Hobbywing XeRun XR8 Plus G2S Bruksanvisning
Hobbywing
Radiostyrda leksaker
XeRun XR8 Plus G2S
Läs nedan 📖 manual på svenska för Hobbywing XeRun XR8 Plus G2S (2 sidor) i kategorin Radiostyrda leksaker. Denna guide var användbar för 15 personer och betygsatt med 4.5 stjärnor i genomsnitt av 2 användare
Sida 1/2
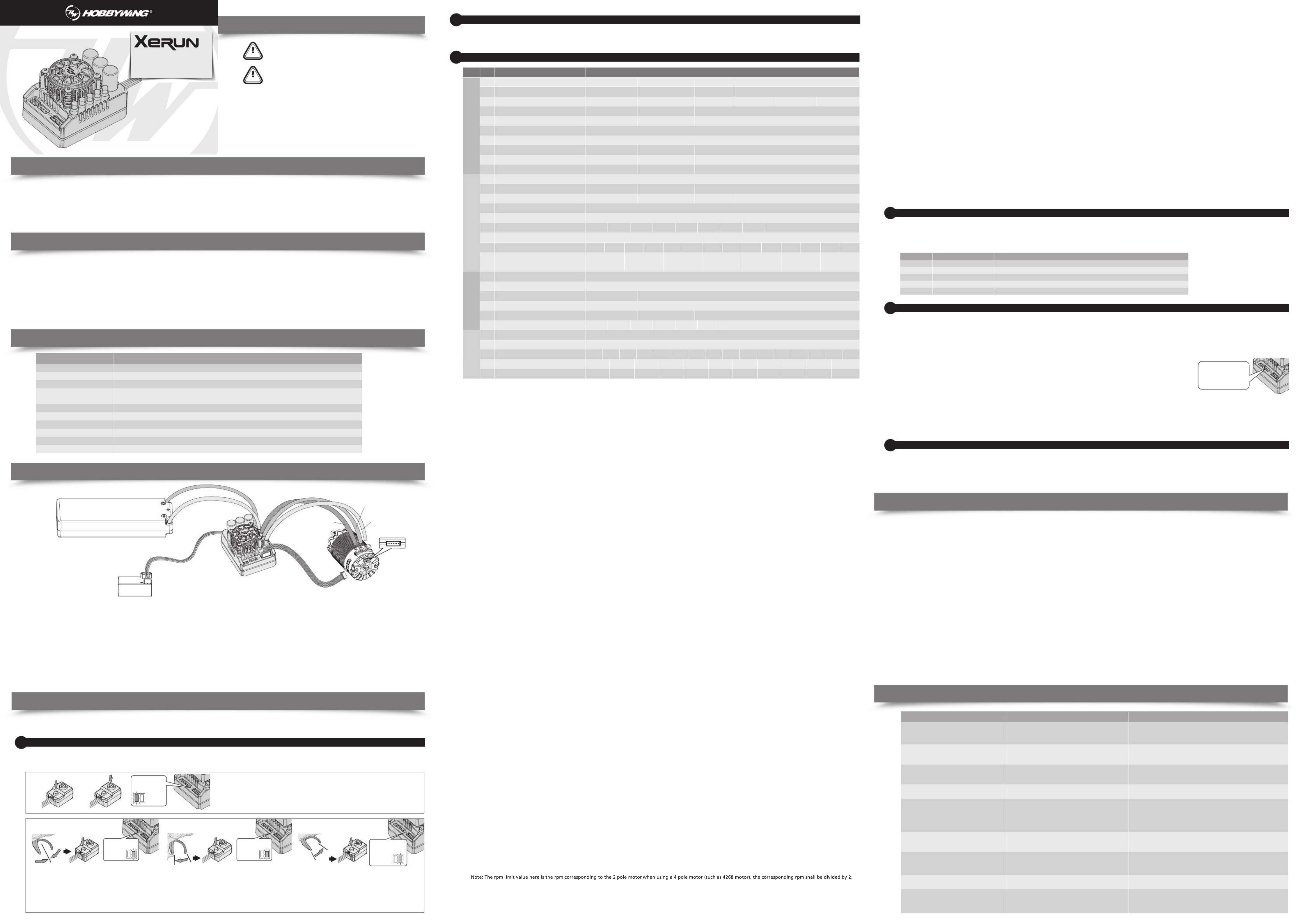
Thank you for purchasing this HOBBYWING product! The power of
brushless power system is powerful. Any improper use may cause
personal injury and damage to the product and related devices. We
strongly recommend reading through this user manual before use and
strictly abide by the specified operating procedures. We shall not be
liable for any liability arising from the use of this product, including but
not limited to reimbursement for incidental or indirect losses.
Meanwhile, we do not assume any responsibility caused by
unauthorized modification of the product. We have the right to change
the product design, appearance, performance and use requirements
without notice.
Progammable Items
3
• Please make sure that all wires and parts is insulated before connecting the ESC, because short circuit will damage the ESC.
• Please connect all parts properly. Poor connection will damage the device and you would not control the vehicle normally.
• Please check power devices and instructions to ensure the matching of power is reasonable.
• Please use 60W of welding devices to weld input/output wire and the plug of the ESC to ensure reliable welding.
• Please do not run at full speed if the tire left the ground, otherwise the tire will burst and cause injury.
• The external temperature of the ESC cannot exceed 90 /194 . High temperature will destroy the ESC and the motor. Open the overheat protection function of the ESC.℃ ℉
• Please remember to disconnect the battery and the ESC. If not, the ESC will consume electric energy and the battery will be completely discharged which will lead to the
failure of battery or ESC. We are not responsible for any damage caused by this!
• Built-in 5 common profiles, suitable for all 1/8 Racing, select and use instantly. (e.g. Zero timing-Blinky mode, 1/8 Off-Road Racing, 1/8 On-Road Racing, 1/8 GT Racing, 1/8 Sport mode).
• There are 30 built-in adjustable parameters to set various power requirements. The parameters can be imported and exported, which is convenient for drivers to communicate with and
learn from each other.
• Support the firmware upgrade of the ESC (The multi-function LCD programming box or OTA Programmer is needed to purchase). You can enjoy the latest functions.
• Support 48 degrees Boost and Turbo timing. When matching with XERUN 4268/4274 G3 motor, the Max. Speed can be promoted by 50%, easily win your rival.
• Multiple function: Low voltage protection, thermal protection of the ESC, motor and capacitor.
• Built-in switch mode BEC with a maximum output of 15A and voltage adjustable from 6V to 8.4V (step: 0.1V) for usage with servos & other devices require different voltages.
• The built-in reverse connection protection circuit of the ESC avoid the damage to the ESC due to reverse connection.
• The record function of real-time data: Open this function by connecting the ESC with HW Link (OTA Programmer is needed to purchase) and mobile App can check throttle quantity, Voltage,
Current, Temperature, RPM and other data in real time, and obtain the running status of the ESC and motor.
• The record function of off-line data: It can not only read out the extreme value data such as the maximum temperature of the esc and motor,maximum RPM of the motor through the LCD
program box or HW link app (OTA Programmer is needed to purchase), but also view the historical running data (graph) in the data record in HW link app (OTA Programmer is needed to purchase).
Cont./Peak Current
Motor Type
Applications
LiPo Cells
BEC Output
Cooling Fan
Size/Weight
Connectors
Programming Method
200A / 1080A
Sensored / Sensorless Brushless Motors
1/8 On-Road/Off-Road/Truggy Racing
2-6S LiPo
6-8.4V Adjustable, Continuous/Peak Current: 6A/15A(Switch-mode)
Powered by the stable BEC voltage of 6-8.4V
56.1(L) x 42.1(W) x 38.5(H)mm / 122g (W/O Wires)
Input End: No Connectors; Output End: No Connectors
Multifunction LCD Program Box, OTA Programmer
Mode XERUN XR8 Plus G2S
Motor Limit With 4S Lipo: KV 3000 4268 / 4274 Size motor≤
With 6S Lipo: KV 2400 4274 Size motor≤
03
Features
02
Warnings
04
Specifications
05
Connections
CA UT IONS
AT T ENT ION
When first use the ESC or the transmitter changes “TRIM” tune, D/R,EPA and other parameters, the throttle range is need to reset. We strongly recommend to open the fail safe function of
the transmitter, set the no signal protection of throttle channel(“F/S”) to close the output or set the protection value to the throttle neutral position. Thus the motor can stop running if the
