inte kategoriserad NEXTO DI
- Inte kategoriserad Thermarest
- Inte kategoriserad Fortinge
- Inte kategoriserad RF-Links
- Inte kategoriserad LiveU
- Inte kategoriserad Y-brush
- Inte kategoriserad Austral
- Inte kategoriserad HMD
- Inte kategoriserad Luxul
- Inte kategoriserad Cherub
- Inte kategoriserad ProLights
- Inte kategoriserad Xinfrared
- Inte kategoriserad Brizo
- Inte kategoriserad SAVS
- Inte kategoriserad I-PRO
- Inte kategoriserad Europalms
- Inte kategoriserad DuroStar
- Inte kategoriserad Waterstone
- Inte kategoriserad Huslog
- Inte kategoriserad Mr Steam
- Inte kategoriserad DVDO
- Inte kategoriserad A-Designs
- Inte kategoriserad Henry Engineering
- Inte kategoriserad Primacoustic
- Inte kategoriserad HomeCraft
- Inte kategoriserad Heusinkveld
- Inte kategoriserad EnOcean
- Inte kategoriserad Storcube
- Inte kategoriserad Varia
- Inte kategoriserad Gurari
- Inte kategoriserad Fezz
- Inte kategoriserad ASI
- Inte kategoriserad Lexivon
- Inte kategoriserad Graff
- Inte kategoriserad Swiss Eye
- Inte kategoriserad Cane Creek
- Inte kategoriserad EPEVER
- Inte kategoriserad KED
- Inte kategoriserad Caberg
- Inte kategoriserad Exped
- Inte kategoriserad Lawn Star
- Inte kategoriserad Edouard Rousseau
- Inte kategoriserad GameDay
- Inte kategoriserad Sparkle
- Inte kategoriserad Söll
- Inte kategoriserad X-Lite
- Inte kategoriserad AXESS
- Inte kategoriserad Glemm
- Inte kategoriserad Ridem
- Inte kategoriserad StarIink
- Inte kategoriserad Belanger
- Inte kategoriserad Røde
- Inte kategoriserad Noyafa
- Inte kategoriserad Envertec
- Inte kategoriserad Nordic Winter
- Inte kategoriserad Volcano
- Inte kategoriserad Wire Technologies
- Inte kategoriserad Taco Tuesday
- Inte kategoriserad CEEM
- Inte kategoriserad IMM Photonics
- Inte kategoriserad Field Optics
- Inte kategoriserad Robern
- Inte kategoriserad Signature Hardware
- Inte kategoriserad GRAUGEAR
- Inte kategoriserad Sure Petcare
- Inte kategoriserad Sortimo
- Inte kategoriserad Livall
- Inte kategoriserad Beaphar
- Inte kategoriserad Catit
- Inte kategoriserad WarmlyYours
- Inte kategoriserad Mebby
- Inte kategoriserad TONI&GUY
- Inte kategoriserad Balam Rush
- Inte kategoriserad Roesle
- Inte kategoriserad Oreg
- Inte kategoriserad Karran
- Inte kategoriserad Duravit
- Inte kategoriserad Topex
- Inte kategoriserad OOONO
- Inte kategoriserad CaviLock
- Inte kategoriserad Origin Storage
- Inte kategoriserad Kostal
- Inte kategoriserad Stamos
- Inte kategoriserad Ulsonix
- Inte kategoriserad Stamony
- Inte kategoriserad Uniprodo
- Inte kategoriserad Physa
- Inte kategoriserad Pitsos
- Inte kategoriserad Yamazen
- Inte kategoriserad Lantus
- Inte kategoriserad STANDARD
- Inte kategoriserad BigBlue
- Inte kategoriserad RC Allen
- Inte kategoriserad Plastkon
- Inte kategoriserad Triplett
- Inte kategoriserad Soler & Palau
- Inte kategoriserad Tele Vue
- Inte kategoriserad Wiesenfield