receiver cannot receive the signal of the transmitter. The calibrating steps of throttle is as follows:
06
ESC Setup
Set the throttle range
1
01
Disclaimer
Please connect the wire correctly according to the instructions and drawing:
1. Motor Wiring:
There is difference between connection of sensored brushless motor and sensorless brushless motor. Please according to the following wiring method:
A. Connect sensored brushless motor:
There is strict wiring order from the ESC to the motor, the three A/B/C ESC wires must connect to the three A/B/C motor wires correspondingly. Next, connect the ESC sensor port and the
motor sensor port with the stock 6-pin sensor cable. If you don’t plug the sensor cable in, your ESC will still work in sensorless mode even if you’re using a sensored motor.
Note:If the forward and backward is reverse after installing the motor, please modify “no. 1I” parameters “Motor Rotation” to change the direction.
B. Sensorless Motor Wiring:
Users do not need to be worried in r egards to the connectivity with the A/B/C(ESC and motor) as ther e is no polarity. You may find it necessary to swap two wir es if the motor runs in reverse.
2. Receiver Wiring:
Insert the throttle control flat cable of ESC into the throttle channel (i.e. THROTTLE channel) of the receiver. Since the red line in the flat cable outputs 6-8.4v voltage to the receiver and
steering servo. Please do not supply additional power to the receiver, otherwise the electric adjustment may be damaged.
3. Battery Wiring:
Please make sure that the (+) pole of the ESC is connected to the (+) of the battery, and the (-) pole is connected to the (-). If connect reversely, the ESC cannot start up. (Add the picture of
connecting battery here.)
Warning!
This is an extremely powerful system. For your safety and the safety of those around you, we strongly recommend removing the pinion gear attached to the motor before
calibrating and setting this system. It is also advisable to keep the wheels in the air when you turn on the ESC.
20211119
1) Illustration of power on/off: Short press the ON/OFF key to turn on the ESC in the off state, and long press the ON/OFF key to turn off the ESC.
2) Beep illustration when turn on the ESC: When turn on ESC under normal conditions (i.e. it is started without pressing the SET key), the motor will emit several Beeps to indicate the LiPo
cells. For example, “Beep, Beep, Beep” means 3S, “Beep, Beep, Beep, Beep” means 4S.
Power on/o and Beep illustration
2
1. Turn on the transmitter, ensure all parameters (D/R, EPA, ATL) on the throttle channel are at
default (100%). For transmitter without LCD, please turn the knob to the maximum, and the
throttle “TRIM” to 0. (If the transmitter without LCD, turn the knob to the middle point).
2. Start by turning on the transmitter with the ESC turned off but connected to a battery. Holding
the“SET” button then press the “ON/OFF” button, the RED LED on the ESC starts to flash (The
motor beeps at the same time), and then release the “SET” button immediately.
Note : Beeps from the motor may be low sometimes, and you can check the LED status instead.
Hold the
SET button.
Press the
ON/OFF button Release the SET
button once the LED
flashes.
3、Set the neutral point, the full throttle endpoint and the full brake endpoint.
• Leave transmitter at the neutral position, press the “SET” button, the RED LED dies out and the GREEN LED flashes 1 time and the motor beeps 1 time to accept the neutral position.
• Pull the throttle trigger to the full throttle position, press the “SET” button, the GREEN LED blinks 2 times and the motor beeps 2 times to accept the full throttle endpoint.
• Push the throttle trigger to the full brake position, press the “SET” button, the GREEN LED blinks 3 times and the motor beeps 3 times to accept the full brake endpoint.
Note:
• The end position of forward: Pull the trigger to the maximum throttle position if it is pistol-style transmitter. Push the throttle to the top if it is board-style transmitter.
• The end position of backward: Push the trigger to the maximum brake position if it is pistol-style transmitter. Pull the throttle to the bottom if it is board-style transmitter.
4、The motor can be started 3 seconds after the ESC/Radio calibration is complete.
Move the throttle trigger to the neutral
position and press the SET button.
The Green LED flashes
once and motor emits
“Beep” tone.
Move the throttle trigger to the end position
of forward and press the SET button.
Move the throttle trigger to the end position
of backward and press the SET button.
The Green LED flashes
twice and motor emits
“Beep-Beep”
tone.
The Green LED flashes
three times and motor
emits “Beep-Beep-
Beep” tone.
08