- Inte kategoriserad Bulgin
- Inte kategoriserad Pure 100
- Inte kategoriserad Petite Chérie
- Inte kategoriserad Njoy
- Inte kategoriserad Studio Titan
- Inte kategoriserad AstrHori
- Inte kategoriserad Icron
- Inte kategoriserad Pyrex
- Inte kategoriserad Platypus
- Inte kategoriserad Trezor
- Inte kategoriserad Ferrofish
- Inte kategoriserad HPRC
- Inte kategoriserad Really Right Stuff
- Inte kategoriserad Decimator
- Inte kategoriserad Chimera
- Inte kategoriserad ButtKicker
- Inte kategoriserad Blonder Tongue
- Inte kategoriserad Crystal Video
- Inte kategoriserad Tilta
- Inte kategoriserad Luxli
- Inte kategoriserad PAG
- Inte kategoriserad Senseca
- Inte kategoriserad NeoMounts
- Inte kategoriserad Western Co.
- Inte kategoriserad ProFlo
- Inte kategoriserad Rohl
- Inte kategoriserad Violectric
- Inte kategoriserad Aalberg Audio
- Inte kategoriserad Ruggard
- Inte kategoriserad OM SYSTEM
- Inte kategoriserad Moman
- Inte kategoriserad DiversiTech
- Inte kategoriserad Evooch
- Inte kategoriserad Bolin Technology
- Inte kategoriserad Total Chef
- Inte kategoriserad Total
- Inte kategoriserad PoLabs
- Inte kategoriserad Taiji
- Inte kategoriserad Digi-Pas
- Inte kategoriserad Pfister
- Inte kategoriserad Fellow
- Inte kategoriserad Kolcraft
- Inte kategoriserad Klauke
- Inte kategoriserad Axler
- Inte kategoriserad Symmons
- Inte kategoriserad Jacuzzi
- Inte kategoriserad Gerber
- Inte kategoriserad Royale
- Inte kategoriserad Venicci
- Inte kategoriserad Das Keyboard
- Inte kategoriserad Schaffner
- Inte kategoriserad Vitec
- Inte kategoriserad Nicols
- Inte kategoriserad ARNOLD Lichttechnik
- Inte kategoriserad Matterport
- Inte kategoriserad API Audio
- Inte kategoriserad Moomin
- Inte kategoriserad Belulu
- Inte kategoriserad Jedo
- Inte kategoriserad RIX
- Inte kategoriserad Bayco
- Inte kategoriserad Dinstar
- Inte kategoriserad EMeet
- Inte kategoriserad Noordi
- Inte kategoriserad Corona
- Inte kategoriserad Coors Light
- Inte kategoriserad Arco
- Inte kategoriserad KoolScapes
- Inte kategoriserad Netter Vibration
- Inte kategoriserad Califone
- Inte kategoriserad Dynon Avionics
- Inte kategoriserad Uvex
- Inte kategoriserad UAvionix
- Inte kategoriserad LARQ
- Inte kategoriserad ORCA
- Inte kategoriserad YA-MAN
- Inte kategoriserad CRAFT + MAIN
- Inte kategoriserad V-Tone
- Inte kategoriserad Hellberg
- Inte kategoriserad Stelzner
- Inte kategoriserad LightKeeper Pro
- Inte kategoriserad BMAX
- Inte kategoriserad Cressi
- Inte kategoriserad Singercon
- Inte kategoriserad Pivo
- Inte kategoriserad Sharkbite
- Inte kategoriserad Lively
- Inte kategoriserad CatSynth
- Inte kategoriserad Ember
- Inte kategoriserad Sifflus
- Inte kategoriserad ACOPower
- Inte kategoriserad Cosi Home
- Inte kategoriserad Clean Paper
- Inte kategoriserad GeoBox
- Inte kategoriserad URC
- Inte kategoriserad Advanced Network Devices