Trouble Shooting
In order to make one firmware applicable to all different racing conditions, there are 5 groups of preset modes in the ESC. Users are able to change the settings of the modes provided and
match suitable gear ratio. Plug-and -screw. Users can change the settings as per the control feel, track, and rename the setting mode. For example, the name can be changed from “1/8
Off-Road” to “NC2020-1900” to indicate the NC2020 uses 1900KV. This can be saved for future reference as well.
07
Explanation for LED status
1. During the Start-up Process
• The RED LED keeps flashing rapidly indicating the ESC doesn't detect any throttle signal or the neutral throttle value stored on your ESC may be different from the current value stored on
the transmitter.
• The GREEN LED flashes “N” times indicating the number of LiPo cells you have connected to the ESC.
2. In Operation
• The throttle triggle is at the neutral:
1) In the normal mode(Non blinky mode),the RED LED turns on soild.
2) In the blinky mode(Non RPM limit mode), the boost timing and turbo timing are 0, the RED LED will blink.
3) In the RPM limit mode:
When RPM limit is 80000, the red LED long flashes once and the green LED flashes once.
When RPM limit is 74000, the red LED long flashes once and the green LED flashes twice.
When RPM limit is 68000, the red LED long flashes once and the green LED flashes three times.
When RPM limit is 62000, the red LED long flashes once and the green LED flashes four times.
When RPM limit is 56000, the red LED long flashes once and the green LED flashes five times.
When RPM limit is 50000, the red LED long flashes once and the green LED flashes six times.
• Forward: The RED LED dies out and the GREEN LED blinks when your vehicle runs forward. The GREEN LED turns solid when pulling the throttle trigger to the full (100%) throttle endpoint.
• Brake: The RED LED dies out and the GREEN LED blinks when you brake your vehicle. The GREEN LED turns solid when pushing the throttle trigger to the full brake endpoint and setting
the ”Max. Brake Force” to 100%.
• Backward: The RED LED dies out, the GREEN LED blinks when you reverse your vehicle. The GREEN LED turns solid when pushing the throttle trigger to the full brake endpoint and setting
the ”reverse force” to 100%.
3. When Some Protection is Activated
• The RED LED flashes a short, single flash and repeats “ ” indicating the low voltage cutoff protection is activated.☆, , ☆ ☆
• The GREEN LED flashes a short, single flash and repeats “ ” indicating the ESC thermal protection is activated.☆, , ☆ ☆
• The GREEN LED flashes a short, double flash and repeats “ ” indicating the motor thermal protection is activated.☆☆ ☆☆ ☆☆, ,
• The GREEN LEDS flash a short, single flash and repeats “ ” indicating that the load of ESC is heavy, the Over-Current protection is activated.☆☆☆ ☆☆☆ ☆☆☆, ,
• The GREEN LEDS flash a short, single flash and repeats “ ” indicating that the temperature of ESC and capacitor is too high, the thermal protection ☆☆☆☆☆,☆☆☆☆☆,☆☆☆☆☆
of capacitor is activated.
Preset Modes for Different Racing:
External
Programming Port
for Connecting LCD
program box or OTA
Programmer.
Here is the method of setting parameters of ESC:
Note! This ESC has a separate programming port. Please don’t connect the throttle control cable to the setting card, otherwise the setting card cannot work.
1) LCD programming box set the parameters: (Please refer to the instructions of LCD programming box for detailes)
This ESC allows LCD programming box to set parameters or LCD programming box connecting to the computer to set parameters (Use HOBBYWING USB LINK software). Before programming,
you need to connect your ESC and the LCD program box via a cable with two JR male connectors and turn on the ESC; the boot screen will show up on the LCD. Press any button on the
program box to initiate the communication between your ESC and the program box. Seconds later, “CONNECTING ESC” will be displayed, and indicates the following parameters. You can
adjust the setting via “ITEM” & “VALUE” buttons, and press the “OK (R/P)” button to save new settings to your ESC.
2) Use OTA Programmer to set parameters (Please refer to instructions of OTA Programmer for details)
This ESC allows OTA Programmer connecting to the computer, that is, plug the programming wire of OTA Programmer to the
programming port. Then use mobile phone to install HOBBYWING HW LINK App to set parameters.
3) The OTA Bluetooth module:
1) The ESC is able to record the Maximum Temperature of ESC and Motor, Minimum Battery Voltage and Maximum Motor RPM in running.
It automatically saves the recorded data to the designated area when you turn off the ESC after a run. You can check those data via a multifunction LCD program box. Users need to switch