- Inte kategoriserad Telycam
- Inte kategoriserad SafeMi
- Inte kategoriserad XTRARM
- Inte kategoriserad Rock N Roller
- Inte kategoriserad DQ
- Inte kategoriserad Nextorage
- Inte kategoriserad JLCooper
- Inte kategoriserad Twisted Electrons
- Inte kategoriserad OptiTrack
- Inte kategoriserad ZZ-2
- Inte kategoriserad Doona
- Inte kategoriserad SolidDrive
- Inte kategoriserad Induction Dynamics
- Inte kategoriserad USL
- Inte kategoriserad SKB
- Inte kategoriserad Cyber Acoustics
- Inte kategoriserad Freewell
- Inte kategoriserad Bright Starts
- Inte kategoriserad QZ
- Inte kategoriserad MSolutions
- Inte kategoriserad Storm
- Inte kategoriserad Helight
- Inte kategoriserad Xuma
- Inte kategoriserad Go-eCharger
- Inte kategoriserad DARTS
- Inte kategoriserad Singularity Computers
- Inte kategoriserad Boehringer Ingelheim
- Inte kategoriserad Sesame Street
- Inte kategoriserad Ingenuity
- Inte kategoriserad Digital Forecast
- Inte kategoriserad Autoscript
- Inte kategoriserad Mac Tools
- Inte kategoriserad InvisibleShield
- Inte kategoriserad Voigtlander
- Inte kategoriserad Hailo
- Inte kategoriserad XD-Design
- Inte kategoriserad Gator
- Inte kategoriserad SmartGyro
- Inte kategoriserad Star Belly
- Inte kategoriserad Phase Technology
- Inte kategoriserad Casr
- Inte kategoriserad Hypnos
- Inte kategoriserad CkeyiN
- Inte kategoriserad BlaknBlu
- Inte kategoriserad Louroe Electronics
- Inte kategoriserad Orbitrek
- Inte kategoriserad Zaahn
- Inte kategoriserad Livn
- Inte kategoriserad Kaorka
- Inte kategoriserad MOOOV
- Inte kategoriserad Crem
- Inte kategoriserad Sportime
- Inte kategoriserad Quasar Science
- Inte kategoriserad Zeapon
- Inte kategoriserad CLIMAQUA
- Inte kategoriserad Tece
- Inte kategoriserad Beltronics
- Inte kategoriserad Lahti Pro
- Inte kategoriserad Jan Nowak
- Inte kategoriserad HiRO
- Inte kategoriserad Vantrue
- Inte kategoriserad Elight
- Inte kategoriserad Forodi
- Inte kategoriserad CELLFAST
- Inte kategoriserad MOZOS
- Inte kategoriserad Buxton
- Inte kategoriserad ViewZ
- Inte kategoriserad IsoTek
- Inte kategoriserad Miracle Smile
- Inte kategoriserad Zacuto
- Inte kategoriserad VARI-LITE
- Inte kategoriserad Real Cable
- Inte kategoriserad Pengo
- Inte kategoriserad Sophos
- Inte kategoriserad Kica
- Inte kategoriserad Racktime
- Inte kategoriserad Leba
- Inte kategoriserad Kendall Howard
- Inte kategoriserad Starlight Xpress
- Inte kategoriserad Sightron
- Inte kategoriserad Simmons
- Inte kategoriserad Infosec
- Inte kategoriserad Therm-a-Rest
- Inte kategoriserad Hoffman
- Inte kategoriserad Elbro
- Inte kategoriserad Diamond Audio
- Inte kategoriserad Nofred
- Inte kategoriserad Newport Brass
- Inte kategoriserad Ambient
Nyaste Inte kategoriserad Manualer

9 April 2025

9 April 2025

9 April 2025

9 April 2025

9 April 2025

9 April 2025

9 April 2025

9 April 2025

9 April 2025

9 April 2025