on the ESC after the esc is connected with the program box. Long Press the “OK(R/P)” button on any “item” page, then press the “ITEM” button, the following 5 item pages will be displayed:
Mode → ESC Temperature→ Motor Temperature → Min Voltage→ Max RPM
2) The ESC running data is read through the OTA Bluetooth module.
After connecting the OTA Bluetooth module to the esc and establishing communication, you can view not only the four extreme value data recorded above, but also the real-time running
data and historical record data (graph) in the [Data Log] menu in HW link app.
Programming:
5
Here is the method of restore factory reset:
1) Restore the default values with a multifunction LCD program box
After connecting the program box to the ESC, continue to press the “ITEM” button on the program box until you see the “RESTORE DEFAULT” item, and press “OK(R/P)” to factory reset your ESC.
2) Restore the default values with a OTA Programmer (Use HW Link mobile phone App)
Connect OTA Programmer to the ESC, enter into Parameters , click “reset” to factory reset your ESC.【 】
Factory reset
6
Preset modes
4
1A: Running Mode:
Option 1: Forward with Brake
Racing mode. It has only forward and brake functions.
Option 2: Forward/ Reverse with Brake
This option is known to be the “training”mode with “Forward/Reverse with Brake” function. The vehicle only brakes on the first time you push the throttle trigger to the reverse/brake zone.If
the motor stops when the throttle trigger return to the neutral zone and then re-push the trigger to reverse zone, the vehicle will reverse, if the motor does not completely stop, then your
vehicle won’t reverse but still brake, you need to return the throttle trigger to the neutral zone and push it to reverse zone again. This method is for preventing vehicle from being accidentally
reversed.
Option 3: Forward and Reverse
This mode is often used by special vehicles. The vehicle will reverse immediately when you push the throttle triggle to the reverse zone.
1B: Max. Reverse Force:
The reverse force of the value will determine its speed. For the safety of your vehicle, we recommend using a low amount.
1C: Lipo Cells:
Auto Calculation is the default setting. If Lipo batteries are often used with the same cell count,we would recommend setting the Lipo cells manually to avoid the incorrect “Calculation”(For
example,the esc may take a not fully charged 3S Lipo as a fully 2S Lipo) ,which may cause the low-voltage cutoff protection to not function ideally.
1D: Cutoff Voltage:
The ESC will monitor the battery voltage all the time, once the voltage is lower than the threshold value, the ESC will reduce the power to 50% instantly and cutoff the power output in 40
seconds. When enters into voltage protection, the RED LED will single flash that repeats ( …….). Please set the “Cutoff Voltage” to “Disabled” or customized protection threshold ☆, , , ☆ ☆ ☆
value if you are using NiMH batteries.
Option 1: Disabled
The ESC does not cut the power off due to low voltage. We do not recommend using this option when you use any LiPo battery as you will irreversibly damage the product. It is suggested to
set to “Disabled”(But the battery would be damaged due to overcharged)
Option 2: Auto
The ESC calculates the corresponding cutoff voltage as per the number of LiPo cells it detects and the “3.5V/cell” rule. For example, if the ESC detects a 4S, the cutoff voltage protection
threshold value is 3.5x4=14.0V.
Option 3: Customized
The customized cutoff threshold is a voltage for the whole battery pack (adjustable from 5.0V to 20.4V). Please calculate the value as per the number of LiPo cells you are using. For example,
when you use a 4S and you want the cutoff voltage for each cell is 3.0V, you will need to set this item to 12V 3.0*4( )
1E: ESC Thermal Protection:
The output from the ESC will be cut off with the value you have preset. The GREEN LED flashes ( ) when the ESC temperature reaches to the preset value. The output will not resume ☆, , ☆ ☆
until the ESC temperature gets down.
Warning! Please do not disable this function unless you’re in a competition. Otherwise the high temperature may damage your ESC and even your motor.
1F: Motor Thermal Protection:
The GREEN LED flashes ( ) when the motor temperature reaches to the preset value. The output will not resume until the motor temperature gets down.☆☆ ☆☆ ☆☆, ,
Warning! Please do not disable this function unless you’re in a competition. Otherwise the high temperature may damage your motor and even your ESC. For non-Hobbywing
motor, the ESC may get this protection activated too early/late because of the different temperature sensor inside the motor. In this case, please disable this function and
monitor the motor temperature manually.
1G: BEC Voltage:
BEC voltage can be adjusted between 6.0-8.4V. 6.0V is applicable to common servo. If use high-voltage servo, set to higher voltage according to voltage marking of servo.
Warning: The setting BEC voltage should not be higher than the max. voltage of common servo, otherwise it will damage the servo or ESC.
1H: Sensor Mode:
Option 1: Full Sensored
If use XERUN 4268/74-G2/G3 motor, it can set to full sensor mode. The power system will work in the “sensored” mode at all times. The efficiency and drivability of this mode is at the highest.
And Boost Turbo timing can be used and get erupting power.、
Option 2: Sensored/Sensorless Hybrid
This is universal driving mode of current 1:8 power system. The ESC operates the motor in sensored mode during the low-speed start-up process, followed by switching to operating the motor
in the “sensorless” mode when the RPM is increased.
1I: Motor Rotation:
With the motor shaft faces you (the rear end of the motor is away from you), increase the throttle input, the motor (shaft) will rotate in the CCW/CW direction if the “Motor Rotation/Direction”
set to “CCW/CW”. Generally, the vehicle runs forward when the motor (shaft) rotates in the CCW direction. However, some vehicles only run forward when the motor rotates in the CW direction
due to the different chassis design. In that case, you only need to set the “Motor Rotation/Direction” to “CW”.
1J: Phase-AC Swap:
If the A/C wire of ESC connect to A/C wire of motor with crossed way (A wire of ESC connects to C wire of motor, C wire of ESC connects to A wire), set this item as Enable.
Warning! When #A/#B/#C wire of ESC connect to #A/#B/#C wire of motor correspondingly, do not Set to Enable. Otherwise it will damage the ESC and motor.
2A: Throttle Rate Control:
This item is used to control the throttle response. It can be adjustable from 1 to 30 (step: 1), the lower the throttle rate, the more the limit will be on the throttle response. A suitable rate can
help driver to control his vehicle properly during the starting-up process. Generally, you can set it to a high value to have a quick throttle response if you are proficient at throttle control.
2B: Throttle Curve:
The throttle curve parameter reconciles the position of the throttle trigger (in throttle zone) and the actual ESC throttle output. It is linear by default and we can change it to non-linear via
adjusting the throttle curve. For example, if adjust it to +EXP, the throttle output at the early stage will be higher (than the output when the curve is linear); if it is adjusted to –EXP, the throttle
output at the early stage will be lower (than the output when the curve is linear.
2C: Neutral Range:
As not all transmitters have the same stability at “neutral position”, please adjust this parameter as per your preference. You can adjust to a bigger value when this happens.
2D: Initial Throttle Force:
It also called as minimum throttle force. You can set it according to wheel tire and traction. If the ground is slippery, please set a small throttle force.
2E: Coast:
The RPM of the motor will be lowered gradually when throttle is reduced. The vehicle will not reduce speed abruptly when the throttle is reduced to return to the neutral position. The bigger
the value, the more the “COAST” will be felt. Example, COAST of 0 deactivates, and a COAST of 20% would be the maximum amount of COAST.
The advantages of COAST:
When a vehicle has a larger final drive ratio, the tendency of having a “drag” feel is higher. The “COAST” technology is to allow the car to roll (coast) even when the final drive ratio is high.
The Coast function brings better and smoother control feeling to racers. Some drivers will refer to this to the traditional brushed motors.
Note : The “Coast” will be void (even if you set it to any value besides 0) if the above “drag brake” is not “0%”.
2F: PWM Drive Frequency:
The acceleration will be more aggressive at the initial stage when the drive frequency is low; a higher drive frequency is smoother but this will create more heat to the ESC. If set this item to
“Customized”, then the PWM frequency can be adjusted to a variable value (which ranges from 2K to 32K) at any 0-100% throttle input, Please choose the frequencies as per the actual test
results of your vehicles.
2G: Softening Value:
It allows users to fine-tune the bottom end, change the driving feel, and maximize the driving efficiency at different track conditions. The higher the “Softening Value”, the milder the bottom
end. In Modified class, drivers often feel the power of the bottom end is too aggressive. Little throttle input usually brings too much power to the car and make it hard to control at the corners,
so HOBBYWING creates this softening function to solve the issue.
2H: Softening Range:
It's the range to which “Softening Value” starts and ends. For example, 0% to 30% will be generated when the user pre-programs the “Softening Range” at a value of 30%.
2I: RPM Limit:
It is used to set the max. RPM value of the motor. Set corresponding values according to the motor and competition rules.
3A: Drag Brake Force:
It is the braking power produced when releasing from full speed to neutral position. This is to simulate the slight braking effect of a neutral brushed motor while coasting.
3B: Max. Brake Force:
This ESC provides proportional braking function; the braking effect is decided by the position of the throttle trigger. It sets the percentage of available braking power when full brake is applied.
Large amount will shorten the braking time but it may damage your pinion and spur.
3C: Initial Brake Force:
It is also known as “minimum brake force”. It is the force when pushing throttle trigger from neutral zone to the initial brake position. To get a smoother braking effect, the default is
equal to
the drag brake.
3D: Brake Rate Control:
It’s adjustable from 1 to 20 (step: 1), the lower the brake rate, the more limit on the brake response. A suitable rate can aid the driver to brake his vehicle correctly. Generally, you can set
it to a high value to have a quick brake response.
3E: Brake Curve:
This item is used for regulating the relation between the throttle range in brake zone and the brake force. The default setting is linear. You can change it to non-linear via a LCD program
box and a PC (HOBBYWING USB LINK software needs to be installed on the PC.) for different braking effect.
3F: Brake Frequency:
The brake force will be larger if the frequency is low; you will get a smoother brake force when the value is higher. If set this item to “Customized”, then the brake frequency can be
adjusted to a variable value (which ranges from 0K to 16K) at any 0-100% throttle input, please choose the frequencies as per the actual test results of your vehicles.
4A: Boost Timing:
It is effective within the whole throttle range; it directly affects the car speed on straightaway and winding course. The ESC adjusts the timing dynamically as per the throttle amount in
the operation. The Boost Timing is not constant but variable.
5A: Turbo Timing:
This item is adjustable from 0 degree to 48 degrees, the corresponding turbo timing (you set) will initiate at full throttle. It’s usually activated on long straightaway and makes the motor
unleash its maximum potential.
5B: Turbo Delay:
When “TURBO DELAY” is set to “INSTANT”, the Turbo Timing will be activated right after the throttle trigger is moved to the full throttle position. When other value(s) is applied, you will
need to hold the throttle trigger at the full throttle position (as you set) till the Turbo Timing initiates.
5C: Turbo Increase Rate (deg / 0.1sec):
This item is used to define the “speed” at which Turbo Timing is released when the trigger condition is met. For example, “6 degs / 0.1sec” refers to the Turbo Timing of 6 degrees that
will be released in 0.1 second. Both the acceleration and heat is higher when the “Turbo increase rate” is of a larger value.
5D: Turbo Decrease Rate (deg/0.1sec):
After the Turbo Timing is activated and the trigger condition turns to not be met (i.e. vehicle slows down at the end of the straightaway and gets into a corner, full throttle turns to partial
throttle, the trigger condition for Turbo Timing turns to be not met), if you disable all the Turbo Timing in a moment, an obvious slow-down like braking will be felt and cause the control
of vehicle to become bad. If the ESC can disable the Turbo Timing at some “speed”, the slow-down will be linear and the control will be improved.
Warning! Boost Timing & Turbo Timing can effectively improve the motor efficiency; they are usually used in competitions. Please take some time to read this manual and
then set these two items carefully, monitor the ESC & motor temperatures when you have a trial run and then adjust the Timing and FDR accordingly as aggressive Timings
and FDR may cause your ESC or motor to be burnt.
Note: Parameters 5A-5D only has function when you set the “Drive Mode” to “Full Sensored”.
2E Coast 0-15 (Adjust Step 1)
Parameters
Type ID Item
For/RevFor/Rev/Brake
General SettingThrottle ControlBrake ControlTiming
1A Running Mode For/Brake
4 Cells2 Cells 3 Cells 6 Cells5 Cells1C LiPo Cells Auto Calculate
75%50%1B Reverse Force 25% 100%
CustomizedAuto (3.5V/Cell)1D Cutoff Voltage Disabled
10%8%2C Neutral Range 6%
4K3K
2F PWM Drive Frequency 2K
1G BEC Voltage 6.0-8.4V (Adjust Step 0.1V)
2A Throttle Rate Control 1-30 (Adjust Step 1)
2D Initial Throttle Force 1-15 (Adjust Step 1)
2G Softening Value 0-30° (Adjust Step 1°)
3A Drag Brake 0%-100% (Adjust Step 1%)
3C Initial Brake Force 0%-50% (Adjust Step 1%)= Drag Brake
3B Max. Brake Force 0%-100% (Adjust Step 1%)
4A Boost Timing 0-48° (Adjust Step 1°)
5A Turbo Timing 0-48° (Adjust Step 1°)
3D Brake Rate Control 1-20 (Adjust Step 1)
Disabled1E ESC Thermal Protection Enabled
Disabled1F Motor Thermal Protection Enabled
Sensored/Sensorless Hybrid1H Sensor Mode Full Sensored
Disabled1J Phase-AC Swap Enabled
CWMotor Rotation CCW
Customized2B Throttle Curve Linear
Customized3E Brake Curve Linear
1I
8K 12K 16K 24K 32K Customized
2K1K3F Brake Frequency 0.5K 4K 8K 16K
80000RPM
40000RPM (4Poles)
2I RPM Limit Unlimited 74000RPM
37000RPM (4Poles)
68000RPM
34000RPM (4Poles)
62000RPM
31000RPM (4Poles)
56000RPM
28000RPM (4Poles)
50000RPM
25000RPM (4Poles)
20%10%2H Softening Range 0% 25% 30% 35% 40% 45% 55% 60% 65% 70% 75%
0.1s0.05s
3deg/0.1s 6deg/0.1s 9deg/0.1s 12deg/0.1s 15deg/0.1s 18deg/0.1s 21deg/0.1s 24deg/0.1s 27deg/0.1s 30deg/0.1s
5B Turbo Delay 0.15s 0.2s 0.25s 0.35s 0.4s 0.45s 0.5s 0.6s 0.7s 0.8s 0.9s 1.0sInstant
5C Turbo Increase Rate (deg/0.1sec) Instant
Instant3deg/0.1s 6deg/0.1s 9deg/0.1s 12deg/0.1s 15deg/0.1s 18deg/0.1s 21deg/0.1s 24deg/0.1s 27deg/0.1s 30deg/0.1s5D Turbo Decrease Rate (deg/0.1sec)
Customized
Mode #
1
2
3
4
5
Modes/Profiles
Zero T iming
1/8 Off-Road
1/8 On-Road
1/8 GT
1/8 Sport
Applications
Applicable for various STOCK Racing that the ESC must use Zero Timing (Blinky Mode)
Applicable for 1/8 Off-Road / Truck Racing
Applicable 1/8 On-Road Racing
Applicable 1/8 GT Racing
Applicable for 1/8 Sport/Entertainment
Troubles SolutionsPossible Causes
1. The battery voltage was not output to the ESC.
2. The ESC switch was damaged.
3. The positive and negative pole of the ESC is
connected reversely.
The battery voltage is not within the normal range.
1. The ESC does not detect the throttle signal.
2. The neutral point of the ESC does not match
with the transmitter.
The rotation direction of this car frame is
different from mainstream
1. Some soldering between the motor and the ESC
was not good.
2. The ESC was damaged (some MOSFETS were burnt).
1. The receiver was influenced.
2. The ESC entered the LVC protection.
3. The ESC entered the thermal shutdown protection.
1.Check whether there is poor welding of power input gate and reweld it.
2. Replace the switch.
3.Reconnect as per right poles.
Check the battery voltage.
1 Check whether the throttle wire and the channel is plugged correctly, .
and whether the transmitter is turned on.
2. Move the throttle trigger to the neutral point and recalibrate the throttle range.
Set the rotation direction of the motor to “CW” direction.
1. Check all welding points and reweld if necessary.
2. Contact the dealer for repair.
1. Check all devices and try to find out all possible causes, and check the
transmitter’s battery voltage.
2. The RED LED keeps flashing indicating the LVC protection is activated,
please replace your pack.
3. The GREEN LED keeps flashing indicating the thermal protection is
activated, please let your ESC cool down before using it again.
1. Recalibrate the throttle neutral position. No LED on the ESC will come
on when the throttle trigger is at the neutral position.
2. Set the “Running Mode” to “Fwd/Rev with Brk “.
3. Contact the distributor for repair or other customer service.
1. Connect the LCD setting box with the correct interface
The motor cannot start and emit Bi-Bi-, Bi-Bi-,
with the green LED flashing (the interval between
the Bi-Bi- and Bi-Bi- is 1 seconds)
Power on and inspect LiPo(Green LED flashes N
times) Red LED flashes rapidly. The motor does
not rotate.
The LED isn’t on and the motor cannot start.
The fan doesn’t work.
The motor suddenly stopped or significantly
reduced the output in operation.
The motor stuttered but couldn’t start.
The vehicle could run forward (and brake),
but could not reverse.
Connect LCD parameter setting box, display
“CONNECTING ESC” all the time.
The vehicle ran backward when you pulled the
throttle trigger towards you.
1. The throttle neutral position on your transmitter
was actually in the braking zone.
2. Set the “Running Mode” improperly.
3. The ESC was damaged.
1.The programming port of ESC is used incorrectly.
1. Plug the throttle wire into the TH channel marked by the receiver.
2. Insert according to the sequence marked by the receiver.
Press SET key to set neutral point when setting the
throttle range, the green LED does not flash and
without “Bi” sound. Or cannot set the end point of
forward and backward after setting the neutral point.
1.The throttle wire of ESC is not plugged into the right
channel of receiver.
2.The throttle wire is connected reversely.
XERUN XR8 Plus G2S
USER MANUAL
Brushless Electronic Speed Controller
Battery
Electronic Speed Controller
Receiver Motor
Sensor port of motor
Sensor wire
AC
B

Produktspecifikationer
Varumärke: | Hobbywing |
Kategori: | Radiostyrda leksaker |
Modell: | XeRun XR8 Plus G2S |
Behöver du hjälp?
Om du behöver hjälp med Hobbywing XeRun XR8 Plus G2S ställ en fråga nedan och andra användare kommer att svara dig
Radiostyrda leksaker Hobbywing Manualer

28 Mars 2025

28 Mars 2025

27 Mars 2025

27 Mars 2025

27 Mars 2025

27 Mars 2025

27 Mars 2025

27 Mars 2025

27 Mars 2025

27 Mars 2025
Radiostyrda leksaker Manualer
- Radiostyrda leksaker ACME
- Radiostyrda leksaker MJX
- Radiostyrda leksaker Absima
- Radiostyrda leksaker Spektrum
- Radiostyrda leksaker Chicco
- Radiostyrda leksaker Overmax
- Radiostyrda leksaker Carson
- Radiostyrda leksaker Parrot
- Radiostyrda leksaker Velleman
- Radiostyrda leksaker Amewi
- Radiostyrda leksaker Proline
- Radiostyrda leksaker Biltema
- Radiostyrda leksaker TacTic
- Radiostyrda leksaker DJI
- Radiostyrda leksaker Little Tikes
- Radiostyrda leksaker Revell
- Radiostyrda leksaker Futaba
- Radiostyrda leksaker Conrad
- Radiostyrda leksaker Tamiya
- Radiostyrda leksaker Traxxas
- Radiostyrda leksaker ARRMA
- Radiostyrda leksaker Carrera
- Radiostyrda leksaker Spin Master
- Radiostyrda leksaker Graupner
- Radiostyrda leksaker Blade
- Radiostyrda leksaker ParkZone
- Radiostyrda leksaker JETI
- Radiostyrda leksaker Ninco
- Radiostyrda leksaker Multiplex
- Radiostyrda leksaker SkyRC
- Radiostyrda leksaker SAB
- Radiostyrda leksaker Ripmax
- Radiostyrda leksaker Maverick
- Radiostyrda leksaker Reely
- Radiostyrda leksaker Robbe
- Radiostyrda leksaker LRP
- Radiostyrda leksaker Lenoxx
- Radiostyrda leksaker Axial
- Radiostyrda leksaker Hangar 9
- Radiostyrda leksaker FMS
- Radiostyrda leksaker E-flite
- Radiostyrda leksaker Flyzone
- Radiostyrda leksaker XciteRC
- Radiostyrda leksaker FrSky
- Radiostyrda leksaker WLtoys
- Radiostyrda leksaker Force Engine
- Radiostyrda leksaker Sharper Image
- Radiostyrda leksaker Vaterra
- Radiostyrda leksaker Jada
- Radiostyrda leksaker HPI Racing
- Radiostyrda leksaker Kyosho
- Radiostyrda leksaker PowerBox Systems
- Radiostyrda leksaker Losi
- Radiostyrda leksaker Hobby Zone
- Radiostyrda leksaker JR
- Radiostyrda leksaker RC4WD
- Radiostyrda leksaker Sky Rider
- Radiostyrda leksaker DF-Models
- Radiostyrda leksaker ROCHOBBY
Nyaste Radiostyrda leksaker Manualer

28 Mars 2025

28 Mars 2025

27 Mars 2025

25 Februari 2025

7 Februari 2025

6 Februari 2025

6 Februari 2025

6 Februari 2025

8 Januari 2025

30 December 2025